Appendix a - worked example – Atec Agilent-53200A Series User Manual
Page 22
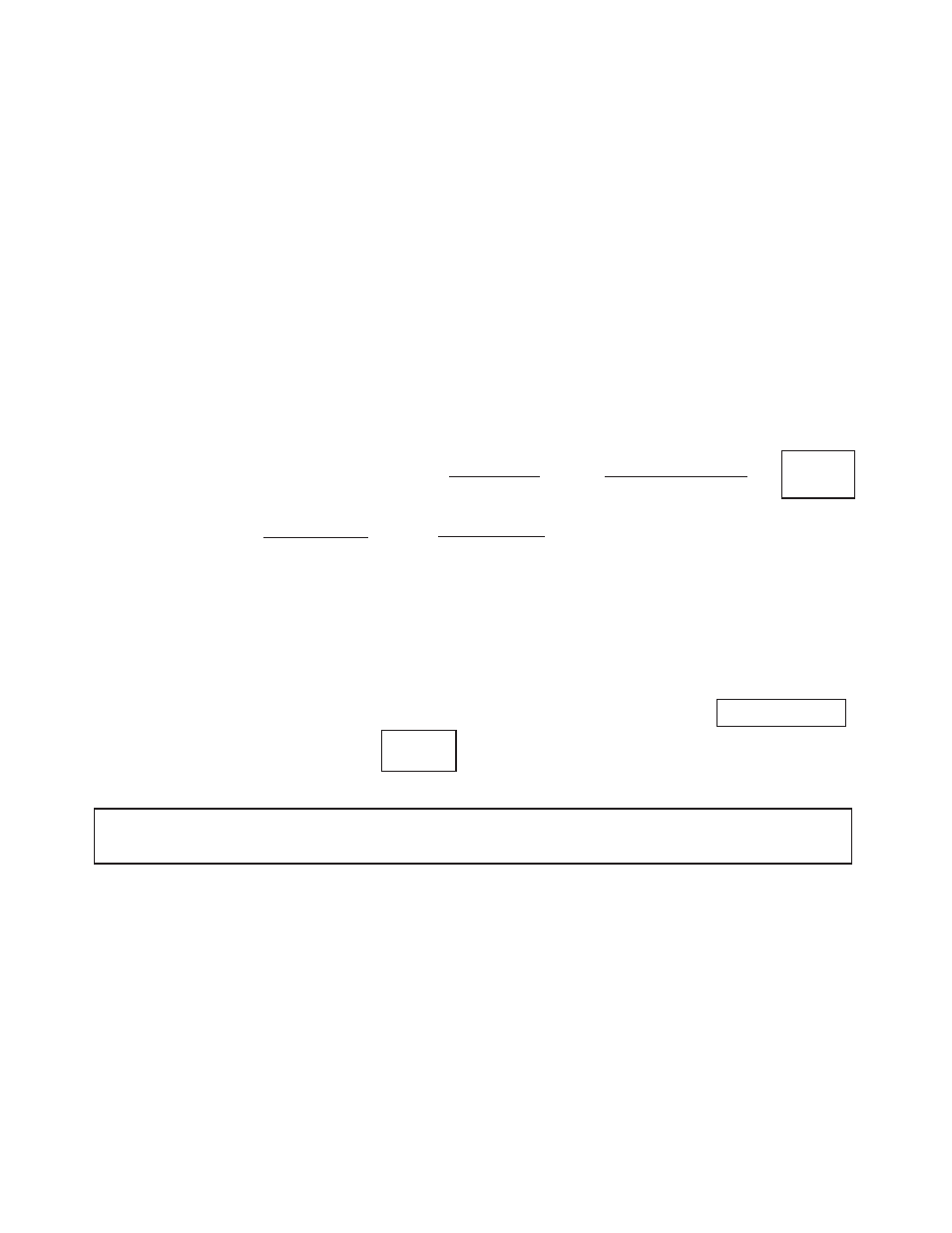
22
Parameter assumptions:
• 53220A
• 95% confidence
• 100 MHz signal, 1 sec gate
• AUTO frequency mode
• Level: 5 V input signal amplitude
• TCXO standard timebase for unit plugged in for 30 days
• Assume operating temperature is within T
CAL
± 5 °C
• Instrument has been re-calibrated so Factory Calibration Uncertainty term is not required.
Process:
Basic accuracy = ± [(k * Random Uncertainty) + Systematic Uncertainty + Timebase Uncertainty]
1. Use k=2 for 95% confidence and k=2.5 for 99% confidence calculations)………………..k = 2
2. Random uncertainty for frequency measurement =
=
=
T
SS
= 100 ps
T
E
(for 5 V)
E
N
= Assume input signal RMS noise voltage is 0.
Vx = N/A (remove signal from other channel)
SR
-TRIG POINT
= maximum slew rate (sine)SR= 2πF*V
0 to PK
= 2π(100 MHz)*5 V = 3.14*10
9
Volts/Hz
Since
T
SS
>> T
E
, we use the R
E
equation. Value is much greater than 6. so we limit RE to 6 due to gate time. R
E
= 6
Gate time = 1 sec
3. Systematic uncertainty for frequency measurement = If R
E
>= 2: 10
ps/gate max, 2 ps/gate (typ) = 2 E-12 parts error
4. Timebase uncertainty = aging = 0.2 ppm =
Aging: 0.2 ppm
Basic accuracy = ± [(k * random uncertainty) + systematic uncertainty + timebase uncertainty] =
± [(2 * (23.3 E-12)) + 2 E-12 + 0.2 E-6] = ± 0.2 E-6 parts error
Note: Using a higher accuracy timebase or locking to an external timebase standard will have the biggest impact on
improvement to accuracy calculations.
Appendix A - Worked Example
Basic Accuracy Calculation for Frequency Measurement
1.4* (T
SS
2
+ T
E
2
)
½
R
E
* Gate Time
1.4* (100ps
2
+ .159ps
2
)
½
6 * 1 s
23.3 E-12
parts error
(500 μV
2
+ E
N
2
+Vx
2
)
½
SR
-TRIG POINT
(500 μV
2
)
½
3.14 * 10
9
.159 ps
=
=
=
0.2 E-6
parts error