Cla-Val 582SWS Series User Manual
Two-door check valves, Series installation / operation / maintenance
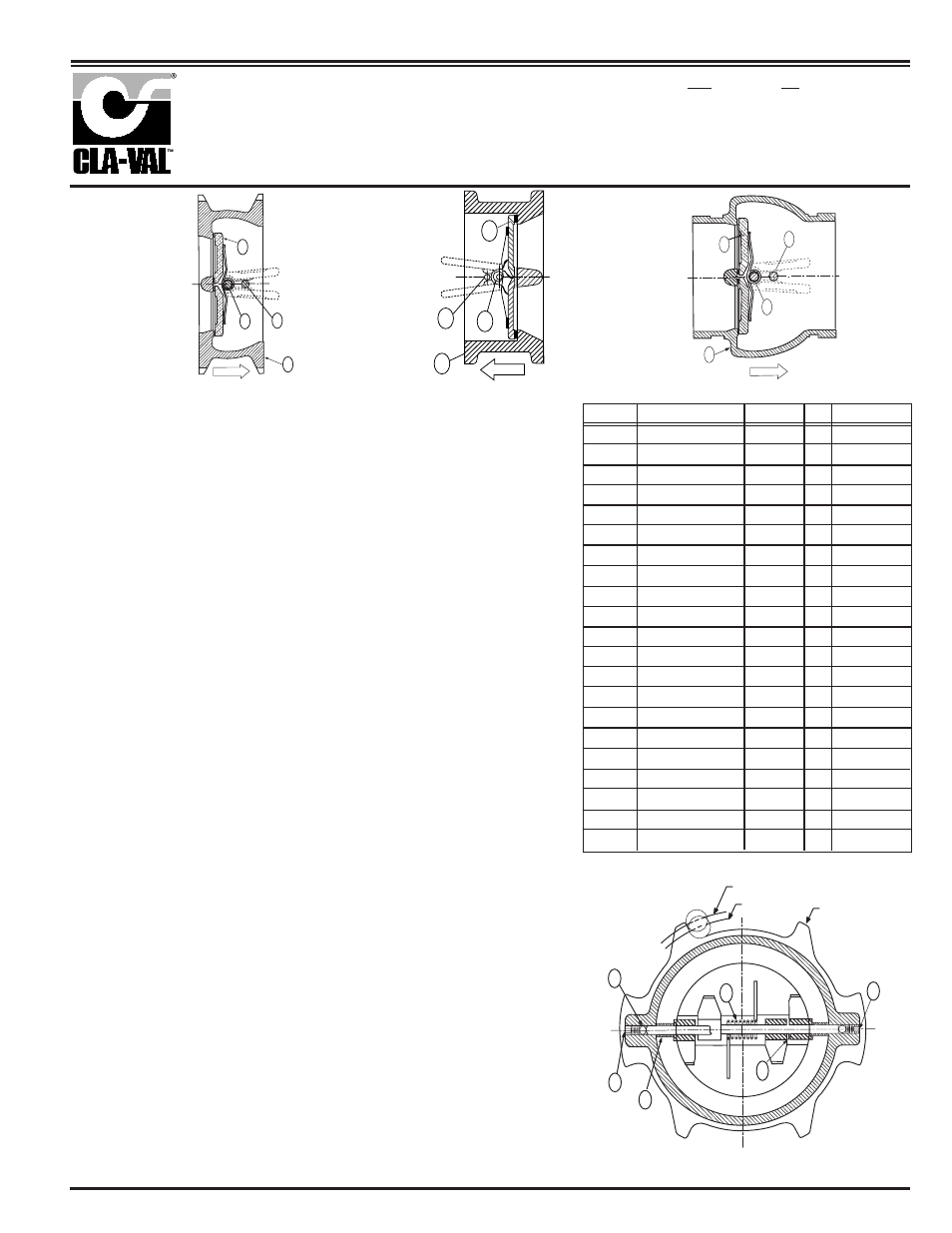
2
5
4
1
FLOW
2
4
1
5
FLOW
FLOW
1
2
5
4
SERIES
INSTALLATION / OPERATION / MAINTENANCE
Two-Door Check Valves
582
INTRODUCTION
The Cla-Val Series 582W, 582G Two Door
Check Valves are ruggedly constructed with
bronze doors and stainless steel trim for years
of trouble-free operation. The valve should be
installed in horizontal or vertical flow up pipes
carrying clean water. the valves have special
springs for operation in blower air service
(Series 582A).
Two door check valves are designed to open
allowing flow in the forward direction and close
rapidly upon flow reversal. The valves are used
to prevent reverse flow through pumps or pip-
ing systems. The size, cold working pressure,
model number, and year of manufacture are
stamped on the nameplate for reference.
The valve is not intended for fluids containing
suspended solids such as wastewater or haz-
ardous fluids.
RECEIVING AND STORAGE
Inspect valves upon receipt for damage in ship-
ment.
When lifting, the valve, always lift by the body
and never lift by the bronze or stainless steel
trim. Lifting eyebolts are provided on NPS 10-
12 (DN 250-300) valves.
The valves should remain boxed, clean and dry
until installed to prevent weather related dam-
age. For storage greater than six months, the
rubber surfaces of the seat should be coated
with a thin film of FDA approved grease.
DESCRIPTION OF OPERATION
The Cla-Val Two Door Check Valves are
designed to prevent reverse flow automatically.
On pump start-up, the flow of water enters the
valve from the seat end (right sided Figure 1)
and forces the two door open until the strike the
disc stop pin. On pump shut-down, the torsion
spring closed the door before flow reversal
takes place.
The valve body is supplied with compact wafer
ends as shown in Figure 1 for installation
between mating flanges.
The only moving parts in the valve are the
doors and spring, which are guided in the body
with a hinge pin and a full open disc stop pin.
The pins are retained in the body by stabiliza-
tion spheres to prevent vibration. The valve has
a resilient seat for drop tight shut off.
INSTALLATION
CAUTION: The flow arrow on the valve body
must point in the direction of flow when the sys-
tem is in operation. The valve can be installed
in horizontal lines with the disc hinge pin in the
vertical position, or in vertical lines with flow up.
Valves for air service (Series 582A require spe-
cial springs to allow full valve opening.
Install valve between standard flanges that cor-
respond to the dimensions given in ANSI B16.1
for 125# flanges or to those given in ISO 7005
for PN10 and PN16 flanges. (See Table 1)
Note: Integrally-cast locating wings around the
exterior, enable the valves to mount between
these different bolt patterns. (See Figure 2) The
number of wings are not provided because the
desired universal fit is accomplished without
them.
The gasket can be rubber or compressed fiber.
Ring gaskets are appropriate for this wafer style
check valve, but full-face flange gaskets may
be substituted. The studs or bolts used should
span the full length of the valve.
Three diameters of straight pipe upstream of
the valve are recommended to prevent turbu-
lent flow through the valve, which can cause
vibration and wear.
When mating the check valve with butterfly iso-
lation valves, the isolation valve must be
installed at least one diameter downstream of
the check valve because, in most sizes the
check valve discs extend beyond the down-
stream flange face and may interfere with the
operation of adjacent valves. In these sizes, a
short run of pipe or spacer is needed between
the check valve and the isolation valve.
INSTALLATION PROCEDURE:
Lower valve between mating flanges. NPS10
(DN 250-300) valves are provided with a lifting
eyebolt to aid in this process. Lubricate the
flange bolts or studs and insert them around the
flange. lightly turn bolts or nuts in graduated
steps using the cross-over tightening method.
Recommended lubricated torques for use with
resilient gaskets are given in Table 1.
Size
Class
Bolt Size Qty Bolt Torque
NPS 2
ANSI 125#
5/8 in.
4
25-75 ft-lb
DN 50
ISO 7005 PN16
M16
4
40-120 N-m
NPS 2.5 ANSI B16.1 125#
5/8 in.
4
25-75 ft-lb
DN 65
ISO 7005 PN16
M16
4
40-120 N-m
NPS 3
ANSI B16.1 125#
5/8 in.
8
25-75 ft-lb
DN 80
ISO 7005 PN16
M16
8
40-120 N-m
NPS 4
ANSI B16.1 125#
5/8 in.
8
25-75 ft-lb
DN 100
ISO 7005 PN16
M16
8
40-120 N-m
NPS 5
ANSI B16.1 125#
3/4 in.
8
40-120 ft-lb
DN 125
ISO 7005 PN16
M16
8
40-120 N-m
NPS 6
ANSI B16.1 125#
3/4 in.
8
40-120 ft-lb
DN 150
ISO 7005 PN16
M20
8
65-200 N-m
NPS 8
ANSI B16.1 125#
3/4 in.
8
50-150 ft-lb
DN 200
ISO 7005 PN10
M20
8
65-200 N-m
DN 200
ISO 7005 PN10
M20
12
65-200 N-m
NPS 10
ANSI B16.1 125#
7/8 in.
12
60-180 ft-lb
DN 250
ISO 7005 PN10
M20
12
65-200 N-m
DN 250
ISO 7005 PN16
M24
12 100-300 N-m
NPS 12
ANSI B16.1 125#
7/8 in.
12
65-200 ft-lb
DN 300
ISO 7005 PN10
M20
12
80-240 N-m
DN 300
ISO 7005 PN16
M24
12 125-375 N-m
Table 1. Flange Bolt Torques
Figure 2 Integrally-Cast Locating Wings
7
6
3
B DIA.
9
8
10
ANSI CLASS 125
BOLT CIRCLE
ISO BOLT CIRCLE
Figure 1 2” thru 12”
Figure 1A 14” thru 60”
Figure 1B 2” thru 12”
Page 1