Troubleshooting, Caution – Lincoln Electric IM10071 MAGNUM PRO THRU THE ARM ROBOTIC TORCH User Manual
Page 25
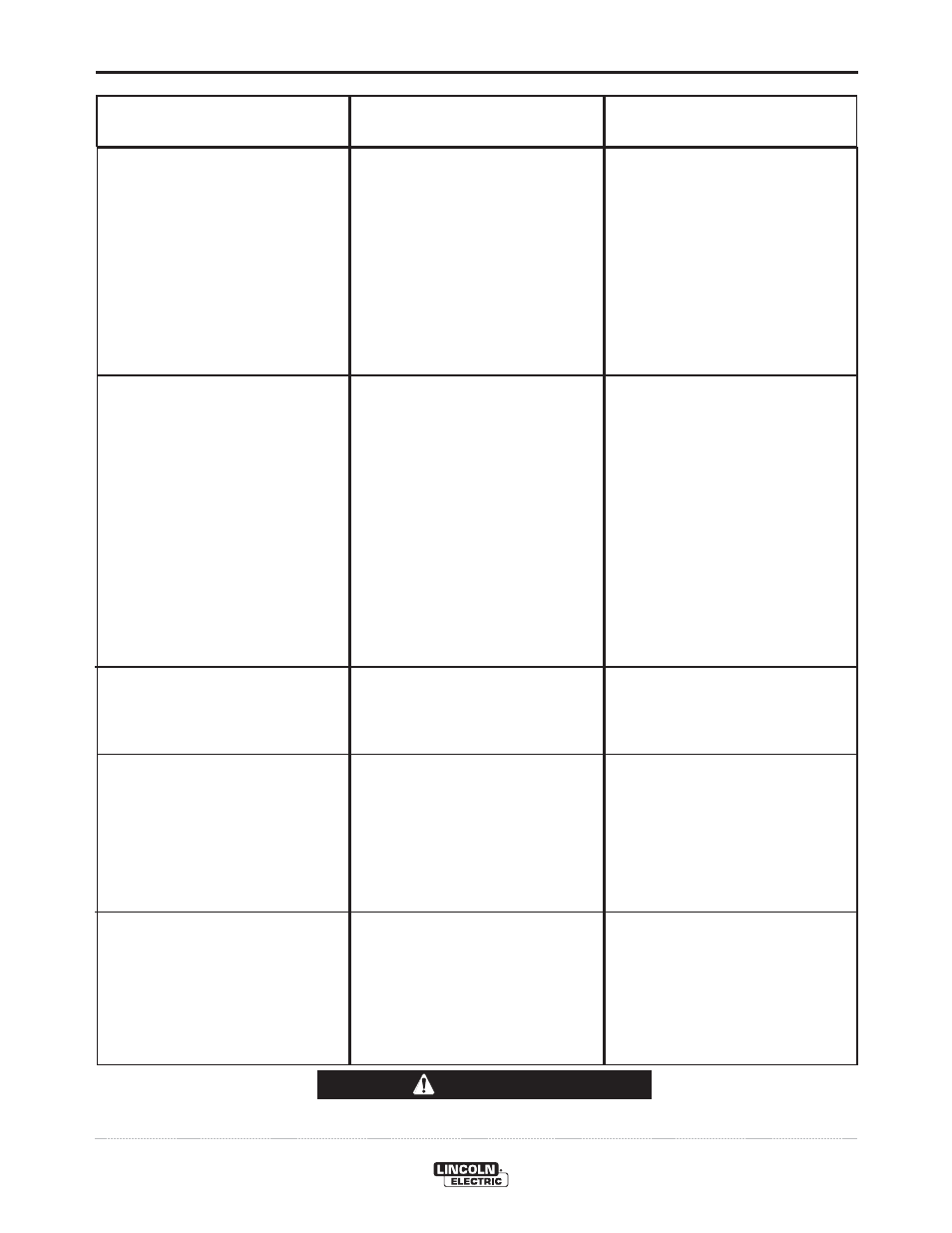
E-2
TROUBLESHOOTING
E-2
MAGNUM® PRO THRU THE ARM ROBOTIC TORCH
Observe all Safety Guidelines detailed throughout this manual
If for any reason you do not understand the test procedures or are unable to perform the tests/repairs safely, contact your
Local Lincoln Authorized Field Service Facility for technical troubleshooting assistance before you proceed.
CAUTION
PROBLEMS
(SYMPTOMS)
POSSIBLE
CAUSE
RECOMMENDED
COURSE OF ACTION
No wire feed occurs.
Sluggish wire feed.
Intermittent wire feed.
Frequent birdnesting or kinking of
wire in the gun cable.
Wire Brake not functioning.
1. Out of wire.
2. Contact tip burn back.
3. Fully or partially blocked gun liner.
4. Bird nest.
5. No motor voltage or current from
machine
6. Contact tip size too small for wire
diameter used.
1. Drive roll is worn or galled
2. Machineʼs wire feed speed set-
ting is too low.
3. Wire is obstructed somewhere
along the wire feed path in the
gun.
4. Low motor voltage.
5. Gun cable is twisted.
6. Mechanical resistance to wire
feeding is too large
1. Drive roll has become galled.
2. Wire has become kinked along its
feed path.
1 Wire shavings/lubricant is building
up in the cable.
2 Cable liner is too large for wire
size.
1. Air not being supplied.
2. Wire brake stuck closed.
1. Install full spool of specified wire.
2. Replace contact tip.
3. Remove and clean or replace gun
liner.
4. Cut out bird nest, reload wire, and
check for proper wire alignment.
5. See Troubleshooting section in
welding machineʼs or wire feed-
erʼs instruction manual.
6.Replace contact tip with one that
is the correct size.
1. Clean drive roll or replace drive
roll.
2. Increase wire feed speed.
3. Check for obstructions: remove
any wire shavings; remove kinked
wire; remove and clean or
replace gun liner.
4. See Troubleshooting section in
welding machineʼs instruction
manual.
5. Remove cable and reinstall per
installation instructions.
6. Reposition robot so that cable is
less twisted or bent.
1. Remove and then clean or
replace drive roll
2. Manually pull wire slowly thru gun
until unkinked wire emerges
1. Clean cable or replace cable
liner.
2 Install the smallest possible liner
which is specified for the wire
being used (i.e. use a .052-1/16
liner instead of a 1/16-5/64 liner
when welding with 1/16” diameter
wire.
1. Ensure proper air supply.
2. Repair / Replace as needed