Operation of self tune® function, Theory of operation – Dwyer 1600 User Manual
Page 11
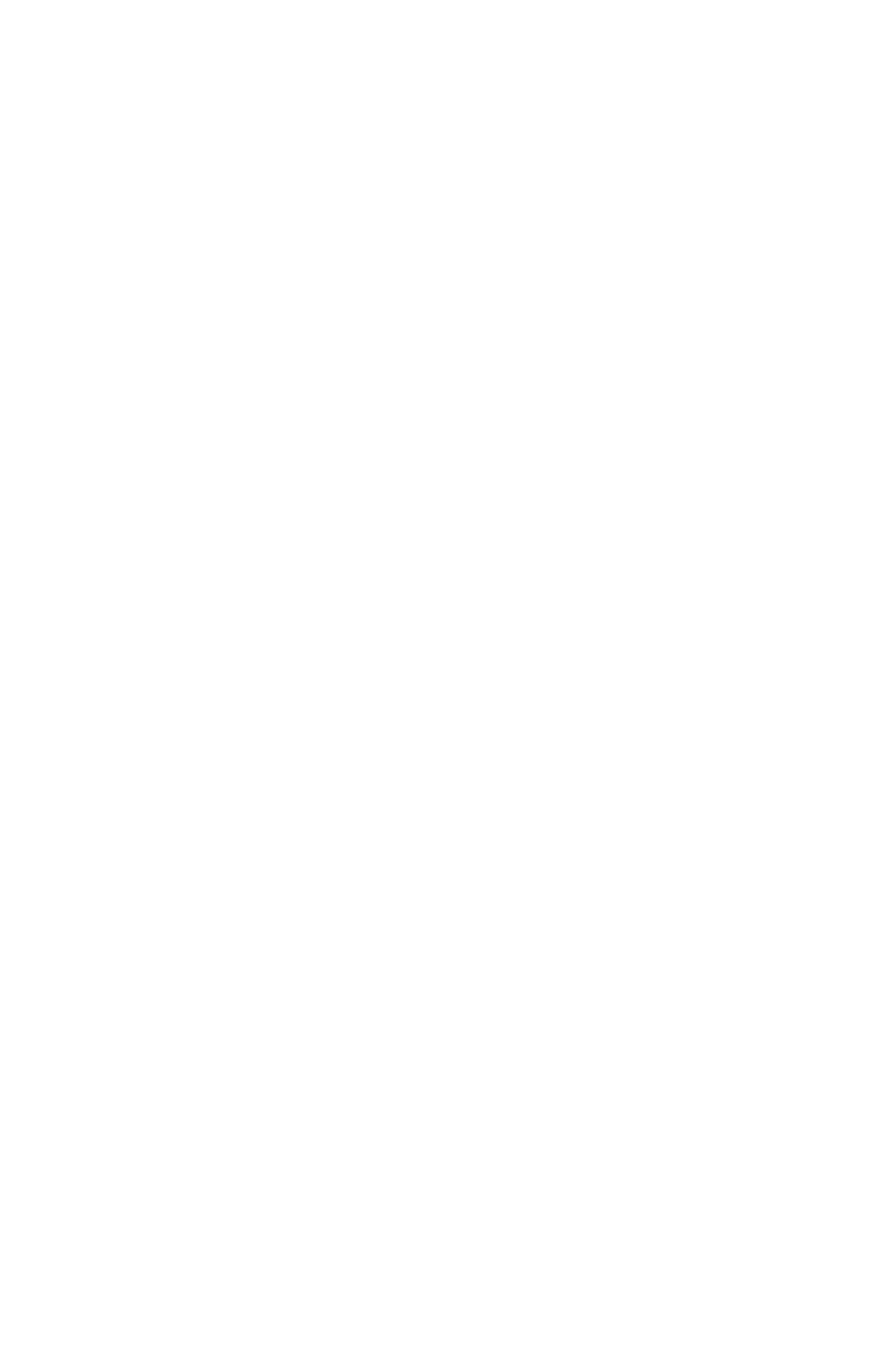
Rev. 10/98
11
949-1239-3
The partial status display sequences with the set value showing the ramp
(S1rA) or soak (S1So) segment being processed at that moment. It will also
show the Program output status if at Hold or OoFF.
When StAt is selected On, the HOME Display alternately indicates the
normal HOME and the Ramp/Soak full status in both the upper and lower
displays. The full status display sequences with the set value; Program run,
Hold, or OoFF; and with the time remaining for the ramp S1rA or the soak
S1So segments.See Programming and Operation for Ramp/Soak Feature
below for more information.
If PctO (Secondary Menu) is turned On, the lower display changes to show
the active percentage of output as required to maintain SP1. The display
is similar to the Auto/Manual display above, except that the letter indicators
do not flash, and the output is displayed in whole percentages of output, not
in tenths of a percent. If the control has both SP1 and SP2, the lower display
will alternate between the SP1 percent output and the SP2 percent output.
OPERATION OF SELF TUNE® FUNCTION
Self Tune® allows automatic selection of the necessary parameters to
achieve best control operation from your 1600 Series control. If you are
using the control output as a simple on-off function (S#Ot set for OnOF),
none of the following will apply.
Theory of Operation
The Self Tune function calculates the Pb1, rES, and rtE parameters under
the PID tunE selection as shown in the Secondary Menu . These values are
determined by measuring the response of the process connected to the
control. When Self Tune is started, the control temporarily acts as an on-
off control. While in this mode the control measures the overshoot and
undershoot of the process, and the period of the process (the time from peak
value to the next peak value). These measurements are collected over a
period that lasts three periods of overshoot and undershoot. The data
collected over this time is then compared and calculated into final PID
values. The calculations for the PID values are the same as used in the
standard Ziegler - Nichols equations that have been recognized as standard
for decades.
The only modification to the application of the Ziegler - Nichols equations is
controlled by the dFAC menu item. This menu item controls the amount of
rate (derivative) that is applied. A dFAC setting of 3 (factory default) or less
allows for less damping. A dFAC setting of 4 allows for critical damping as