Operation, Ransburg, High voltage on control sequence – Ransburg Voltage Master 2 78789_LEPS5001 User Manual
Page 28: High voltage off control sequence, Overload sequence
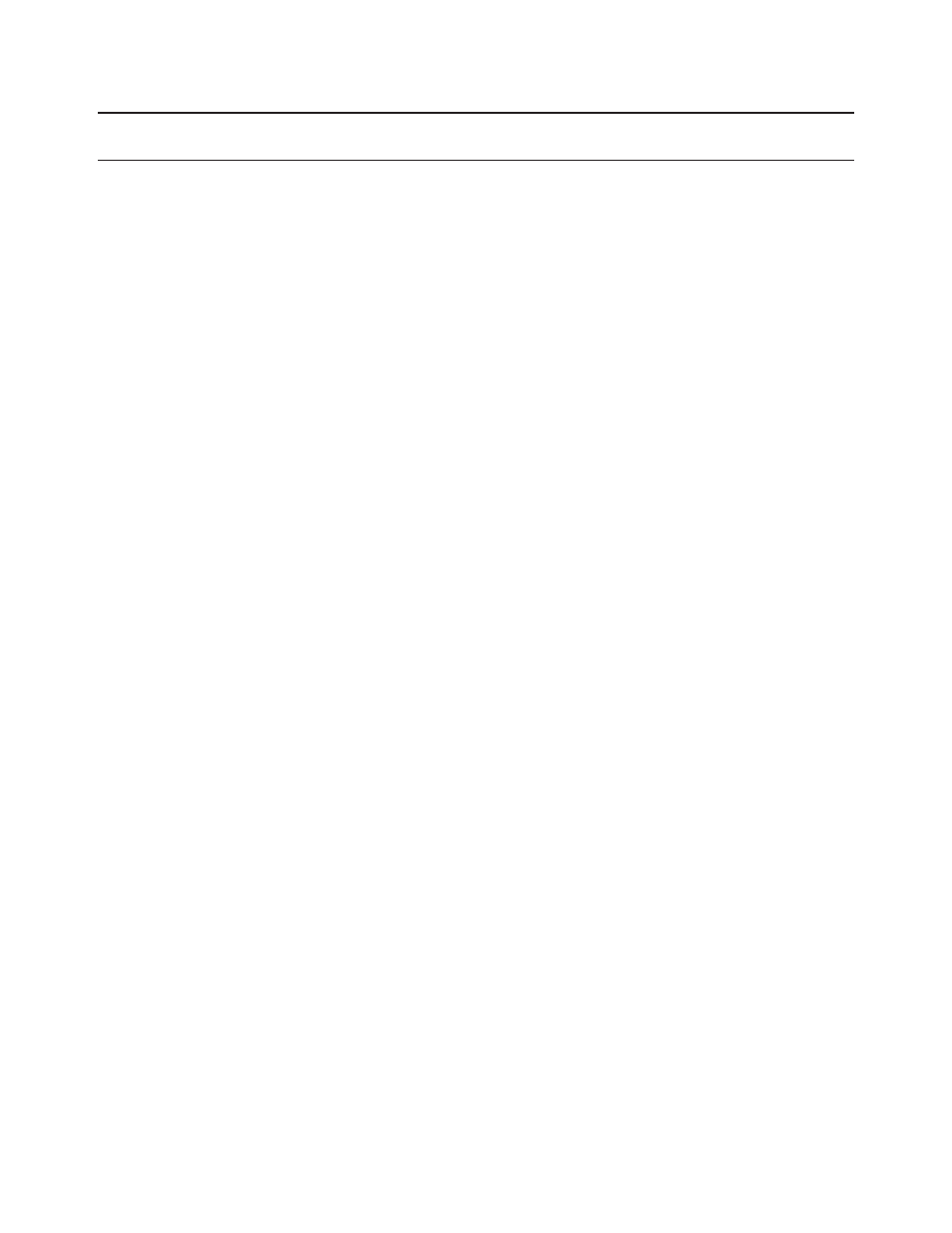
OPERATION
Reference the control panel schematic in Figure
5, the power supply schematic in Figure 14 and
any system installation drawings.
The following explanations assume that all ex-
ternal interlocks or jumpers are installed and
that the power supply is operating normally. The
following is intended for those that have a basic
understanding of electrical circuits and schematics.
HIGH VOLTAGE ON
CONTROL SEQUENCE
When the front panel HV ON/OFF momentary
switch or external HV ON signal (PLC or push-but-
ton) is supplied across terminals TB2-3 and TB2-5,
voltage is supplied to the CR1 coil through the
Master Control circuit board interlock (J3-1 &
J3-4) and one set of normally closed (NC) CR3
contacts. Voltage is also supplied through a series
of interlocks, pressure switch(es), and operator
controls, depending on the system installation
requirements, to CR2 and the HV ON lamp, any
of which will turn HV OFF or not allow HV to be
turned ON if broken. The voltage supplied to
CR1 energizes the coil causing NO CR1 contacts
(#11 to #12) to close, which then energizes the
CR2 coil and the HV ON indicator. Activation of
CR2 then causes one set of NO CR2 contacts to
close (#11 to #12) which latches the CR2 coil ON.
Another set of NO CR2 contacts supply voltage
from a set of NC CR3 contacts through the Motor
Control PCB interlock (J2-5 to J2-6) to the variable
control transformer (VAT1). VAT1 then supplies
AC voltage to the Power Supply via TB4 and then
through the control cable (supplied as part of the
power supply).
The overload circuit is activated upon application of
a momentary HV ON contact closure across wires
#3 and #5. When the contact closure opens, the
inhibit timer keeps the overload circuit disabled
for approximately 3-4 seconds, allowing the power
supply to reach normal operating voltage without
causing nuisance or unpredictable overloads at
start-up. The LED, located on the Master Control
board (see Figure 10), indicates that the inhibit
condition is active.
HIGH VOLTAGE OFF
CONTROL SEQUENCE
When the front panel HV ON/OFF/RESET, external
pushbutton, external interlock, or external PLC
HV OFF opens the circuit to wire #10, voltage is
removed from the coil of CR2. Thus, the NO CR2
contacts open and remove voltage from VAT1 to
the power supply and the HV ON indicator.
OVERLOAD SEQUENCE
The current return from the power supply tank is
compared to the overload setting within the Master
Control board circuit. If the actual output current
exceeds the overload setting, then a set of the
Control board overload relay contacts open (wire
#10 to J3-25, 27) disconnecting voltage from the
CR2 coil through the latched CR2 contacts (wire
#11 to #12) to VAT1 and therefore the power supply
tank. Another set of Control PCB overload contacts
close (wire #10 to #15) supplying voltage to the
CR3 coil, HV OL light, Horn, and external alarm.
One set of NO CR3 contacts (wire #10 to #15)
will then latch CR3 ON until a RESET command
is given which removes voltage at wire #10 and
therefore the CR3 coil. Another set of NC CR3
contacts open to ensure that the CR1 coil cannot
be energized again with a HV ON command until
a HV RESET (HV OFF) command has first been
received.
Voltage Master 2 - Operation
24
Ransburg
CP-02-02.6