Troubleshooting checklist (continued) – Warner Electric CB Series and Super CB Series Sizes 2, 4, 5, 6 and 8 User Manual
Page 9
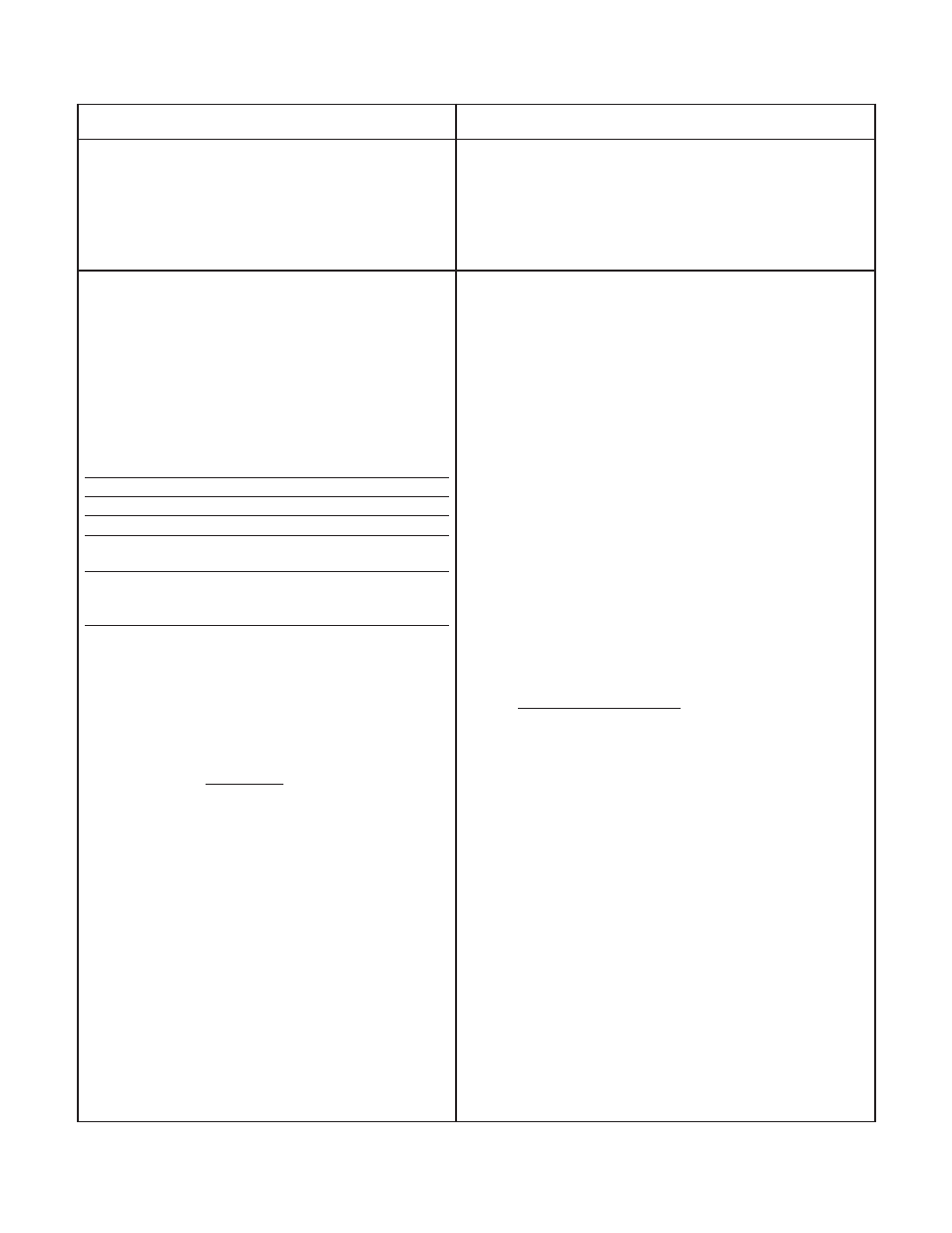
9
Warner Electric • 800-825-9050
P-258 • 819-0406
Troubleshooting Checklist (continued)
Possible Problem
Recommended Action
5. Lubrication has been added to the unit. Added
lubrication can result in a mis-match of lubricants which
can cause a soapy appearing viscous material around
the collar and springs. This can cause the springs to
slide on the hubs rather than grab them. The result is a
loss of accuracy.
A. Disassemble the unit. Using a clean rag, wipe excess material
from the hubs, springs and collar.
Do not use solvent
. (If the
added lubricant was due to spray from a chain lubricator, take
steps to guard against reoccurrence.) When re-assembling the
unit ensure that the spring differential is set properly. See
Section 5 “CB Spring Differential Adjustment.”
6. Output does not repeat stopping point
Clutch
Tc
t
lc
CB-2
1.65
0.003
0.0116
CB-4
4.40
0.004
0.0450
CB-5
6.88
0.004
0.1663
CB-6
8.75
0.005
1.221 (0.75 in. bore)
1.138 (1.0 in. bore)
CB-8
20
0.005
9.43 (.075 in. bore)
9.32 (1.0 in. bore)
8.15 (1.5 in. bore)
I = (t) (Tc + To) (3700) - Ic
RPM
How to determine maximum inertia load.
T x 3700 x t = WR
2
RPM
A. There is not enough RPM or inertia to fully disengage the
clutch spring and fully engage the brake spring. Add inertia
by either increasing RPM or adding weight to the output
(such as a sprocket or flywheel). To calculate the inertia
required, use the following table and formula:
Minimum Inertia Calculation
l = Minimum inertia required to fully activate the
Clutch/Brake - lb.in.
2
t = Time – Seconds
T
c
= Torque required to fully activate the
Clutch/Brake – in.lb.
T
o
= Frictional Torque – in.lb.
RPM = Revolutions per minute
lc = Inertia at the output side of the clutch – lb. in.
2
Example:
CB-5 in a system running at 300 RPM with 10 in. lb.
drag. What inertia is required to fully activate the
Clutch/Brake?
I = (0.004) (6.88 + 10) (3700) - 0.1663 = 0.6664 lb. in.
2
300
B. There is too much system friction (drag) to allow the output
inertia to fully disengage the clutch spring and engage the
brake spring. Reduce system friction. Also, see Section A
above on minimum inertia.
C. The control tang is broken on the brake spring. Replace the
spring, using the “Light Repair Kit.”
D. There is binding caused by rigid mounting. (See Section 2).
Unit must not be rigidly mounted. The plate must be
allowed to “float” axially.
E. There is insufficient anti-back holding capability, or the unit
has been reversed. See technical ratings for anti-back
holding capabilities and re-evaluate sizing.
Important: Do
not reverse unit!
F. An overhauling load is causing misregistration. Verify the
unit has anti-overrun feature.
G. The anti-overrun holding capacity has been exceeded. See
technical ratings and re-evaluate unit sizing.