Safety engineering, Safety engineering 7, 7safety engineering – Lenze MDFQA Operating Instructions User Manual
Page 36
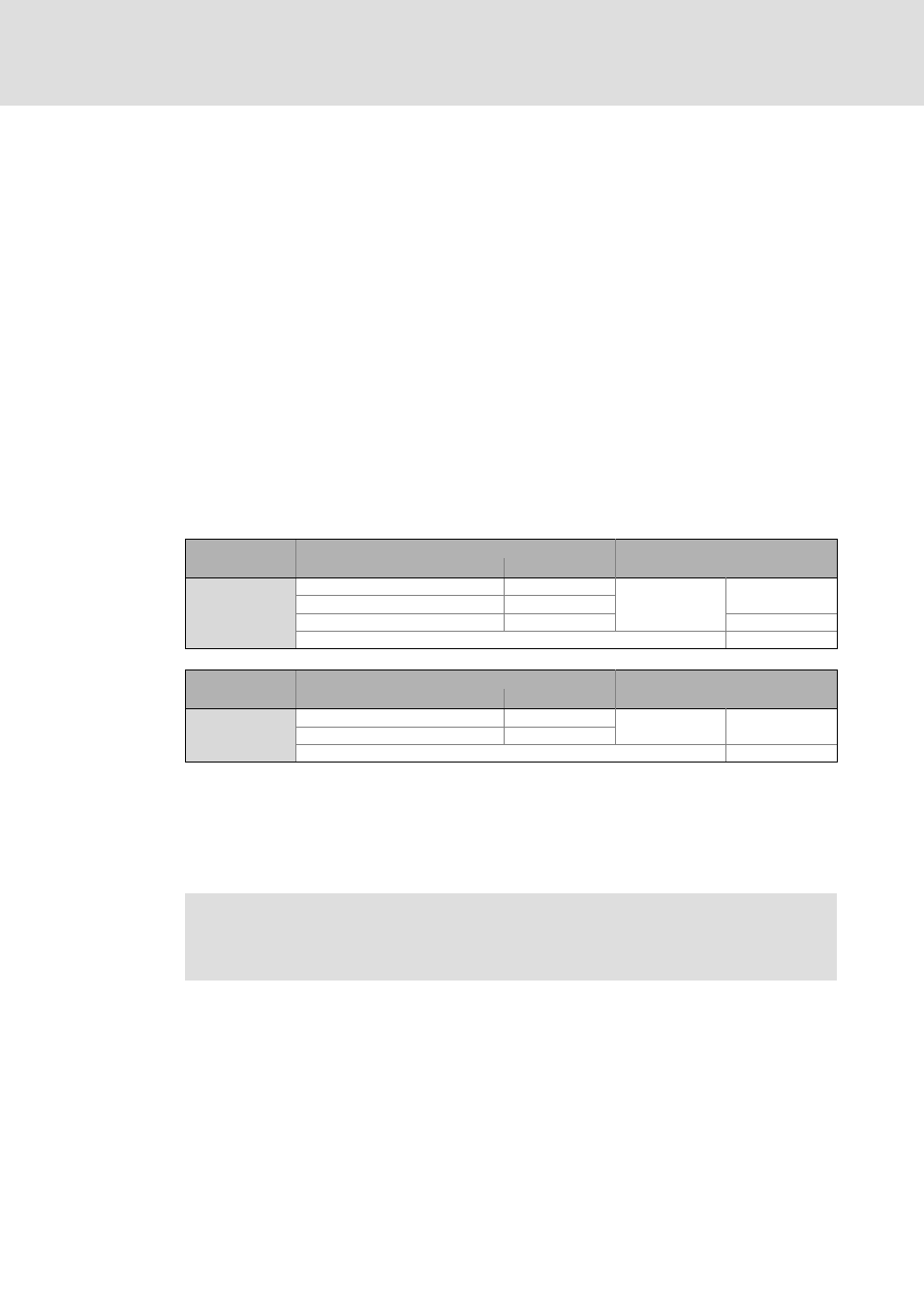
Safety engineering
7
Lenze
36
BA 33.0006 3.0
7
Safety engineering
Motor−encoder combinations
Drive systems with Servo Drives 9400 and safety module SM301 provide speed−dependent
safety functions for safe speed monitoring and/or safe relative−position monitoring.
Observe permissible motor−encoder combinations during configuration.
ƒ
Possible speed−dependent safety functions with safety module SM301:
– Safe stop 1 (SS1)
– Safe operational stop (SOS)
– Safely limited speed (SLS)
– Safe maximum speed (SMS)
– Safe direction (SDI)
– Safe speed monitor (SSM)
– Safely limited increment (SLI)
ƒ
Permissible motor−encoder combinations for these functions:
Synchronous
servo motors
Encoder
Safe speed monitoring with SM301
Type
Product key
MCS 06 ... 19
MDXKS 56 / 71
Sin/cos absolute value, single−turn
AS1024−8V−K2
Single−encoder
concept
PL d / SIL 2
Sin/cos absolute value, multi−turn
AM1024−8V−K2
Resolver
RV03
PL e / SIL 3
Two−encoder concept Up to PL e / SIL 3
Asynchronous
servo motors
Encoder
Safe speed monitoring with SM301
Type
Product key
MCA 10 ... 26
MQA 20 ... 26
Sin/cos incremental
IG1024−5V−V3
Single−encoder
concept
PL e / SIL 3
Resolver
RV03
Two−encoder concept Up to PL e / SIL 3
A "two−encoder concept" includes e.g. a resolver as motor encoder and, at the same time,
an absolute value encoder (sin/cos), an incremental encoder (TTL), or digital encoder
(SSI/bus) as position encoder on the machine.
In the case of the "2−encoder concept", the achievable risk mitigation (PL/SIL) depends on
the suitability of the encoders used.
)
Note!
If feedback systems for safety functions are used, the manufacturer’s
documentation must be observed!