Mechanical installation, Electrical connections, Electrical connections – 0-10 vdc input – NOVUS TxIsoRail 4-20 mA User Manual
Page 2
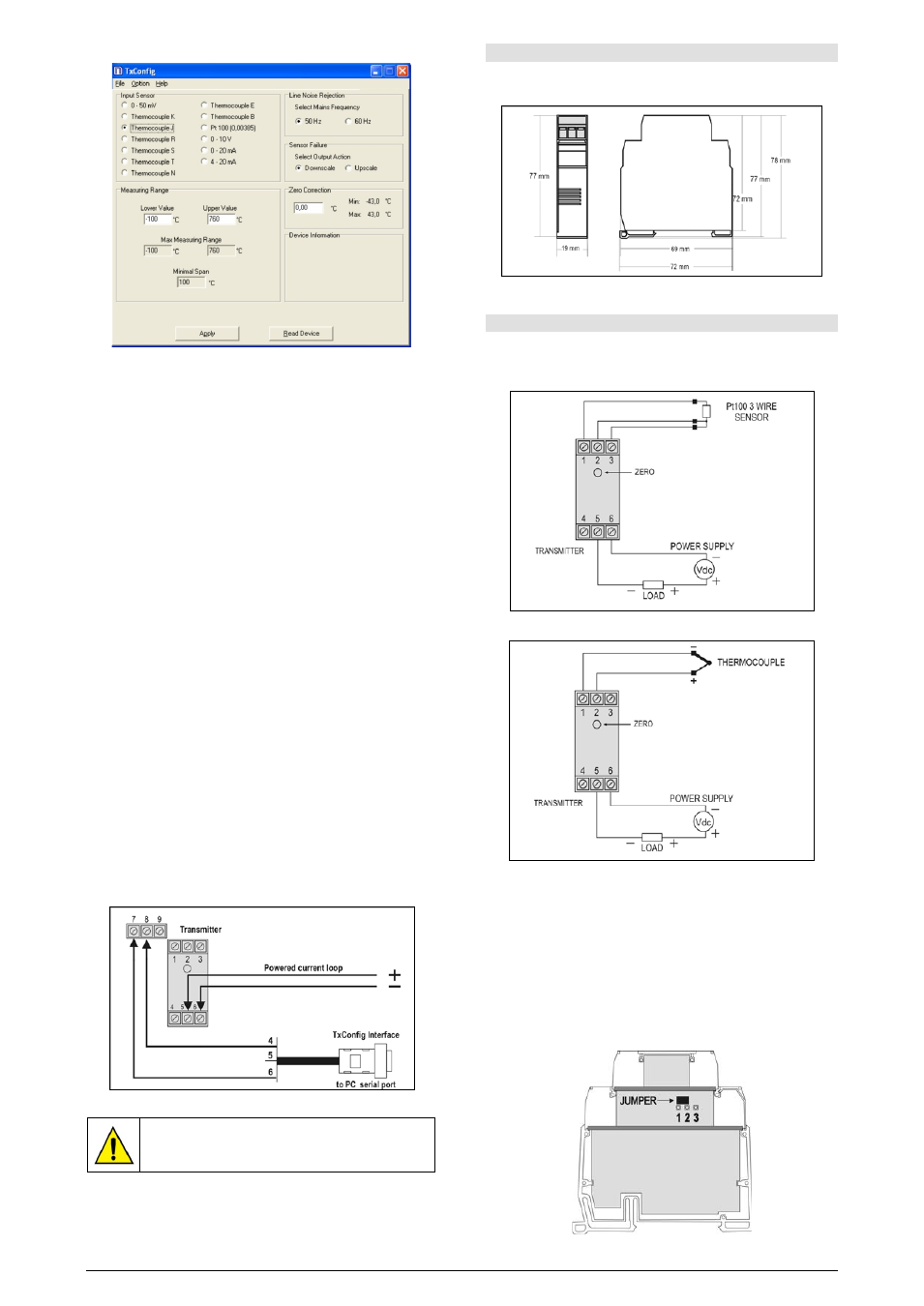
NOVUS AUTOMATION
2/3
The TxConfig screen in shown in Fig 3.
Fig. 3 – TxConfig main screen
The fields in the screen mean:
1. Input Sensor: Choose the desired temperature sensor among the
available options. See Table 1.
2. Measuring Range: Defines the beginning and the end of the range.
When the Low Scale Limit is configured with a value higher than the Full
Scale Limit, the current output will have a decrescent behavior (20~4
mA).
The values configured in these fields can not be beyond the sensor
measuring range. The minimum span value has to be observed as well
(see Table 01).
3. Line Noise Rejection: The transmitter incorporates a digital filter to
cancel the induced noise from the 50 or 60 Hz systems. For better
performance, select the line frequency used in your country.
4. Sensor Failure: establishes the transmitter output behavior (upscale or
down-scale) in the presence of a sensor fail.
5. Zero Correction: Allows for small sensor corrections.
6. Device Information: The Device Information box contains relevant data
concerning a particular transmitter. Please pass along this information
when contacting the technical assistance department.
7. Apply: Sends a new configuration to the transmitter.
8. Read Device: Brings to the screen the current transmitter parameters
configuration.
Note: The factory default configuration is (unless otherwise specified or
ordered):
Pt100 input, 0 to 100 ºC
60 Hz filtering and upscale (20 mA) output for sensor fail.
The transmitter must be powered in order to be configured. The TxConfig-USB
interface provides the necessary power. The TxConfig-RS232 interface,
however, requires an auxiliary supply to guarantee a reliable communication
with the computer.
An external 9 V battery can be used for this purpose (Fig. 1). An alternative is
to configure the transmitter while it is in operation; this way, the needed energy
is supplied by the current loop, as in Fig. 4.
Fig. 4 – TxConfig Interface connections – Loop powered
The TxConfig interfaces contain dedicated circuitry for proper
communication between transmitters and computer. Always make
use of the TxConfig interfaces for configuration purposes, otherwise
the transmitters may get damaged, voiding the warranty.
MECHANICAL INSTALLATION
The transmitter is intended for DIN rail mounting. Its drawing is presented in
Fig. 04.
Fig. 4 – Transmitter dimensions
ELECTRICAL CONNECTIONS
Figure below shows the transmitter connections to the sensor and power
supply. Terminals 1, 2 e 3 are used for sensor input. For 2-wire Pt100,
terminals 2 and 3 shall be connected together.
Fig. 5 – Transmitter wiring (Pt100)
Fig. 6 – Transmitter wiring (Thermocouple)
The LOAD represents the input shunt of an instrument measuring the 4-20
current loop.
Electrical Connections – 0-10 Vdc Input
For 0-10 Vdc input, the transmitter requires an internal hardware
configuration change. Please open the instrument case and change the
jumper shown in Fig. 07.
• Position 1-2 : 0-10 Vdc input
• Position 2-3 : all other input types
Fig. 7 – Jumper position for 0-10 Vdc input