C.E. Niehoff & Co. N1387-1/EPM Troubleshooting Guides User Manual
Page 2
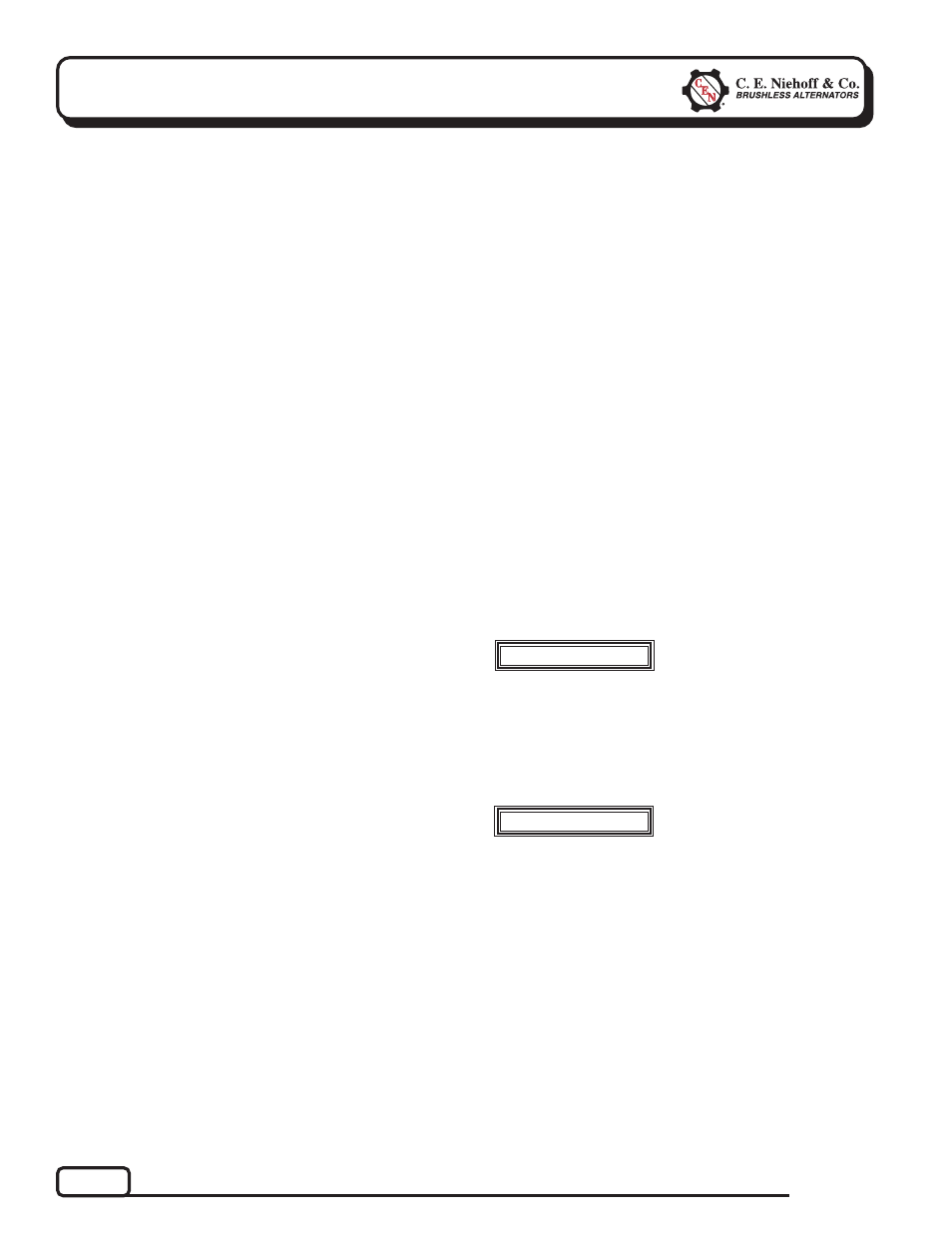
Page 2
TG0019A
Section 1: Component Description and Operation
CEN N1387-1 Dual Voltage Alternator Descrip-
tion and Operation
N1387-1 28 V 210 A alternator with optional 28 V/14
V (50 A maximum on 14 V) is internally rectified. All
windings and current-transmitting components are
non-moving, so there are no brushes or slip rings to
wear out.
After engine is running,
N3225 regulator receives
energize signal. Regulator monitors alternator
rotation and provides field current only when it
detects alernator shaft rotating at suitable speed.
After regulator detects alternator rotation, it gradu-
ally applies field current, preventing an abrupt
mechanical load on accessory drive system. The soft
start may take up to 20 seconds.
N3225 regulator used with these units also
• is negative temperature compensated. Setpoints
are 28.0 ± 0.2 V and 14.0 ± 0.2 V at 75° F.
• provides overvoltage cutout (OVCO). Regulator
will trip OVCO when system voltage rises above
32 V in a 28 V system (16 V in a 14 V system) for
longer than 2 seconds. OVCO feature detects high
voltage and reacts by signaling relay in F– alterna-
tor circuit to open, turning off alternator. Restart-
ing engine resets OVCO circuit. If vehicle is run in
OVCO mode OVCO will automatically reset when
system voltage drops to 22 V (11 V on 14 V side).
Regulator regains control of alternator below
output voltage.
• maintains alternator output voltage at regulated
settings as vehicle electrical loads are switched
on and off.
• can be used in single or dual voltage with this
alternator.
— Allows single-voltage operation (28 V only).
14 V is not available as a single voltage appli-
cation.
— Provides optional 28 V/14 V output only from
the regulator when phase cable from alterna-
tor is connected to regulator.
• works with the EPM to provide dual voltage
output during batteryless operation. When
operating in batteryless mode, the system will
have higher ripple. LEDs might change color
more rapidly depending on loads.
EPM Electric Power Manager used with these units
• is rated for continuous current at 200 A on 28 V
side. The 14 V side is rated for continuous
current at 100 A.
• manually connects batteries after battery-connect
button on vehicle is pressed.
• automatically disconnects batteries from vehicle
loads 3 minutes after engine shuts down.
• provides 28 V auxillary output power for up to
four 20 A channels and 14 V auxillary output
power for one 20 A channel, protected by an
internal, resettable, electronic circuit breaker.
• keeps batteries connected to system when emer-
gency flashers are used.
Normal Start-Up Procedure
1. Press the vehicle battery-connect button to connect
batteries.
2. Turn START-RUN switch to RUN.
3. Wait until glow plug light goes off.
4. Turn START-RUN switch to START and crank
engine.
5. Return switch to RUN when engine starts.
6. If engine fails to crank, turn START-RUN switch to
OFF, repeat steps 1-5 above.
7. If engine still fails to start, the EPM could be
damaged.
Emergency Start-Up Procedure
1. Connect slave vehicle Nato connector to vehicle.
2. Follow steps 2-5 above.
3. Disconnect slave NATO connector after engine is
running.
Shutdown Procedure
1. Place gear shift in park or neutral and set parking
brake.
2. Turn start-run switch to OFF to stop engine.
3. Batteries will be disconnected from vehicle in 3
min. unless emergency flashers are on, then
batteries will stay connected until flashers are
turned off or battery is discharged.
This procedure will bypass EPM and
batteries in system. Use this
procedure ONLY when vehicle must
be removed immediately from
location in an EMERGENCY.
a. Remove cables from “Load” side of EPM and
temporarily attach to “Battery” side of EPM.
b. Follow steps 2-5 above.
Do not leave vehicle cabling
connected as described in steps 7a-
b. Diagnostic and repair must be
performed as soon as possible.
WARNING
WARNING