Maintenance, Disassembly and assembly of the chuck, Spare parts – ROHM DURO-NC - Power chucks with quick-acting jaw change system User Manual
Page 13: 1 determing the clamping force
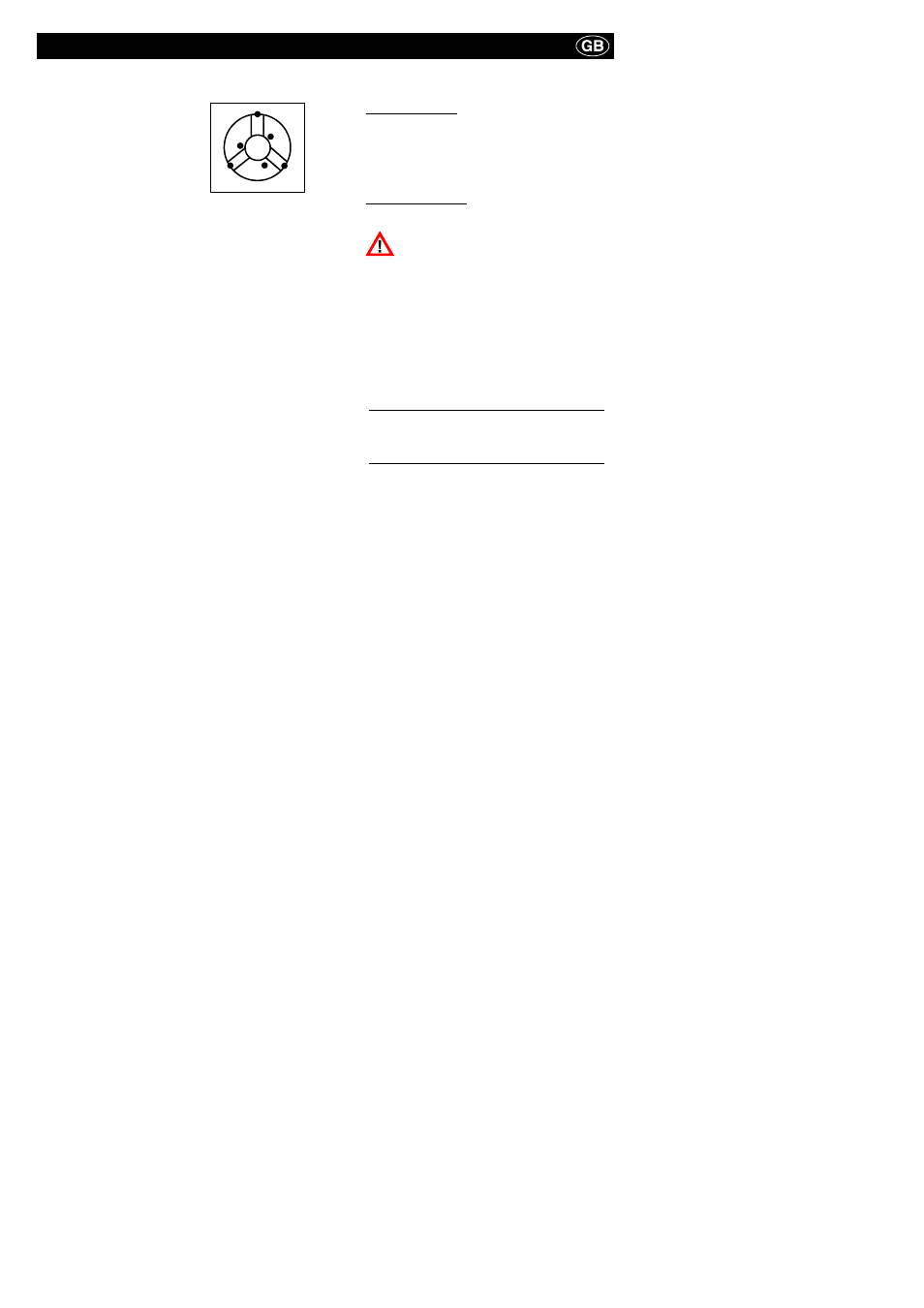
4. Maintenance
1. To maintain its reliability
and high quality, the chuck
must be lubricated at the
grease nipples at regular in-
tervals (see illustration).
After lubrication, move the
clamping piston several ti-
mes over its full stroke in or-
der to distribute the grease
more evenly.
Then lubricate again.
2. Performance and clamping force must be checked after
some time, depending on the conditions of use. The most
reliable method of measuring the clamping force is by
means of a load cell.
3. Performance check: The clamping piston must move
when the lowest possible actuating pressure of 3-4 bar is
applied. However, this method is not reliable enough to
serve as a substitute for the clamping force measure-
ment.
If the clamping force has dropped substantially or if the
clamping piston can no longer be moved with ease, the
chuck must be disassembled, cleaned and relubricated.
4. Maintenance intervals: Depending on the conditions of
use, but not later than after the specified periods.
We recommend our special grease F 80.
Lubricate all lubricating points
every 20 hours of operation
heavy soling every 8 hours.
Disassemble the chuck and clean all parts
every 2000-3000 hours of operation.
5. Disassembly and assembly of the chuck
1. Remove jaws 18 from chuck (see ”Changing the jaws”).
2. Unscrew cover plates 5 and 6 from guide jaws 2.
3. Unscrew base of chuck body (provided with jacking
screw threads).
4. Remove adjusting ring 8.
5. Remove piston 3 together with guide jaws 2.
6. Unscrew adjusting screw (laterally of the guide jaw)
and push out rack 4.
7. If spring bolt resists movement, it can be removed by
unscrewing the screw plug.
8. Remove rotary bolt from bore after unscrewing the pin.
9. To reassemble the chuck reverse the above procedure
Important:
Make sure that the adjusting screw does not block the
rack 4. To avoid this, bring the adjusting ring 8 into a sui-
table position.
6. Spare parts
When ordering spare parts, please quote the Ident. No. of the chuck and the item number or designation of the desired part
(see page 3). -- The Ident. No. will be found on the face of the chuck.
7. Calculating the clamping force and speed of rotation
7.1 Determing the clamping force
The clamping force F
sp
of a rotary chuck is the total of all
jaw forces acting radially on the workpiece. The clamping
force applied before the cutting process and with the
chuck stationary is the initial clamping force F
spo
. The
clamping force F
sp
avialable during the cutting process is,
firstly, the initial clamping force F
spo
existing with the
chuck stationary. This force is then increased or decrea-
sed by the centrifugal force F
c
on the jaws.
F
sp
= F
spo
F
c
[N]
(1)
The (--) sign is for clamping forces applied from the
outside in.
The (+) sign is for clamping forces applied from the
inside out.
The clamping force F
sp
avialable during the cutting
process multiplied by safety factor S
z
²
1,5.
The size of this factor is determined by the accuracy of the
influence parameters such as loading, clamping coeffi-
cient, etc.
F
sp
= F
spz
.
S
z
[N]
(2)
A safety factor of S
p
²
1,5 should be taken into
consideration for the static initial clamping force F
spo
.
Consequently, the following applies for the clamping force
with the chuck stationary.
F
spo
= S
sp
.
(F
sp
F
c
)
[N]
(3)
The (--) sign is for clamping forces applied from the
outside in.
The (+) sign is for clamping forces applied from the
inside out.