Model lm, lmn, Description, 1 design – Xylem LMN User Manual
Page 43: 2 pump coding, 3 shaft sealing
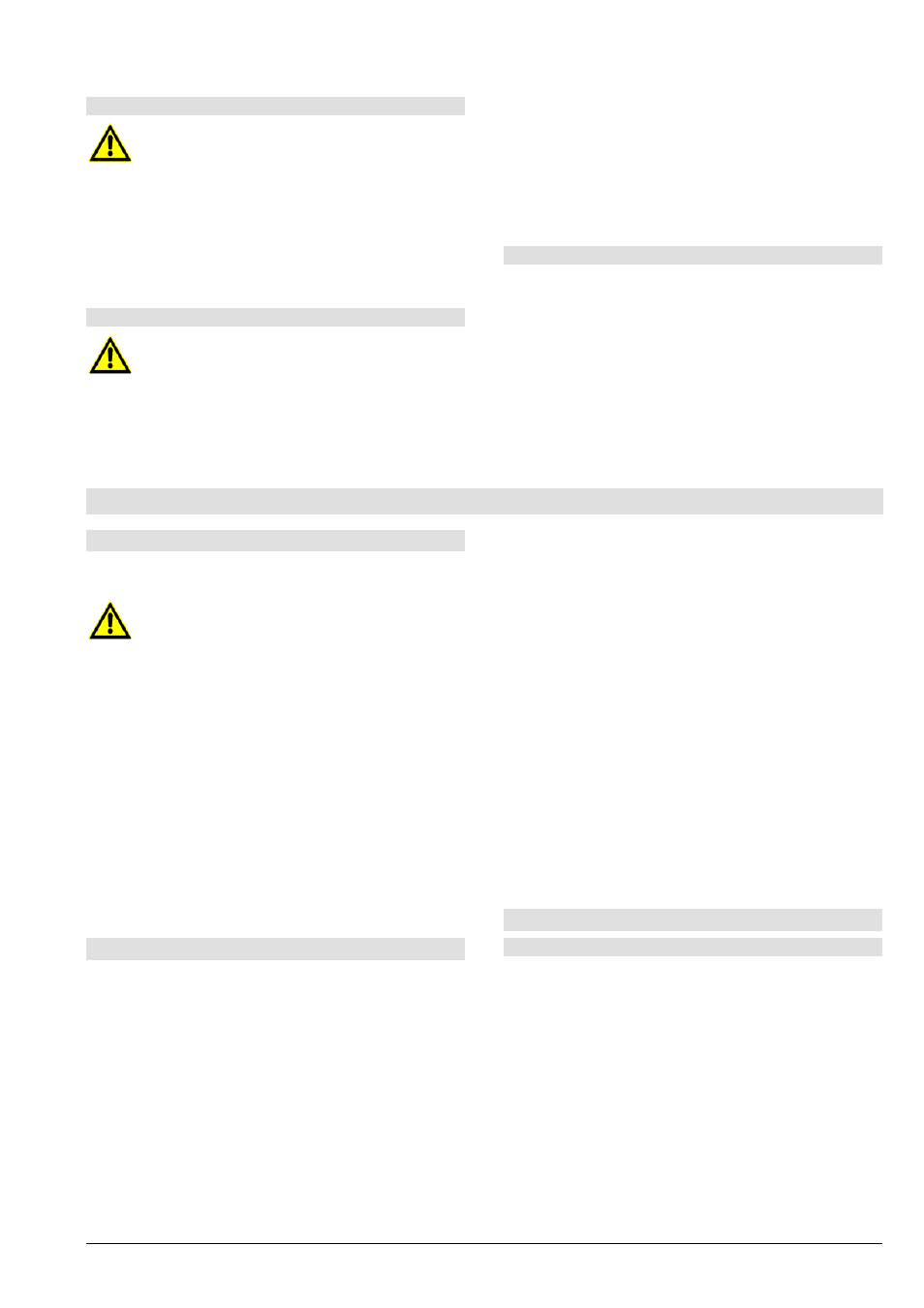
Installation, Operating and Maintenance Instruction
Model LM, LMN
LM ger/fr/eng
Page 39
Revision 06
Article No 771073101
Issue 08/2013
2.7.2 Permitted Nozzle Loads and Torques
Basically the suction and discharge piping must
be designed in such way, that as little forces as
possible are effective to the pump. If that is not
possible, the values shown in chapter 3.5 must
not be exceeded under any circumstances. This
is valid for the operation as well as for the
standstill of the pump and therefore for all
possible pressures and temperatures of the
unit.
2.7.3 NPSH
The pumped liquid must have a min. pressure
NPSH at the impeller inlet, so that cavitation
free work is secured resp. a "break off" of the
pump flow is prevented. This condition is
fulfilled, when NPSH-value of the system
(NPSHA) lies above NPSH-value of the pump
(NPSHR) under all operating conditions.
Attentention must especially be piad to the NPSH-
value on pumping liquids near the vapour pressure. If
the NPSH-value of the pump remains under, this can
lead from damage of the material due to cavitation to
destruction by overheating.
The NPSH-value of the pump (NPSHR) is shown in
the curves of every pump type.
2.7.4 Back Flow
In systems where pumps are operating in closed
circuits under pressure (gas cushions, steam
pressure), the pressure of the gas cushion must not
be reduced via the pump, since the back flow speed
may be much higher than the operating speed, which
would destroy the unit.
3. Description
3.1 Design
The pumps of Model LM and LMN are single-stage
volute casing pumps in block design with motor.
These pumps are not qualified for dangerous or
inflammable fluids. Not qualified for the
operation in areas subject to explosion hazards.
The motors comply with DIN 42677-IM B5. Motor and
pump shaft are coupled rigidly.
The permitted application conditions and design
details of the delivered pump are shown in the
attached data sheet and / or the order confirmation
(see Design Coding System in chapter 3.2).
Installation position: LM and LMN-pumps are
intended for use with horizontal shaft, discharge up.
Installation positions deviating therefrom must be
approved by the manufacturer.
Max. operating pressure: see chapter 3.8.
The appropriate sectional drawing of the supplied
pump as well as the pump weight and the complete
pump unit weight are shown in the appendix.
3.2 Pump Coding
Due to the coding on the data sheet and / or order
confirmation all information regarding the delivered
pump can be found in this Installation, Operation and
Maintenance Instruction, e.g.:
LMN 65 - 250 U1 V N 370 2
(0)
(1) (2) (3)
(4) (5) (6)
(7)
Position (0) - Name of Model
LMN / LM - block pump design
Position (1) - Discharge nozzle in mm
Position (2) - Nominal diameter of impeller in mm
Position (3) - Design of the shaft sealing
Single mechanical seal acc. DIN 24960 l1k /
EN 12756 Form U, unbalanced
U1 Carbon / Silicon carbide / EPDM
(BQ1EGG)
U2 Carbon / Silicon carbide / Viton (BQ1VGG)
U3 Silicon carbide / Silicon carbide / Viton
(Q1Q1VGG)
Position (4) - Impeller material
N = Cast iron - Model LMN (0.6020), Model
LM (0.6025)
S = Bronze (2.1050.01), only at model LM
V = Stainless steel (1.4404), only at model
LMN
Position (5) - Pump casing material
N = Cast iron - Model LMN (0.6020), Model
LM (0.6025)
Other materials are not available.
Position (6) - Motor power (in 1/10 kW)
Position (7) - Number of motor contacts - 2 pole =
2950 rpm resp. 4 pole = 1450 rpm
3.3 Shaft Sealing
3.3.1 Structure of the mechanical seal
This shaft seal is a single mech. seal with installation
dimensions according to EN 12756 (DIN 24960)
design "K". API plan 02 / ISO plan 00.
No additional flushing of the seal chamber is
necessary. The seal casing where the mechanical
seal is located must always be filled with liquid.
For a description of materials and operational ranges
of the mech. seals supplied, please refer to the data
sheet in the Operation Instructions and order
confirmation.
For the internal structure of the mechanical seal see
the following sectional drawings.