Troubleshooting guide – Landoll 5211 Grain Drill User Manual
Page 74
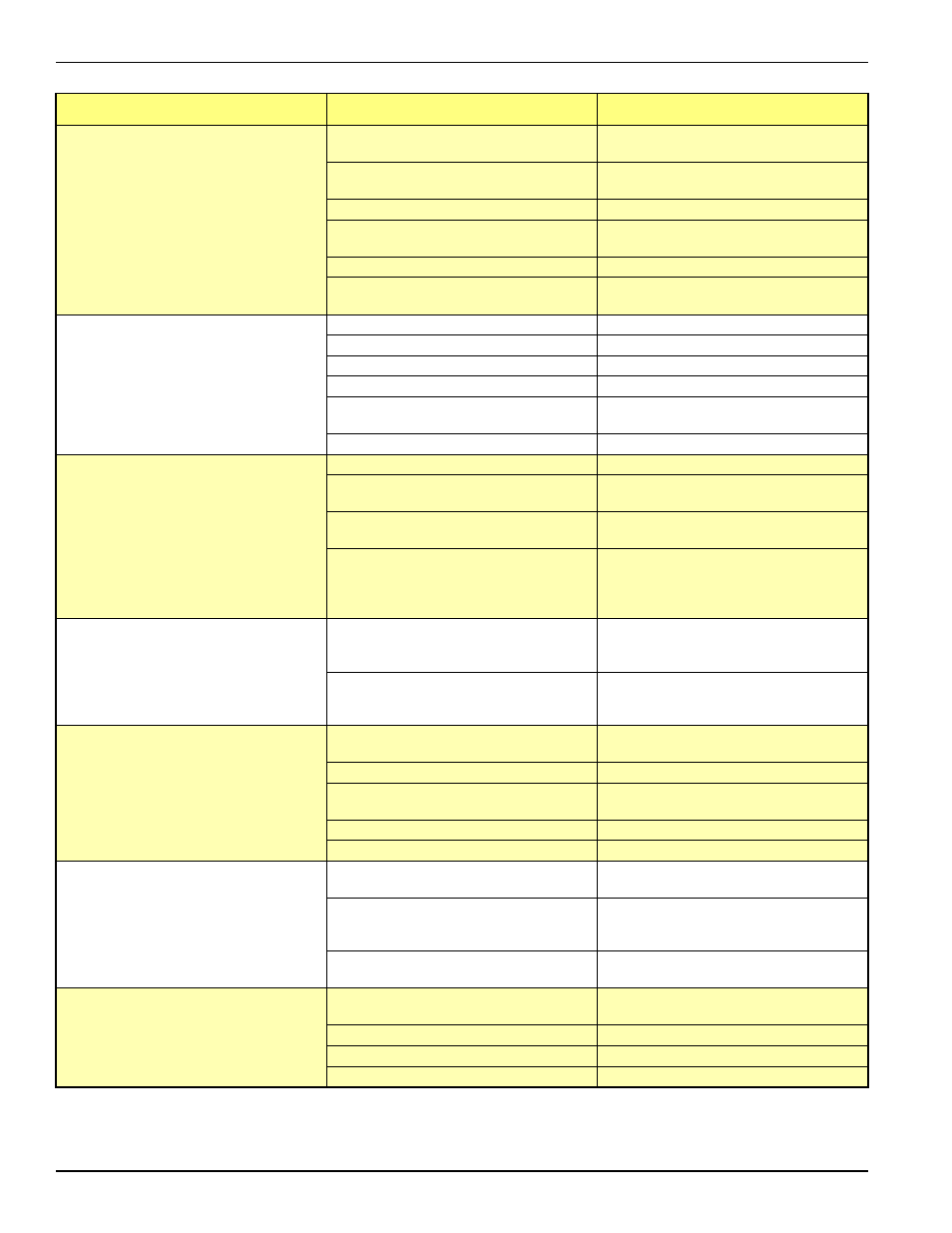
5-2
F-725-1213 Edition
TROUBLESHOOTING GUIDE
SECTIONS PLANTING AT DIFFERENT
RATES
Seed rate adjustment not the same on all
sections
Adjust seed rate.
Drive types (sprocket ratio) not the same
on all sections
Change to same drive type on all sections.
Seed meter out of adjustment
Reset seed meters.
Seed rate adjustment handle out of
adjustment
Reset seed rate adjustment handle.
Opener seed tube plugged
Clean out seed tube.
Broken seed meter
Allows excessive seeding - repair seed
meter.
UNEVEN SEED SPACING
Excessive field speed
Reduce field speed.
Unclean seed
Use clean seed
Build up of seed treatment in seed cup
Clean out seed meters
Seed tubes sagging
Replace seed tube
Drive type (sprocket ratio) too slow
Use faster drive type and readjust seed
meter opening.
Plugged opener seed tube
Clean out bottom of seed tube.
OPENER DISCS NOT TURNING FREELY
Opener plugged with mud/dirt
Clean opener.
Scraper set too tight
Adjust scraper (See “Opener Scraper
Soil control strip set too tight against
opener blades
Adjust soil strip
Soil strip plugged with residue
Adjust soil strip closer to blade, move
metal backing strip away from edge of
soil strip (See “Opener Soil Strip
Adjustment” on page 4-28.)
PRESS WHEELS NOT COMPACTING
THE SOIL AS DESIRED
Opener down pressure set too low
Increase air system pressure on row units
(See “Air System Pressure” on
page 4-9.)
Incorrect press wheel depth adjustment
Reset press wheel depth adjustment (See
“Opener – Press Wheel Adjustment”
on page 4-26.)
PRESS WHEEL OR OPENERS
PLUGGING
Backed up with openers in the ground
Clean out opener and press wheels and
check for damage.
Scraper worn or not adjusted correctly
Replace or adjust scraper
Opener blades worn, pinch point too wide
Reset pinch point, replace worn out
blades.
Planting conditions too wet
Wait until drier weather
Opener bearing failure
Replace opener bearings
AIR SPRING LEAKING AIR
Air spring not set all the way forward or
backward in adjustment slots
Replace and reposition air spring
Operating with too low air pressure
Minimum air system pressure is 15 psi
(See “Air System Pressure” on
page 4-9.)
Broken air spring stud
Replace air spring, maximum stud torque
30 ft-lbs.
AIR SYSTEM LEAK - FAST
Broken or pinched air line
Check hitch and wing hinge areas for
broken or pinched air line.
Broken fitting
Repair fitting
Air line disconnected
Reconnect air line.
Air spring has hole
Replace air spring.
PROBLEM
PROBABLE CAUSE
SOLUTION