Cla-Val 393-01/3693-01 User Manual
Page 26
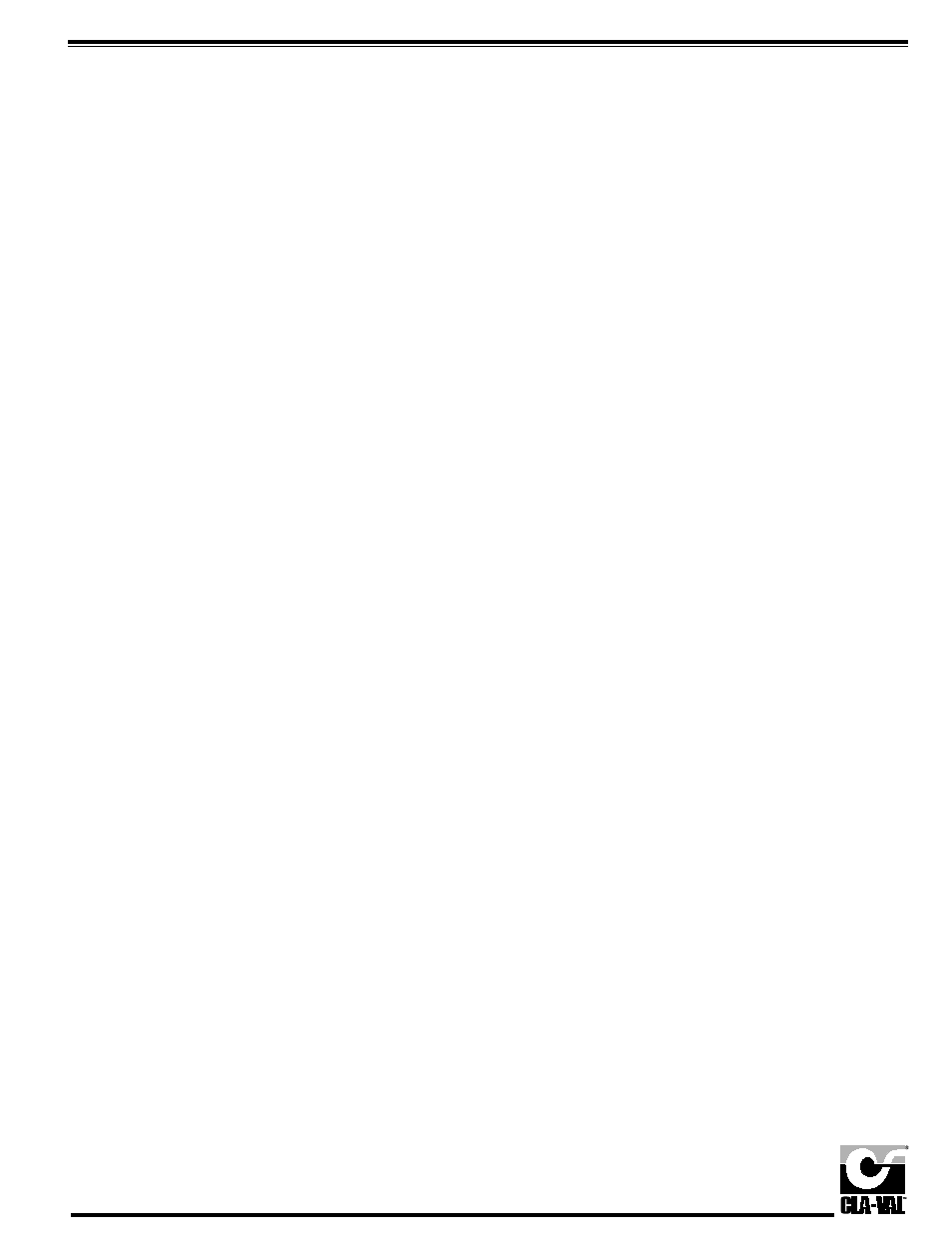
Setting the maximum process variable limit.
Method one: Using the system process variable.
Set the maximum process variable limit by increasing the
actual system dynamic (i.e. pressure, flow etc.) to the
desired value. This can be done by pressing the actuator
increase or decrease push button to attain the desired max-
imum process variable. When achieved, press the red
enable and the white LS2 push buttons at the same time.
The LED directly underneath will illuminate to confirm the
setting. Default setting is 20 mA.
Method two: Applies only to external PV using a milliamp
calibrator (if process variable cannot be changed or is not in
service).
Disconnect the actual process variable wires located on the
logic board (including jumper on terminals 11 and 12 if
used) and connect a milliamp calibrator to the process vari-
able input terminals 10 (+) and 11 (-). Use a milliamp value
corresponding to the desired maximum process variable
limit (i.e. 75 psi = 16mA, if transducer range is 0-100 psi).
This must be 20mA or less. Press the red enable and the
white LS2 push buttons at the same time. The LED directly
underneath will illuminate to confirm the setting. Default
setting is 20 mA.
Setup Complete.
Once the setup of the actuator has been completed, the
setup mode selector must be turned off.
This can be
accomplished by placing switch #4 into the up position. The
actuator is now in remote automatic operation and actuator
movement will begin immediately.
2 Configuration procedures for remote manual mode.
Remove cover using a 3/16 inch Allen wrench.
In this mode, movement of the actuator is by dry contact
closures (supplied by others). Only the direction of rotation,
speed of rotation and actuator minimum and maximum
positions require setting. Use the following steps to estab-
lish or change some or all of the default settings.
Main Power Supply Selection.
The AC input voltage must be selected prior to powering up
the actuator. After cover removal, locate the main switch
located on the power supply board (see power supply
terminal diagram). Slide the switch to the position
corresponding to the correct input line voltage. Default is
120VAC
Right for 120 VAC.
Left for 240 VAC.
Direction of Rotation.
The direction is determined by the position of switch #1.
When this switch is in the down position indicating reverse
acting, the actuator will rotate clockwise when an increasing
command is given. When the switch is in the up position
indicating direct acting, the actuator will rotate counter-
clockwise when an increasing command is given.
Default setting is reverse acting.
Setting the actuator speed.
Turning the speed potentiometer to the desired value can
set actuator speed. Increase is CW and decrease is CCW.
Default setting is 1/2 RPM.
Setup Mode.
The setup consists of setting the lowest limit of actuator
travel (zero position) and the highest limit of actuator travel
(span position). Placing switch #4 (setup mode) in the down
position enables the setup mode. Actuator travel can then
be increased using the blue push button and decreased
using the yellow push button to any position. While in this
mode, all remote commands given to the actuator will be
temporarily disabled.
Setting the minimum actuator position.
Position the actuator using the increase or decrease push
button to the desired minimum position. Press the red
enable and the blue zero push buttons at the same time.
The LED light directly underneath the blue zero push button
will illuminate confirming the setting. Default setting is
minimum CCW position.
Setting the maximum actuator position.
Position the actuator using the increase or decrease push
button to the desired maximum position. Press the red
enable and yellow span push buttons at the same time. The
LED adjacent to the yellow span push button will illuminate
confirming the setting. Default setting is 8 turns from min-
imum CCW position.
Setup Complete.
Once the setup of the actuator has been completed, the
setup mode selector must be turned off.
This can be
accomplished by placing switch #4 into the up position. The
actuator is now in remote manual mode and actuator move-
ment will begin upon contact closure.
3 Diagnostics
The actuator contains two types of diagnostics. LED indica-
tion and voltage meter test ports.
4