Successive repetitions of a program, Determination of pid parameters, Alarms functions – NOVUS Controller N960 User Manual
Page 5: Problems with the controller
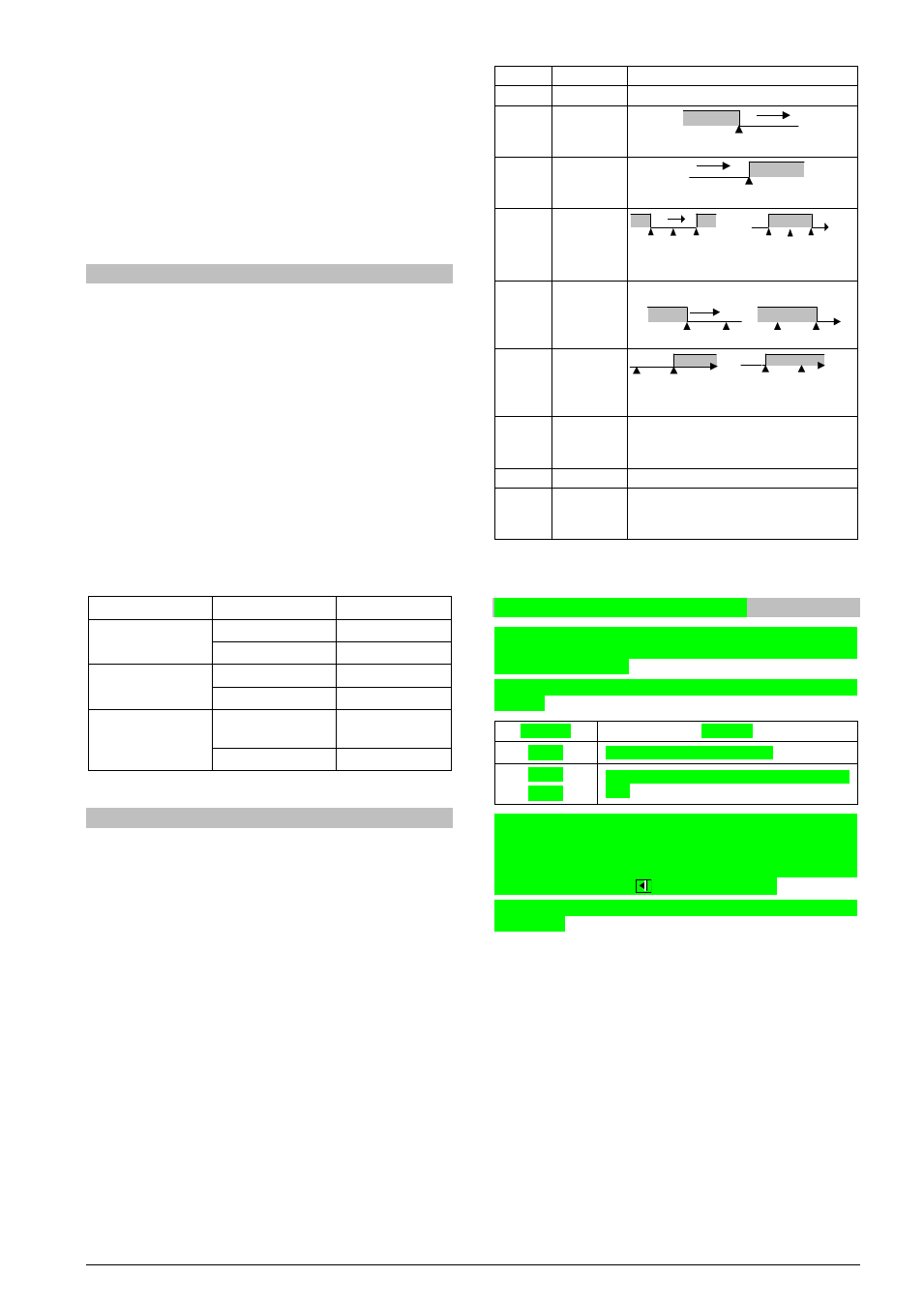
N960 Controller
NOVUS AUTOMATION
5/6
SUCCESSIVE REPETITIONS OF A PROGRAM
The elaborated program can be repeated several times, always
restarting immediately after each execution.
The rPt.p (rePeat Program) parameter, in the Program cycle,
configures the number of times the program must be REPEATED. It
determines the number of executions beyond the initial execution.
With zero (0), the program is executed only one time. It will not be
repeated.
Important: After the last execution of the program, all controller outputs
are turned off and the RUN parameter changes to OFF.
DETERMINATION OF PID PARAMETERS
During the automatic tuning the process is controlled in ON / OFF
mode in the programmed SP - the Ramp to Level function is disabled.
The automatic tuning may take many minutes to the concluded,
particularly in slow processes. Some recommendations for the
automatic tuning process are:
• Program SP to a value close to the point at which the process
will operate after tuning.
• Enable automatic tuning on the “Atvn” screen by selecting
yes
.
• Program the value yes on the “rvn” screen.
The “TUNE” indicator on the display stays lit until the completion of the
automatic tuning process.
During the execution of automatic tuning, large oscillations can be
induced in the process around the set point. Check if the process
supports these oscillations.
If the automatic tuning does not result in a satisfactory control, refer to
Table 3 for guidelines on how to correct the behavior of the process.
PARAMETER
VERIFIED PROBLEM
SOLUTION
Proportional Band
Slow answer
Decrease
Great oscillation
Increase
Rate of Integration
Slow answer
Increase
Great oscillation
Decrease
Derivative Time
Slow answer or
instability
Decrease
Great oscillation
Increase
Table 3 - Guidance for manual adjustment of the PID parameters
ALARMS FUNCTIONS
The minimum and maximum alarms are used to signalize extreme
temperature values. These extreme values are defined on the “A1SP”
and “A2SP” screens.
Differential alarms are used to signalize deviations between temperature
and set point control (SP). Values defined by user on the “A1SP” and
“A2SP” screens represent the values of these deviations.
Initial blocking prevents alarm activation when the controller is turned
on until the temperature reaches the SP value for the first time.
The error alarm in the sensor allows to signalize errors in the sensor.
The Level End Function (End.t) determines that the alarm be activated
the end of the level.
With Event Alarm, an alarm is activated during execution of a certain
program segment.
Table 4 illustrates the operation of each alarm function, using alarm 1
as an example, and presents its identification code on the “A1Fv” e
“A2Fv” screens.
Using the Alarm 1 as example.
PROMPT
TYPE
ACTION
Off
Disabled
Output is not used as alarm.
Lo
Minimum
value
(Low)
SPAn
PV
ON
Ki
Maximum
value
(High)
SPAn
PV
ON
Dif
Differential
(diFerential)
SV
PV
SV + SPAn
SV - SPAn
ON
ON
SV
PV
SV - SPAn
SV + SPAn
ON
Positive SPAn
Negative SPAn
Difl
Minimum
Differential
(diFerential
Low)
SPAn positivo SPAn negativo
SV
PV
SV - SPAn
ON
SV
PV
SV - SPAn
ON
Difk
Maximum
Differential
(diFerential
High)
SV
P
SV + SPAn
ON
SV
PV
SV + SPAn
ON
Positive SPAn
Negative SPAn
Ierr
Sensor Break
(input Error)
Activated when the input signal of PV is
interrupted, out of the range limits or
Pt100 in short-circuit.
End.T
End of Level Activate at the end of the level time.
Rs
Event
(ramp and
Soak)
Can be activated at a specific segment of
program.
Table 4 – Alarm functions
Where SPAn refers to Setpoints of Alarm SPA1 and SPA2.
PROBLEMS WITH THE CONTROLLER
Connection errors and inadequate programming are the most common
errors found during the controller operation. A final review may avoid
loss of time and damages.
The controller displays some messages to help the user identify
problems.
MESSAGE
PROBLEM
----
Open input. Without sensor or signal.
Err1
Err6
Configuration or connection problem in the Pt100
cable
Other error messages displayed by the controller can account for errors in
the input connections or type of selected input non compliant with the
sensor or signal applied to the input. If errors persist, even after a review,
contact the manufacturer. Inform also the device serial number. To find
out the serial number, press
for more than 3 seconds.
This information is necessary for eventual contact with the controller’s
manufacturer.