Installation, Testing – Fulton Vertical Tubeless (FT-A) Thermal Fluid (hot oil) Heater User Manual
Page 38
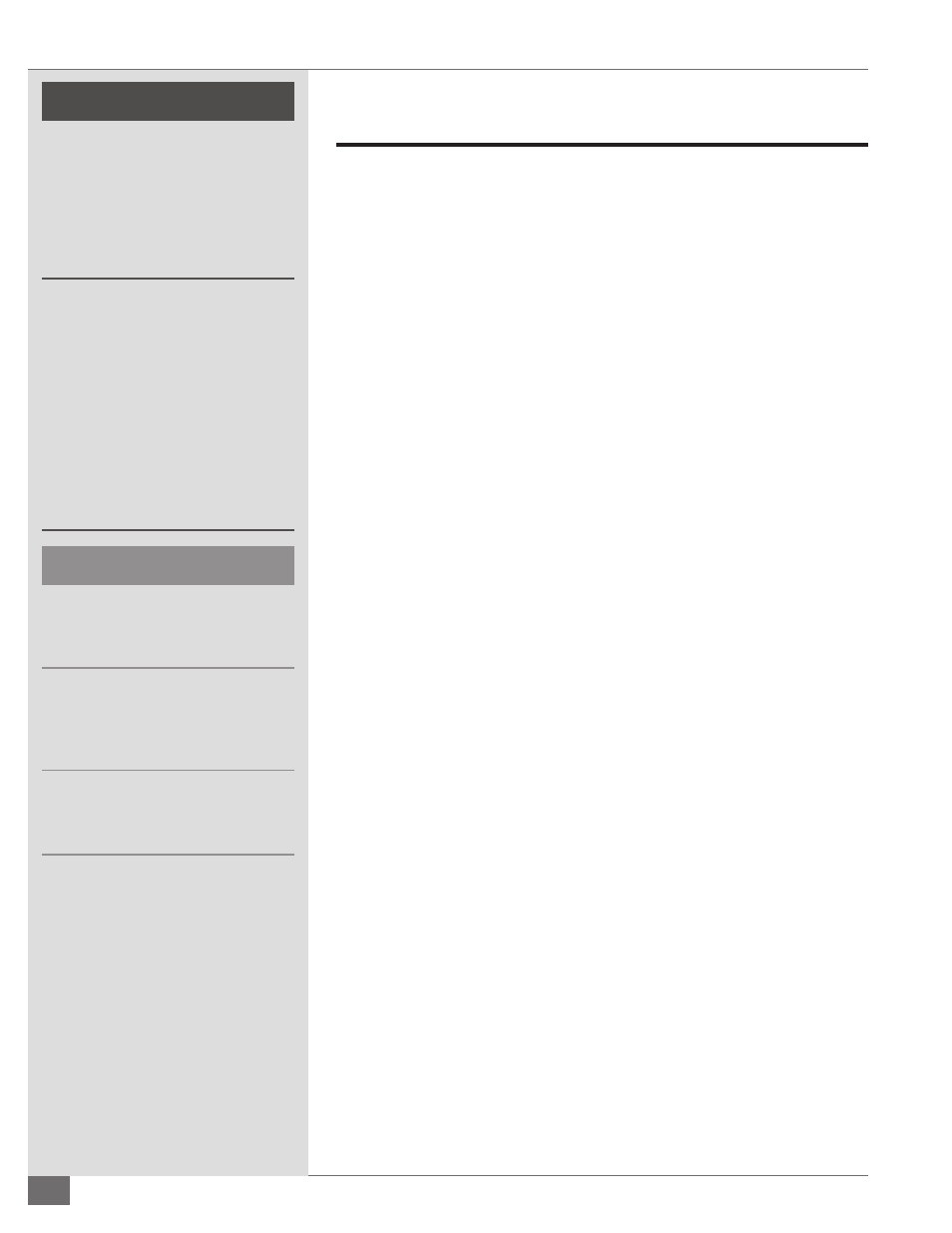
© The Fulton Companies 2013
INSTALLATION
FTA-IOM-2013-0227
SECTION 2
2-32
!
WARNING
All information in this manual is for
reference and guidance purposes,
and does not substitute for required
professional training, conduct,
and strict adherence to applicable
jurisdictional/professional codes and
regulations.
Do not attempt to start the
equipment for any testing prior
to fi lling and purging the vessel.
A dry fi re will seriously damage
the equipment and may result in
property damage or personnel injury
and is not covered by warranty. In
case of a dry fi ring event, shut off
the fuel supply and allow the vessel
to cool to room temperature before
fl uid is reintroduced to the pressure
vessel.
4
CAUTION
Avoid fl ue corrosion and other negative
impacts ensuring properly-sized stack
and fl ue.
In order to meet warranty conditions,
ensure appropriate tests and
operational safety activities are
performed.
Unless specially fi ltered, compressed air
will introduce moisture to the system.
Dry air or nitrogen is recommended.
Testing
Upon completion of the installation, perform the following testing:
1. A pneumatic test of thermal fl uid piping not exceeding 15 psig.
2. Soap tests at all welds and joints to ensure that the system is free from
leaks.
NOTE: Under no circumstances should the system be fi lled with water. Make sure
that the air supply is as free from moisture as possible.
3. Boil-out. The time needed for adequate boilout directly corresponds
to the volume of the system and the amount of moisture and debris in
the system. Boilout typically takes anywhere from one to three days to
complete. Pressure testing on the system should be done by means of an
inert gas such as nitrogen or by an air compressor producing dry air (air
with a dewpoint of 50 F [10 C] or less). Never perform a hydrostatic test on
the system. The boilout procedure is described in the Operation section
of this manual.
4. The most satisfactory method of testing is to introduce bottled nitrogen
through a pressure control valve. Check pressure ratings on all equipment
in the system to ensure that it is capable of withstanding the pressure
involved.