FEC AFC1200 User Manual
Page 17
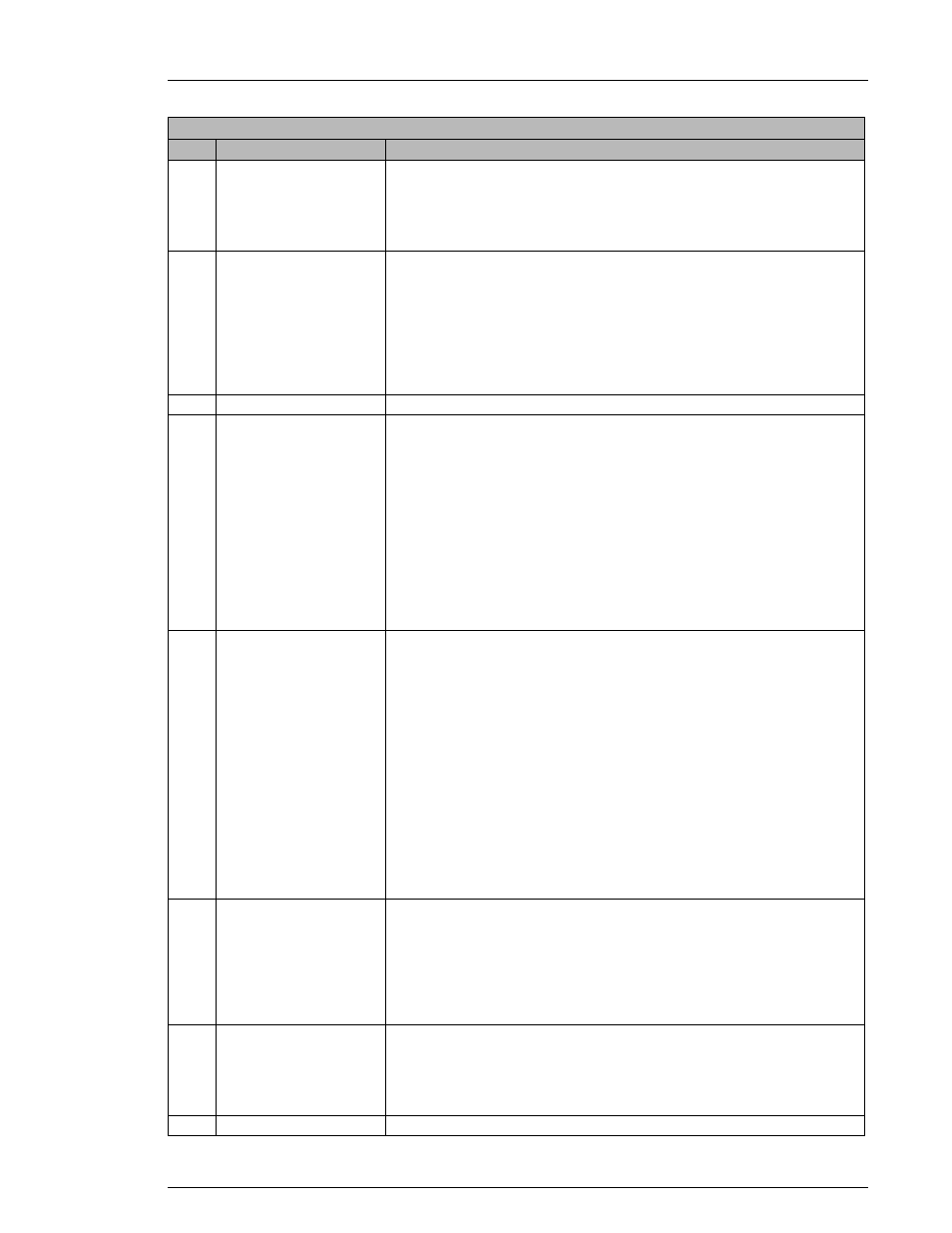
)(& ,QF
Not used - reserved for future implementation.
SEQ SELECT 3
12
Sequence Select Input (Normally Open)
These 3 inputs form a binary code which is capable of selecting up
to 8 different operation sequences. The different sequence options
allow the System to fasten to different specifications with only one
ISA Main Controller Unit. Refer to 4.7.2 Sequence Select Table.
SEQ SELECT 0
SEQ SELECT 1
SEQ SELECT 2
9
10
11
Cycle Count Input (Normally Open)
The System cycle counter will increment each time this signal is
input if the CYCLE COUNT UP is set to PLC SIGNAL on the
Machine Configuration screen. The Cycle Count Input requires a
pulse of at least 50 milliseconds to increment the counter. If the
CYCLE COUNT UP is set to AUTO, the cycle counter increments
automatically at every fastening.
CYCLE COUNT
8
Offset Check Input (Normally Open)
Used to perform the Offset (prevailing torque) Check. The Offset
Check input requires a pulse of at least 50 milliseconds to initiate a
360-degree prevailing torque check. The Busy signal will activate
and the Ready signal will deactivate during the Offset Check
process. After the value has been checked and is verified to be
within limits (less than 12% of the tool's full scale torque value), the
Accept light on the Main Unit will illuminate. If the value is outside of
the limits, the Reject light will illuminate and an Abnormal signal will
be output to the affected Axis Unit(s). If the Fastening Sequence
OFFSET CORRECTION (OC) command is enabled, the data from
the Offset Check will be used to compensate for the prevailing
(offset) torque. If the Fastening Sequence OFFSET CHECK (OF)
command is enabled, the Offset Check will be performed at the first
part of the fastening sequence, regardless of the status of this input.
OFFSET CHECK
7
Self-Check (Zero and Calibration) Input (Normally Open)
Used to perform the System's Self-Check function. The Self-Check
input requires a pulse of at least 50 milliseconds to initiate the Zero
Check and Cal Check. The Busy output signal will activate and the
Ready output signal will deactivate during the self-check cycle. After
the values have been checked (for all Axis Units) and are verified to
be within limits, the Accept light on the ISA Main Unit will illuminate.
If the data is outside of limits, the Reject light on the Main Unit will
illuminate, and an Abnormal signal will be output to the affected Axis
Unit(s). The self-check is performed automatically each time the
System is powered up. (Refer to Section 9.4 Axis Unit Abnormal for
more information regarding System Self-Checks.)
SELF-CHECK
6
Not used - reserved for future implementation.
RUN / PROGRAM
5
Start Cycle Input (Normally Open)
The Start input automatically resets the previous cycle, clears all
data to zero, and initiates the next fastening cycle.The Start input
requires a pulse of 200~500 milliseconds if the Machine
Configuration screen is set up for AUTOMATIC Start input. If the
Machine Configuration screen is set up for DEADMAN (hand-held
operations) input, the Start input must be maintained "on" for the
entire cycle.
START
4
Reverse Spindle Rotation Input (Normally Open)
All active spindles will rotate in an opposite direction for as long as
this signal is activated (on) and maintained. The Reverse input
functions the same as the Reverse pushbutton on the front of the
ISA Main Controller Unit.
REVERSE
3
DESCRIPTION
SIGNAL NAME
PIN #
PLC1 INPUT SIGNALS
Chapter 4: System Setup and Wiring
Page 4-17