Storage, preparation, installation – NORD Drivesystems B2000 User Manual
Page 23
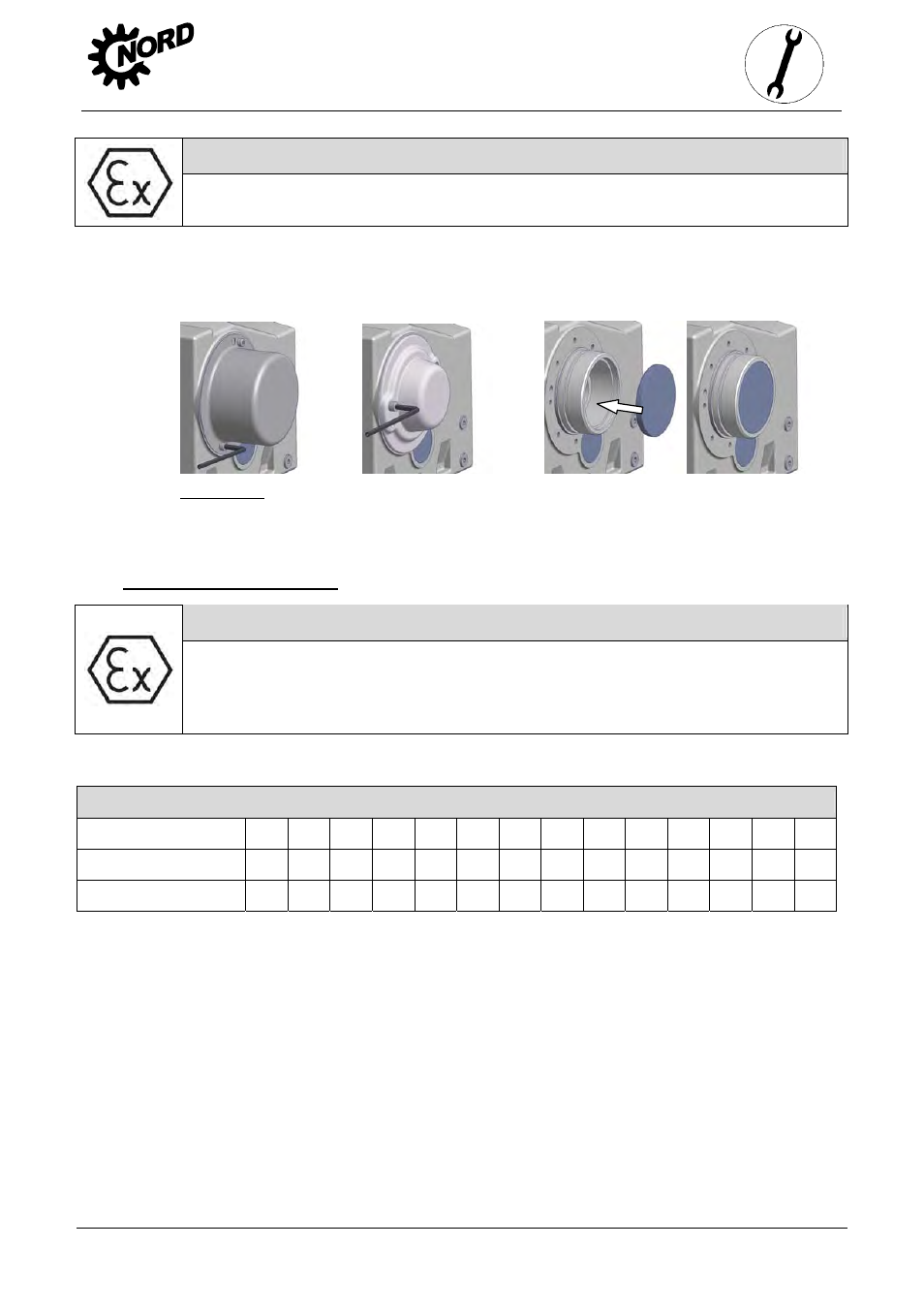
3. Storage, preparation,
installation
www.nord.com B2000-GB-0413
-23-
All fixing screws must be used and coated prior to use with a securing lubricant e.g. Loctite 242,
Loxeal 54-03 and tightened to the correct torque. (See Section 6.3 for torque values) For covers
with option H66, press in the new / new condition closing cap by tapping it lightly with a hammer.
Figure 3-13: Fitting the covers, Option SH, Option H, and Option H66
3.12 Fitting a standard motor
The maximum permitted motor weights indicated in the table below must not be exceeded:
Maximum permitted motor weights
IEC motor size
63
71
80
90
100
112
132
160
180
200 225 250 280
315
NEMA Motor size
56C 143T 145T 182T 184T 210T 250T 280T 324T 326T 365T
Max. motor weight [kg]
25
30
40
50
60
80
100
200
250
350 500 700 1000 1500
Assembly procedure to attach a standard motor to the IEC adapter (Option IEC)/NEMA adapter
1. Clean motor shaft and flange surfaces of motor and adapter and check for damage.
Mounting dimensions and tolerances of the motor must conform to DIN EN 50347/NEMA
MG1 Part 4.
2. Push the coupling sleeve onto the motor shaft so that the motor parallel key engages into
the groove in the sleeve on tightening.
3. Tighten the coupling sleeve on the motor shaft in accordance with the motor manufacturer’s
instructions until it touches the collar. With motor sizes 90, 160, 180 and 225, any spacer
bushes must be positioned between the coupling sleeve and the collar. With standard helical
gear units, dimension B between the coupling sleeve and the collar must be observed (see
Figure 3-14). Certain NEMA adapters require the adjustment of the coupling in accordance
with the specifications indicated on the adhesive plate.
Danger!
Covers must be inspected for transportation damage e.g. dents and warping before
they are fitted. Damaged covers must not be used, as they may cause rubbing.
Danger!
Only standard motors with an adequate ATEX Zone category according to the rating
plate may be used. In addition, for ATEX category 2D gear units (see the ATEX labelling
on the last line of the gear unit rating plate), the motor must have at least protection
class IP6x.