Bell & Gossett P2001489 Integrated Technologic with Sensorless Control User Manual
Page 23
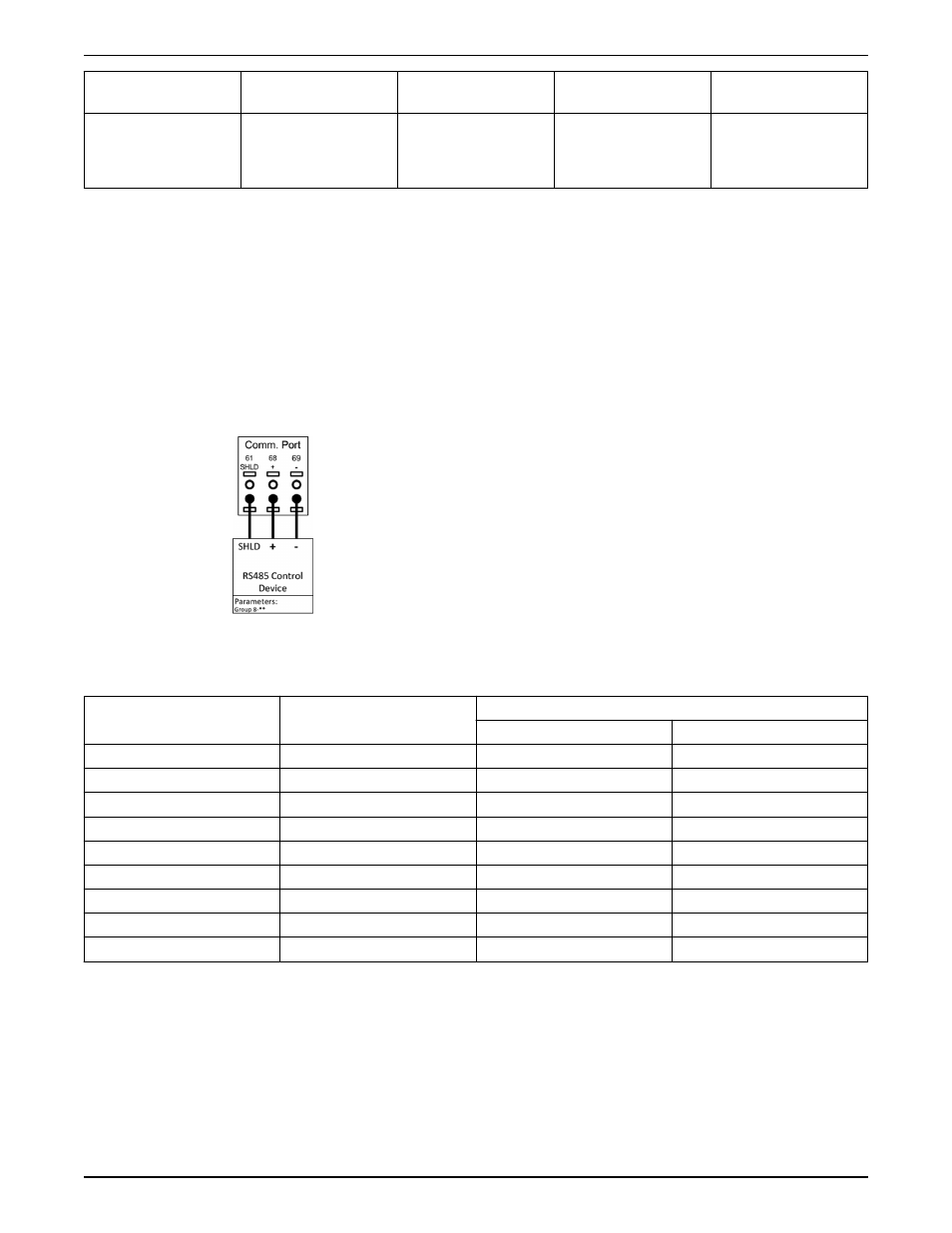
Parameter Number
Parameter Description
For process variable from
BMS/PLC*
For setpoint from BMS/
PLC**
For speed reference from
BMS/PLC***
20-14
Maximum Reference/
Feedback
Maximum transducer
feedback value. For
example, for a 40psi DP
transducer, set to 40 psi.
Maximum reference/
setpoint value. For
example, for a 40psi DP
transducer, set to 40 psi.
NA
* To use AI 54, configure parameters 6-24, 6-25, 6-27 and set 20-00 to Analog Input 54
** To use AI 54, configure parameters 6-24, 6-25, 6-27 and set 3-15 to Analog Input 54
*** To use AI 54, set 3-15 to Analog Input 54
Control from external PLC/BMS through communications port
A BMS or PLC can also be connected to the controller through the communications port.
In this configuration the BMS or PLC can control the drive by overriding the setpoint.
Control cables must be braided screened/shielded and the screen must be connected by
means of a cable clamp at both ends to the metal cabinet of the controller. Be sure to
terminate the bus connections by turning the BUS TER switch to the on position. The BUS
TER switch is located under the LCP as shown in
Figure 5: Configuration switch location
(page 14).
Figure 13: Terminal connections for external control source connected through comm. port
Table 7: Parameter settings for Modbus RTU and BACnet protocols
Parameter Number
Parameter Description
Protocol
Modbus RTU
BACnet
8-02
Control Source
FC Port
FC Port
8-30
Protocol
Modbus RTU
BACnet
8-31
Address
1
1
8-32
Baud Rate
19200
9600
8-33
Parity/Stop bit
Even Parity, 1 Stop bit
No Parity, 1 Stop bit
8-34
Estimated cycle time
0 ms
0 ms
8-35
Minimum Response Delay
10 ms
10 ms
8-36
Maximum Response Delay
5000 ms
5000 ms
8-37
Maximum Inter-Char Delay
0.86 ms
25 ms
The parameters above show an example of typical settings used for Modbus RTU or
BACnet protocols. The parameters must be set according to the devices on the network.
8-32 Baud Rate and 8-33 Parity/Stop Bit should be set to match the other devices on the
network. For detailed communication setup information for Modbus RTU, refer to the
document number MG92B102. For detailed communication setup information for
BACnet, refer to documents MG14C102 and MG11D202. The documents referenced
above are available for download at www.danfoss.com.
Electrical Installation
Integrated Technologic
®
with Sensorless Control INSTRUCTION MANUAL
21