Cashco DA6 User Manual
Page 8
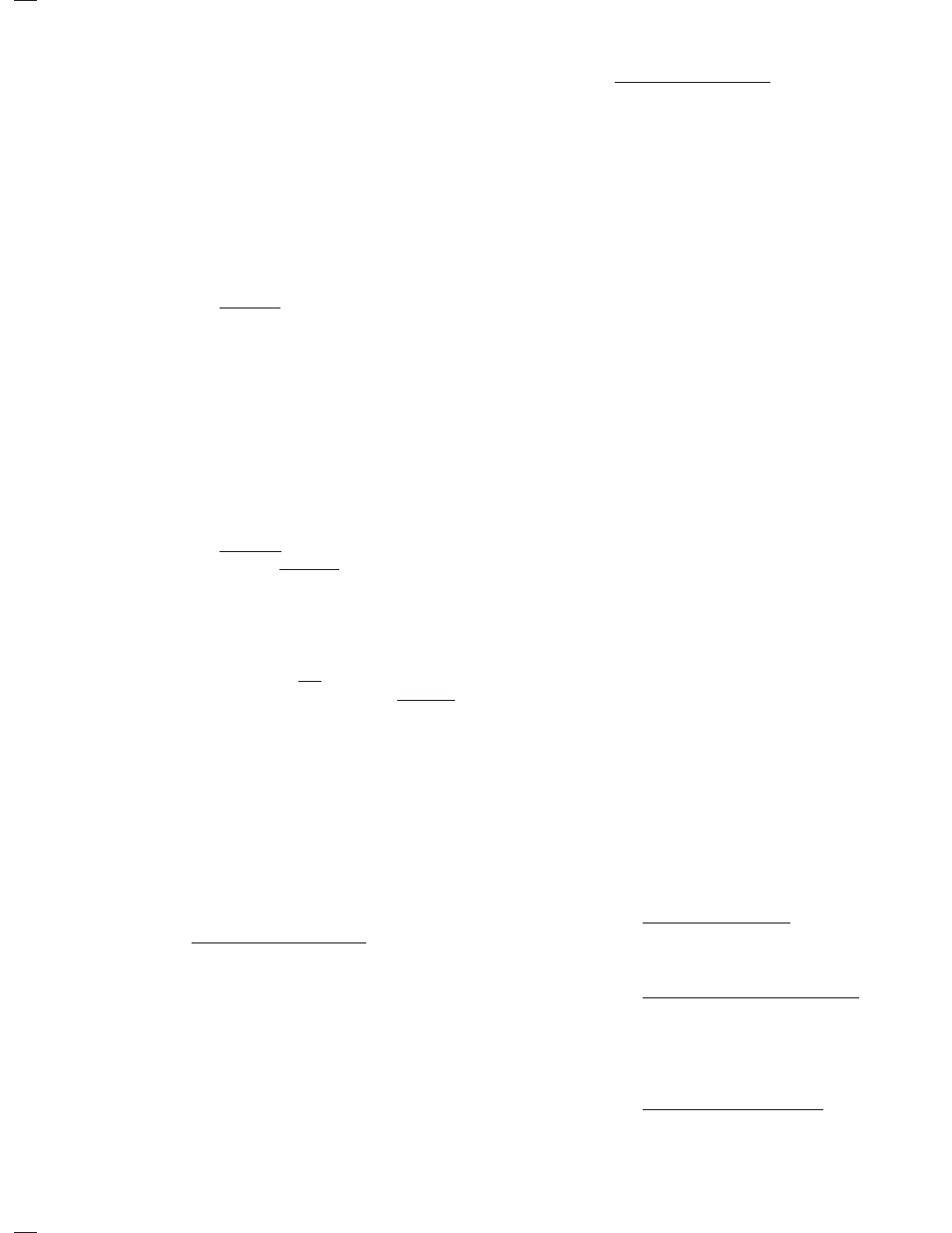
IOM-DA6
8
2. Spread a piston ring seal (27.5) and
slide over lower circumference groove
of valve plug (20), taking care not to
“cut” piston ring seal (27.5). Using
thumbs, work the piston ring seal
(27.5) into the groove of the valve
plug (20). Repeat this pro ce dure
with a second piston ring seal (27.5).
Ori ent/rotate the "splits" in piston ring
seals (27.5) 180° across from each
other.
c. Type
UC:
1. Stretch u-cup seal (27.3) over upper
cir cum fer ence of valve plug (20), tak-
ing care not to “cut” u-cup seal (27.3)
on the protruding shelf that is part of
the valve plug's (20) groove. Ensure
that the u-cup seal (27.3) is oriented
with the center-open-upwards as
shown in Figure 1, as the u-cup seal
(27.3) depends upon the P1-Inlet
Pres sure to pres sure activate the seal
for proper seal ing action.
d. Type
NO:
1. For
“standard”
fl ow direction ap pli ca -
tions, it is not absolutely required that
a dynamic side seal (27) be installed.
(When included with the dynamic seal
(27), better guiding of valve plug (20)
results.) Type “NO” dynamic seal (27)
means NO dynamic seal.
2. The more common “Reverse” fl ow
direction always requires a dynamic
side seal (27).
7. Place fl uid compatible thread anti-seize,
Locktite Corp., "Nickel Anti-Seize", or equal
on thread ed portion of diaphragm cap screw
(7), sizes 1-1/4" and 1-1/2"; or, thread ed post
por tion of valve plug (20), sizes 1/2" – 1" and
2-1/2" – 4". (NOTE: Valves cleaned for oxy-
gen service should use fi sher Scientifi c Co.,
"Fluorolube GR-362", or equal.)
8. Body sizes 2-1/2" thru 4":
a. Place o-ring lower stem seal (14.3) over
upper-end of plug (20) and into groove on
plug (20).
b. Place properly oriented piston/guide bear-
ing (13) over upper-end of plug (20) and
into position on plug (20).
c. Place o-ring middle seal (14.2) over up-
per-end of plug (20) and into groove of
piston/guide bearing (13).
9. Body sizes 1/2 thru 2":
Place new o-ring middle stem seal (14.2) into
groove of valve plug (20) upper surface.
10. Position lower diaphragm pusher plate (10)
on/over upper end of valve plug (20) properly
oriented. For composition di a phragm con struc -
tion the “tongue and groove” “ridge” should
be on upper side, “fl at” side down wards. For
metal diaphragm construction the “rounded”
surface of the lower diaphragm push er plate
(10) should be on upper side, “fl at” side down-
wards.
11. For composition diaphragm construction, place
new o-ring upper stem seal (14.1) on/over
upper end of valve plug (20) and into groove
of lower diaphragm pusher plate (10).
12. For metal diaphragm construction, place
com pat i ble gasket sealant on both sides and
place new lower pusher plate gasket (14.4)
on/over upper end of valve plug (20) and onto
lower diaphragm pusher plate (10). (Gasket
sealant is Federal Process Corp. "Gasoila",
or equal.)
13. Position new diaphragm(s) (9) on/over upper
end of valve plug (20). NOTE: For multiple
diaphragms (9) that include TFE material, the
TFE should be on the wetted side; for 6-ply
elastomeric TFE diaphragm (9), stackup is
TFE-TFE-HK-HK-TFE-TFE, beginning with
the low er wetted diaphragm (9) fi rst.
14. Position upper diaphragm pressure plate (8)
on/over upper end of valve plug (20) prop-
erly oriented. For composition diaphragm
con struc tion the "tongue and groove" "ridge"
should be on lower side, "fl at" side upwards.
For metal diaphragm construction the "round-
ed" surface of the upper diaphragm pressure
plate (8) should be on lower side, "fl at" side
upwards.
15. a. Body sizes 1/2" thru 1": Engage di a phragm
locknut (7) to thread ed post por tion of
valve plug (20) and torque to 60-70 ft-lbs.
by rotating CW.
b. Body Sizes 1-1/4" and 1-1/2": Insert
anti-seize coated di a phragm cap screw
(7) through stacked parts (8, 9, 10, 14.1,
14.4) and into upper end of valve plug (20).
Torque-tighten diaphragm cap screw (7)
to 120-130 ft-lbs.
c. Body Sizes 2-1/2" thru 4": Engage di a -
phragm locknut (7) to threaded post of
valve plug (20) and wrench-tighten fi rmly.