Model lm, lmn, Start-up, operation, shut down, 5 final control – Xylem LMN User Manual
Page 49: 1 initial start-up, 2 switch on drive, 3 restarting, 4 limits of operation
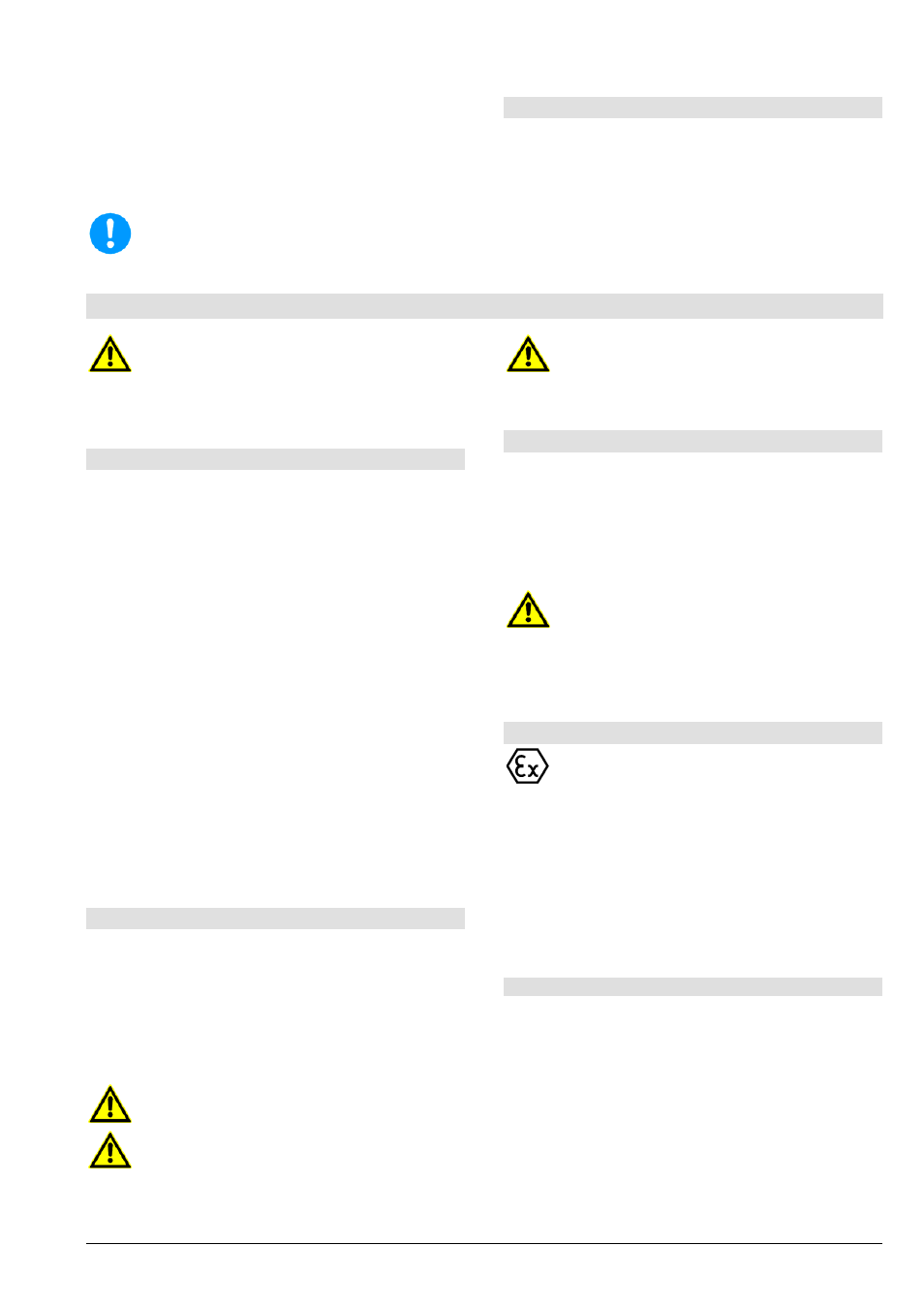
Installation, Operating and Maintenance Instruction
Model LM, LMN
LM ger/fr/eng
Page 45
Revision 06
Article No 771073101
Issue 08/2013
Before starting work, check that the information on the
motor name plate is the same as the local mains
network. The power supply cable of the coupled drive
motor must be connected up in accordance with the
wiring diagram produced by the motor manufacturer.
A protective motor switch must be provided.
The direction of rotation must only be checked
when the pump is full. Dry running will cause
damage to the pump.
5.5 Final Control
It must be possible to turn the unit easily by hand at
the stub shaft.
6. Start-up, Operation, Shut down
The plant may only be started up by people who
are familiar with the local safety regulations and
with these Operating Instructions (especially
with the safety regulations and safety
instructions given here).
6.1 Initial start-up
Before starting up the pump, check, if the following
points were controlled and carried out:
There is no need to lubricate the pump before
starting it up.
Pump and suction pipe must be filled completely
with liquid when starting up.
Turn pump unit once again by hand and check
that it moves smoothly and evenly.
Check that lantern guard sheets are mounted and
that all safety devices are operational.
Switch on any existing sealing or flushing piping.
For quantities and pressures refer to data sheet
and / or order confirmation.
Open valve in suction /intake pipe.
Set discharge side valve to approx. 25% of rated
flow quantity. With pumps with a discharge branch
rated width less than 200, the valve can remain
closed when starting up.
Secure, that unit is electrically connected acc. to
all regulations and with all safety devices.
Check direction of rotation by switching on and off
briefly. It must be the same as the directional
arrow on the drive lantern.
6.2 Switch on drive
Immediately (max. 10 seconds on 50 Hz resp.
max. 7 seconds on 60 Hz currency feed) after
reaching normal operating speed open discharge
valve adjust the required operating point. The
pumping data shown at the type plate resp. in the
data sheet and / or the order confirmation must be
met. Every change is only permitted after talking
with the manufacturer!
Operation with closed valve in the suction and /
or discharge piping is not permitted.
On starting-up without back-pressure, the back-
pressure must be produced through throttling at
the discharge side. After reaching full back-
pressure open valve.
If pump does not reach attended head or if
atypical sounds or vibrations do occur:
Switch off pump (see chapter 6.7) and seek for
causes (see chapter 10).
6.3 Restarting
Basically, the same procedure should be followed as
for starting up for the first time. However, there is no
need to check the direction of rotation and the
accessibility of the pump unit.
The pump should only be automatically restarted if it
has been made sure that the pump has remained
filled whilst stand by.
Be particularly careful not to touch hot machine
parts and when working in the unprotected shaft
seal area. Remember that automatically
controlled systems may switch themselves on
suddenly at any time. Suitable warning signs
should be affixed.
6.4 Limits of Operation
The operating limits of the pump / unit regarding
pressure, temperature, performance and speed
are shown in the data sheet and / or order
confirmation and must be observed under any
circumstances!
Do not exceed the output given on the motor
name plate.
Avoid sudden changes in temperature
(temperature shocks).
The pump and motor should run evenly and
without vibrations; check at least once a week.
6.4.1 Flow min. / max.
If no other data are given in the curves or data sheets,
the following is valid:
Q
min
= 0,1 x Q
BEP
for short time operation
Q
min
= 0,3 x Q
BEP
for continuous operation
Q
max
= 1,2 x Q
BEP
for continuous operation *)
Q
BEP
= Flow in Best Efficiency Point
*) on condition that NPSH
facility
> (NPSH
pump
+ 0,5 m)