Model lm, lmn, Faults - causes and solutions, Lm ger/fr/eng page 49 – Xylem LMN User Manual
Page 53
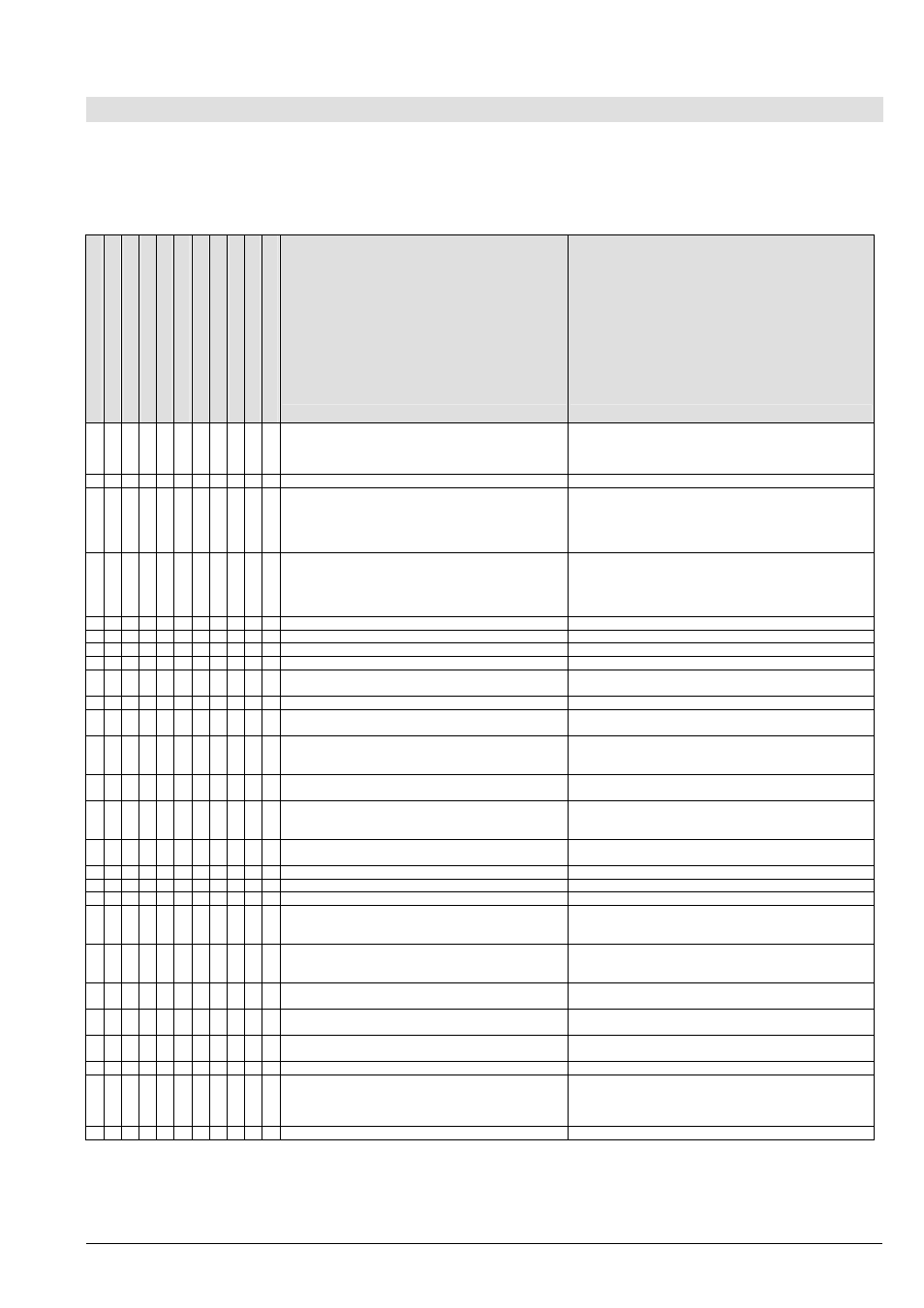
Installation, Operating and Maintenance Instruction
Model LM, LMN
LM ger/fr/eng
Page 49
Revision 06
Article No 771073101
Issue 08/2013
10. Faults - Causes and Solutions
The following notes on causes of faults and how to
repair them are intended as an aid to recognising the
problem. The manufacturer's Customer Service
Department is available to help repair faults that the
operator cannot or does not want to repair. If the
operator repairs or changes the pump, the design data
on the data sheet and chapter 2 of these Operating
Instructions should be particularly taken into account.
If necessary, the written agreement of the
manufacturer must be obtained.
D
ischarge too l
o
w
D
ischarge stops after a ti
me
H
ead too l
o
w
H
ead too hi
gh
D
ri
v
e mechani
sm overl
oaded
P
u
mp not runni
ng qui
etl
y
Temperature i
n
pump too hi
gh
Temperature i
n
shaft seal
ing too hi
gh
Temperature at the beari
ng too hi
gh
P
u
mp l
eaki
ng
Leakage rate at shaft seal
ing too hi
gh
Cause
Solution
■ Back-pressure
too
high
check facility for pollution, open discharge valve
reduce resistance in discharge pipe (e.g. clean filter if
necessary)
use larger impeller (note available motor power)
■
■
■
Back-pressure too low, discharge too low
throttle discharge valve
■ ■ Speed
too
high
reduce
speed
compare speed of motor with specified pump speed (rating
plate)
when adjusting speed (frequency transformer) check reference
value setting
■
■ Speed
too
low
increase speed (check available motor power)
compare speed of motor with specified pump speed (rating
plate)
when adjusting speed (frequency transformer) check reference
value settings
■ ■
■ ■
Flow too little
increase min. flow (open discharge valve, bypass)
■
Flow too big
reduce flow (throttle discharge valve)
■ ■
Impeller diameter too big
use smaller impeller
■
■
Impeller diameter too small
use larger impeller (check available motor power)
■
■
■ ■
Pump and/or pipes not completely filled with liquid
fill
vent
■ ■ ■ Pump
or
suction/intake
pipe
blocked
clean
■
■ Air
in
pipeline
vent
improve course of pipe
■ ■ ■
■ ■
Suction height too big / NPSH of system too small
increase liquid level and admission pressure
reduce resistance in the intake/suction pipe (change course
and rated width, open shut-off valves, clean filters)
■ ■ ■ Air
being
sucked
in
increase
liquid
level
check if suction pipe is vacuum-tight
■ ■ ■
Air being sucked in through shaft sealing
clean sealing pipe
increase sealing pressure
replace shaft sealing
■
■ Direction
of
rotation
is
wrong
swap
over two phases of power supply (to be done by an
electrician)
■
■
■
■
Inner components suffering from wear
replace worn parts
■
■
■
Density and/or viscosity of liquid handled is too high
seek assistance
■
■ Lines and roughness at shaft
replace parts
■
■ Deposits on mechanical seal
clean
replace mechanical seal if necessary
if necessary provide additional rinsing or quench
■
■ Impeller out of balance
remove blocks/deposits
replace impeller if broken or unevenly worn
check shafts to ensure that they are running true
■ ■
■ ■ ■ Forces in pipeline too high (pump unit under strain)
change (support pipes, use compensators, etc.)
is foundation plate/frame properly cast in place?
■ Electricity
supply
not
right
(2-phase running)
check voltage of all phases
check cable connections and fuses
■
Sealing insufficient
tighten screws
replace sealing
■
■ Bearing
damaged
replace
■
Relief fittings insufficient
clean relief openings in impeller
replace worn parts (impeller, split rings)
adjust in line with the system pressure/intake pressure given on
ordering
■ System-related
vibrations
(resonance)
seek
assistance