Cashco DA6 User Manual
Page 7
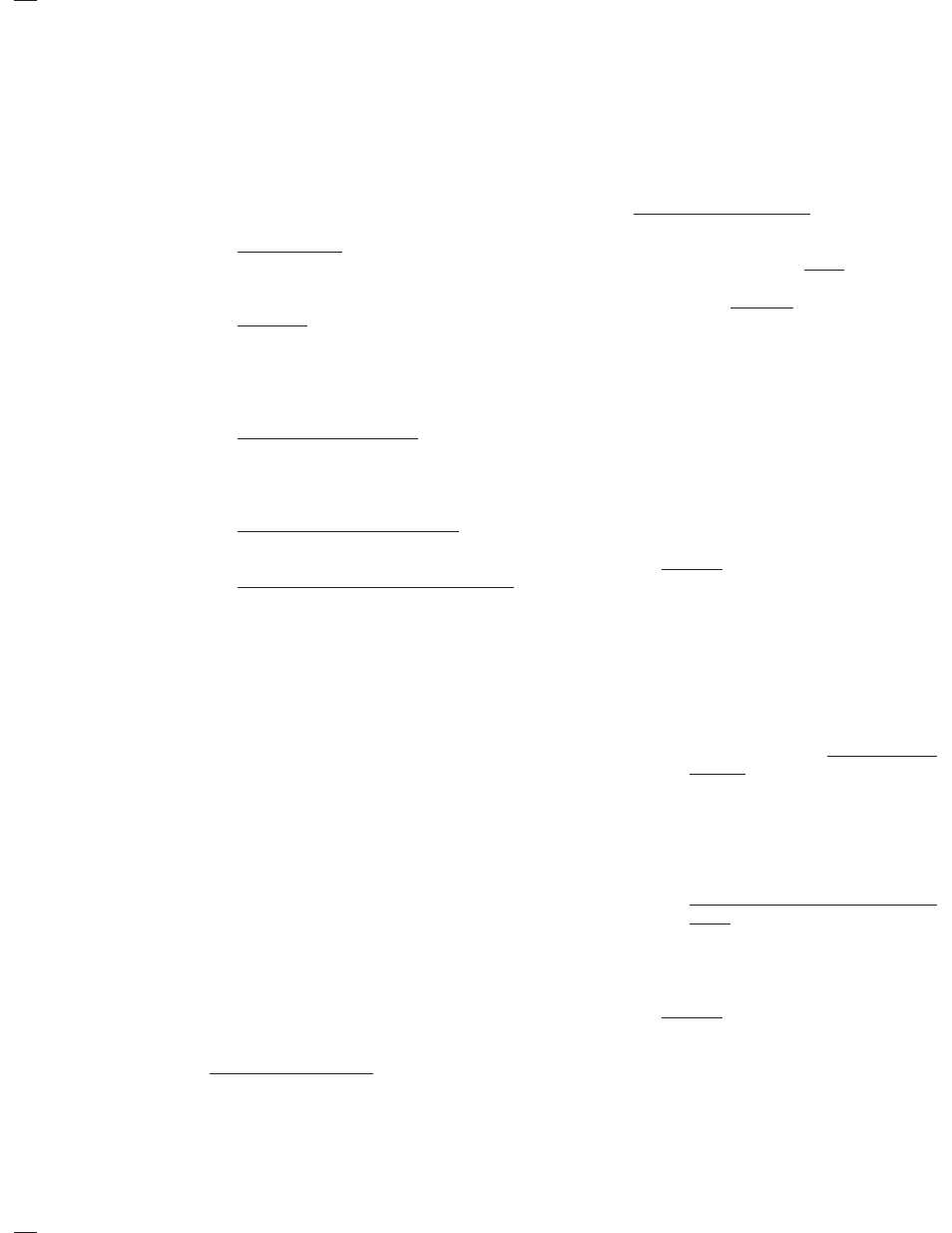
IOM-DA6
7
2. Inspect the metal parts that will be reused. The
parts should be free of surface con tam i nants,
burrs, oxides, and scale. Rework and clean
the parts as necessary. Surface con di tions
that affect the regulator performance are stated
below; replace parts that can not be re worked
or cleaned.
3. QC Finish & Dimensional Requirements:
a. Valve plug (20);
1. No major defects on plug's (20) bot-
tom guide spindle, or at guide area
near dynamic seal groove.
b. Cage
(19);
1. 16 rms fi nish on cylinder bore. No
“ledges” formed due to wear from
moving dynamic side seal (27).
2. 16
rms
fi nish on its seating surface
for tight shutoff.
c. Lower guide bushing (24);
1. 16
rms
fi nish on bore.
2. Max 0.015 inch (0.38 mm) clearance
be tween valve plug (20) spindle and
lower guide bushing (24).
d. Internal sensing drilled plug (32);
1. Ensure that bore is minimum 0.125
inch (3.20 mm). Drill out as required.
e. Piston/Guide Bearing (13) (2-1/2"-4" only);
1. No defects at guide area near dy nam ic
seal groove.
4. Staging Material for Reassembly.
a. Inspect and clean parts, as necessary,
from the spare parts kit. (See Article VII.
A.4. comments concerning cleaning for
ox y gen service.)
b. Lay out all the regulator parts and check
against the bill of material.
E. Reassembly of the ITA:
1. Position valve plug (20) with seat disc-end
upwards. Place new seat disc (28) into re-
cess of lower end of valve plug (20) properly
ori ent ed.
2. Position seat disc washer (29) next to seat
disc (28).
3. Engage seat disc nut (30) to secure wash er
(29) and seat disc (28) to valve plug (20).
Firmly hand-tighten.
4. Body Sizes 1/2" thru 2":
a. Using the two square-section met al bar-
stock pieces of VII.C.1.a., clamp the plug
(20) into a vise with the plug's (20) spindle
pointed up wards.
b. Using a torque wrench, tighten the seat
disc nut (30) to 20 – 35 ft-lbs. by rotating
CW.
c. Remove assembly (20, 28, 29, 30) from
vise and rotate end-for-end and resecure
in vise using same metal bars.
5. Body Sizes 2-1/2" thru 4":
a. Orient plug (20) with upper end up wards,
place into a vise, grasping the seat disc nut
(30); tighten the vise lightly, only enough
to "hold" the plug (20) from ro tat ing out of
the vise. Caution: Over-tightening the
vise can distort the seat disc nut (30) and
give bad fi nal torque values.
b. Place a torque wrench on the 3/4" hex
upper end of the plug (20); tighten the seat
disc nut (30) to 40 – 60 ft-lbs. by ro tat ing
CW.
6. Installation of dy nam ic side seal (27) (See
Figure 1): (NOTE: Dynamic side seal (27) for
sizes 2-1/2" – 4" is located on the piston/guide
bearing (13). The dynamic side seal can be
installed on a workbench without need of a
vise.)
a. Type
CP:
1. Stretch o-ring energizer/seal (27.2)
over low er cir cum fer ence of valve
plug (20), tak ing care not to “cut”
o-ring en er giz er/seal (27.4). Using
thumbs, work the o-ring en er giz er/
seal (27.4) up and into the groove of
the valve plug (20). NOTE: A very
slight amount of fl uid and elas tomer
com pat i ble lu bri cant is rec om mend ed
as an in stal la tion aid. DO NOT “ROLL”
O-RING.
2. Position TFE cap seal (27.1) ring with
rectangular cross-section at lower end
of valve plug (20). Stretch cap seal
(27.1) over low er end of valve plug
(20) us ing thumbs to work the cap
seal (27.1) onto the valve plug (20).
DO NOT USE A TOOL FOR THIS
STEP. Con tin ue pressing cap seal
(27.1) up wards to wards the groove
until the cap seal (27.1) “snaps” into
the groove of the valve plug (20).
b. Type
PR:
1. Wrap corrugated metal piston ring
en er giz er (27.6) over lower cir cum -
fer ence groove of valve plug (20). Us-
ing thumbs work the energizer (27.6)
into the valve plug (20) groove.