130 series actuator start up procedures – Cla-Val 393-01/3693-01 User Manual
Page 24
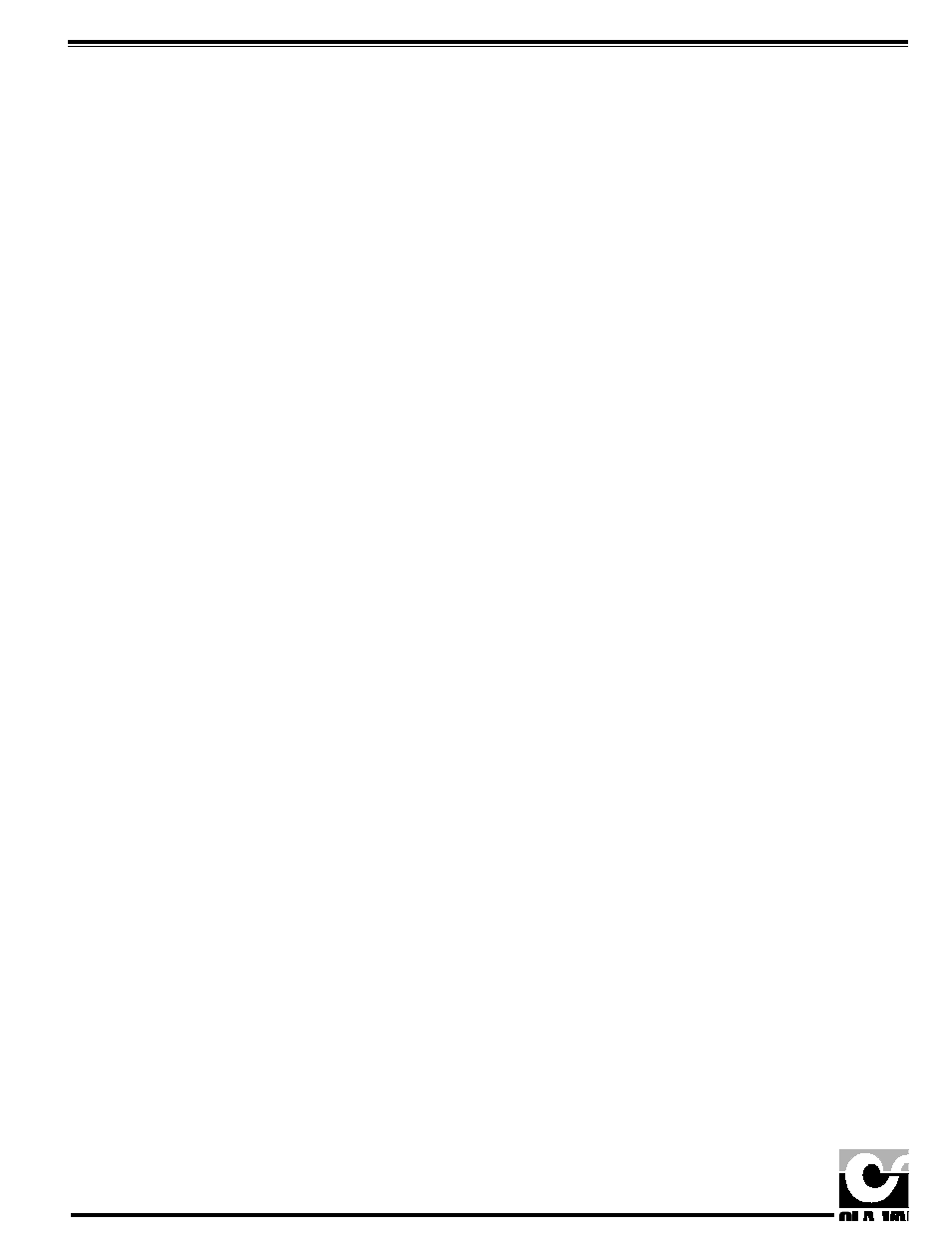
130 Series Actuator Start Up Procedures
Introduction
It is recommended that this manual is read before applying
power to the actuator and start up is attempted. It will take
you step by step through:
• Modes of operation
• Factory configured default settings
• Configuration procedures
• Setup procedures
• Diagnostics
• Electrical components and wiring information
For specific information on the pilot(s) and control
valve being actuated, consult the appropriate section of
the Instruction Operation and Maintenance Manual (i.e.
CRD-30, CRL-30, 90-01, etc.).
There are two separate methods of remote operation possi-
ble with the actuator. These are remote automatic and
remote manual.
The remote automatic mode can use an external process
variable or an internal potentiometer as the feedback signal.
Enable either one by changing the wiring on TB4 terminal
strip (see pages 8,9 and 10).
Remote automatic mode. In this mode the actuator will
typically position in the increasing direction when the set-
point (local or remote) is greater than the process variable
(external PV or internal potentiometer). The actuator will
continue to increase until the process variable is equal to
the setpoint, the actuator maximum travel position (span) is
reached or the process variable has reached a value equal
to the maximum process variable limit.
The actuator will also decrease when the setpoint is lower
than the process variable value. The actuator will continue
to decrease until the process variable is equal to the set-
point, the actuator minimum position (zero) is reached or
the process variable has reached a value equal to the min-
imum process variable range limit.
Remote manual mode. In this mode the actuator can be
positioned between the minimum actuator position (zero)
and the maximum actuator position (span) using dry contact
closures supplied from an external source.
Factory default setting information.
The actuator, if new and factory installed on a hydraulic
pilot, has been configured to specific default settings and
preset at minimum actuator position. If these settings are
appropriate for your application, then further configuration
may not be required.
If new and not installed, these default settings will still be
present, however some adjustment to the hydraulic control
will be required. It will be necessary to turn the adjusting
stem of the hydraulic control counter clockwise to the mini-
mum spring setting before the actuator is installed. This will
insure that the minimum spring setting of the hydraulic pilot
is equal to the minimum setting of the actuator.
If previously in service and settings are unknown, the unit
should be completely reconfigured and the procedure for
the hydraulic control adjusting stem, as described above,
should be followed.
Default settings.
• Actuator power: 120 VAC
• Direction: Reverse acting (clockwise rotation when
process variable is less than setpoint)
• Speed: 1/2 RPM
• Loss of remote setpoint or process variable:
Actuator locks in place.
• setpoint
type: 4-20
mA
• Zero (minimum) actuator position:
Set at minimum CCW position
• Span (maximum) actuator position:
Set at 8 turns CW from minimum CCW position
• Minimum process variable range limit: 4.0 mA
• Maximum process variable range limit: 20.0 mA
• Actuator set to minimum 4.0 mA position
1 Configuration procedures for remote automatic mode
This section contains the configuration and setup proce-
dures for the remote automatic mode only. Use these
steps to establish or change some or all of the default set-
tings.
Remove cover using a 3/16 inch Allen wrench.
Main Power Supply Selection.
The AC input voltage must be selected prior to powering up
the actuator. After cover removal, locate the main switch on
the power supply board (see power supply terminal dia-
gram). Slide the switch to the position corresponding to the
correct input line voltage.
Right for 120 VAC.
Left for 240 VAC.
Direction of Rotation.
The direction is determined by the position of switch #1.
When this switch is in the down position indicating reverse
acting, the actuator will rotate clockwise when an increasing
command is given. When the switch is in the up position
indicating direct acting, the actuator will rotate counter
clockwise when an increasing command is given. Default
setting is reverse acting.
Actuator speed.
Turning the speed potentiometer to the desired value will set
actuator speed. Increase is CW and decrease is CCW.
Default setting is 1/2 RPM.
2