ROTHENBERGER ROWELD ROFUSE Print Plus V2.0 User Manual
Page 25
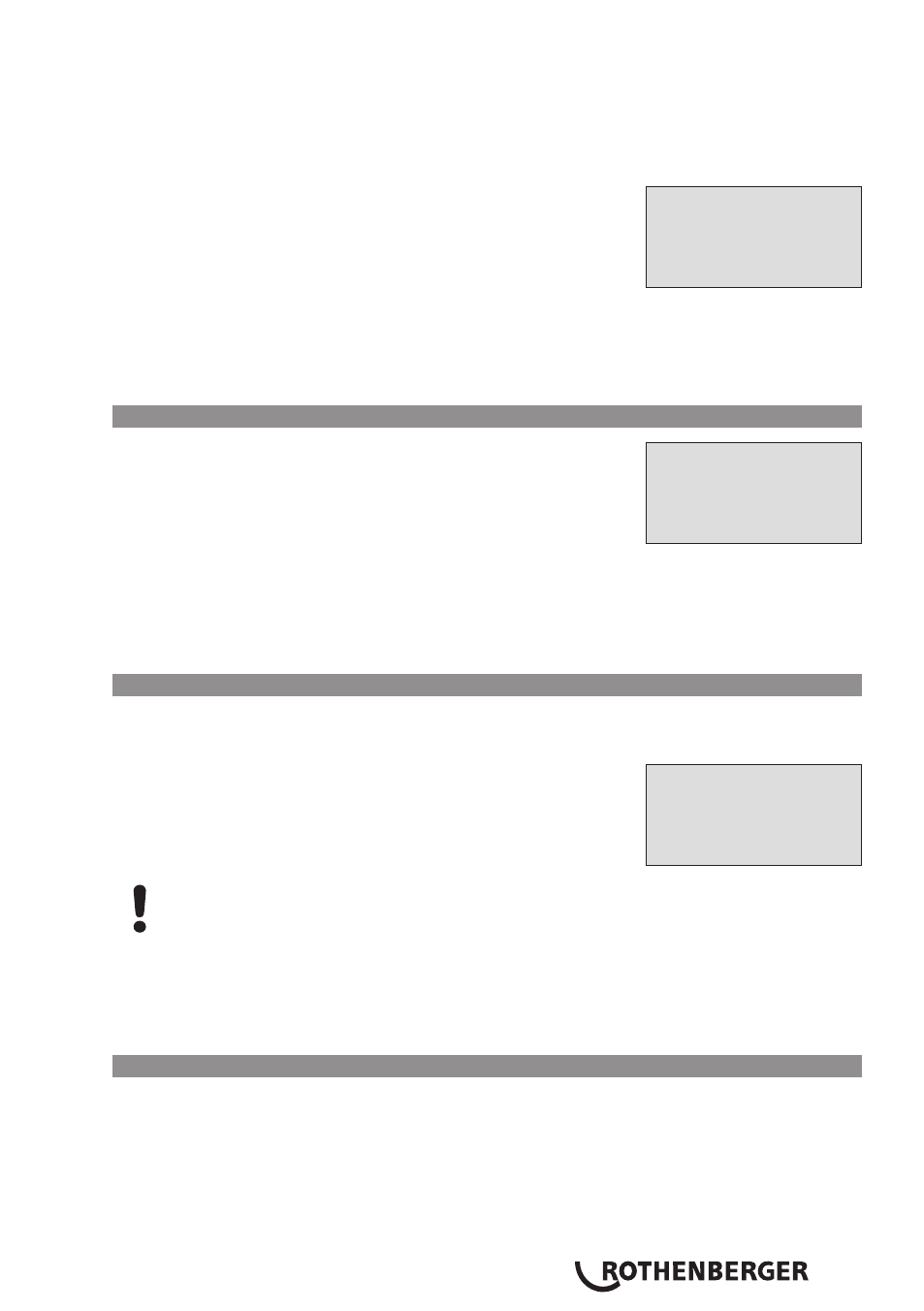
ENGLISH
23
The welding unit can be configured to ask for the welder identification code before the fitting
code is entered. The display screen then shows the message “Enter Welder Code.” (Later this
screen can be accessed by a quick access routine; see Sect. 6.1.) The numeric code can be entered
either by reading it from a tag with the scanner or by using the п, р, с, т keys. Whether the
welder identification code has to be entered and if so, when or how often, is determined in the
“Settings” sub-menu of the configuration menu (see Sect. 10.1).
When the welder code is read from a bar code using the scanner, an
Display 2
Enter Fitting Code
14:32:11 21.10.12
Inp.Volt. 230V 50Hz
No Contact
audible signal confirms this and the screen shows the read code and
switches to the next input display. When the code is entered
manually, it is saved by pressing the START/SET key. If the code
entered is not correct, a “Code Error” message appears; check the
sequence of numbers and correct as needed. If the code entered is
correct, it is saved to system memory and inserted into the welding
reports to be printed.
Only an ISO standard-compliant welder identification code is accepted by the unit. If the welder
code feature is disabled, the input screen for the welder code will not show.
5.3
Connecting the Fitting
Connect the connection terminals to the fitting and check for proper
Display 3
** Welder Code **
********************
**********
contact. Use terminal adapters if needed. The contact surfaces of the
cable connection terminals or adapters and the fitting have to be
clean. Dirty terminals may lead to improper welding and also to
overheated and fused connection terminals. Protect the cable
connectors against getting dirty at all times. Terminals and push-on
adapters should be considered consumables and, therefore, have to
be checked before every welding operation and replaced if damaged
or dirty.
When the fitting is connected, instead of the “No Contact” message (see Display 2) the number
of the next welding report appears, e.g., “Prot. No.: 0015.”.
5.4
Reading the Fitting Code with a Handheld Scanner
Only the bar code on the tag sticking on the fitting to be welded may be used. It is not acceptable
to read the fitting code tag of a fitting of a different kind if the intended one is damaged or
unreadable.
Read the fitting code by holding the scanner in front of the bar code
Display 4
Start ?
Temp.: 20°C
HST 315mm 58s
SAT 40.00V 0.80Ω
at a distance of 5 to 10 cm (2 to 4 inches), where the red line
indicates the reading area. Then push the reading button. If the data
are correctly read, the welding unit confirms this by an audible signal
and displays the decoded data on the screen (see Display 4).
The displayed values are the nominal welding parameters
contained in the fitting bar code. They are displayed before the actual resistance of
the electrofusion fitting is measured. This means that even when the showing ohm
value is o.k., a resistance error may still be detected (see Sect. 9.2). Only when the
welding process starts, the display shows the actual, measured welding parameters.
The “Start ?” message means that the unit is ready to start the welding process. Check the read
data and if you see that they are erroneous, delete them by pressing the STOP/RESET key. The
read data are also deleted if the welding unit is disconnected from the fitting.
5.5
Direct Welding with the AutoWeld Feature
If two welding operations with electrofusion fittings with the exact same welding parameters
succeed each other, it is not necessary to read a fitting bar code or enter welding parameters
manually. To start a welding operation that is fully identical to the preceding one, it is sufficient to
use the AutoWeld feature, provided it was enabled in the configuration menu (see Sect. 10.1). It
is accessible from thre quick selection screen opened from the “Enter Fitting Code” screen with
the ï arrow key (see Sect. 6.1). In this screen, the selection cursor can be moved using the ñ and
ò
; the selection is made with the START/SET key.