GC EUROPE Fujivest Super User Manual
Page 32
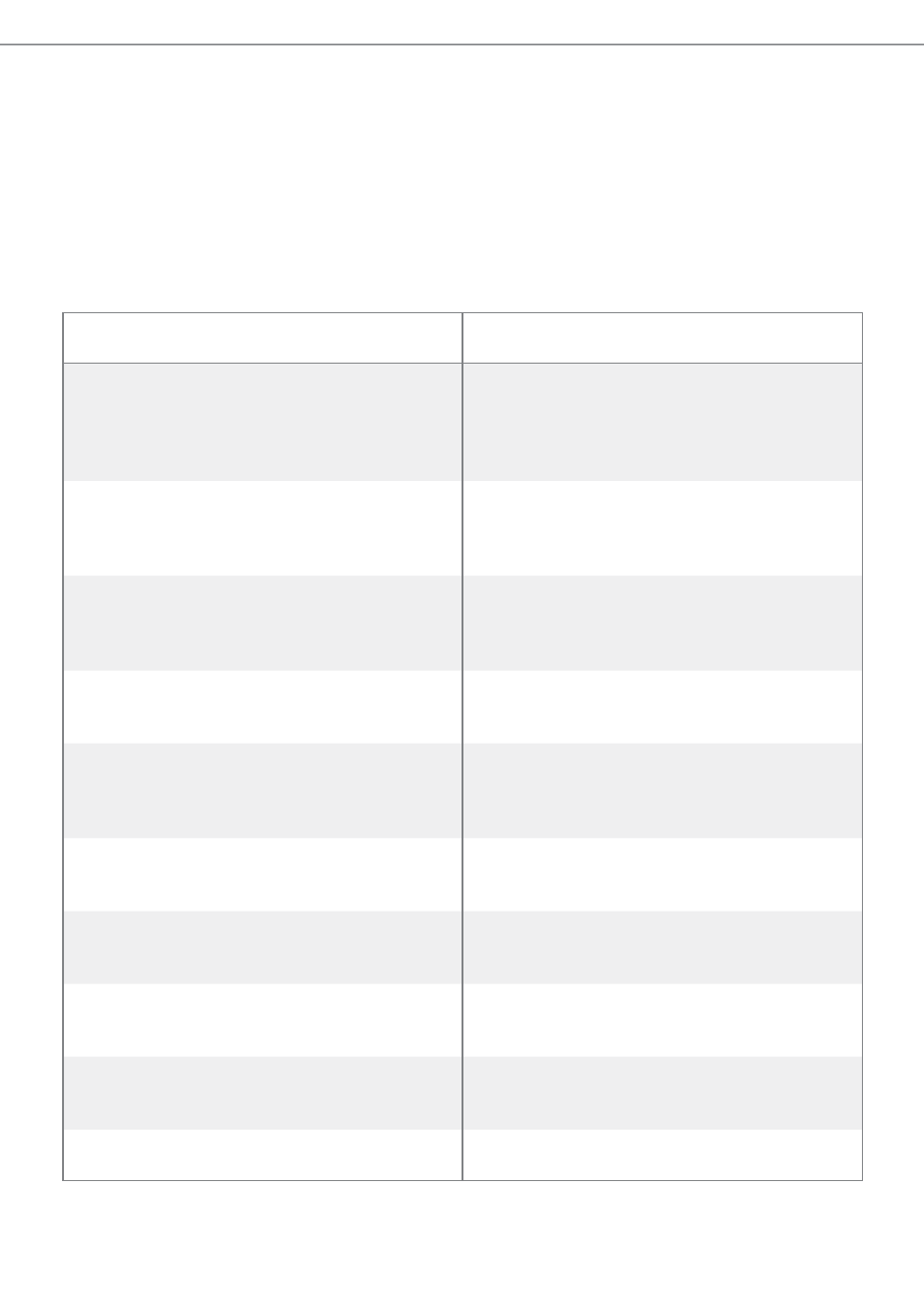
32
Cause
Remedy
- Insufficient mixing/spatulation
- Mix as recommended in the instruction
manual to ensure that the complete setting
reaction occurs. Replace mixing equipment
if worn
- Rate of burnout too fast (plastic parts)
- Decrease heating rate or try the step
heating procedure as detailed in the
instructions for use
- End (final) burnout temperature too high or
heat soak too long (over 1.5 hours)
- Reduce end temperature; do not hold at the
final temperature for more than 1.5 hours.
Check calibration of burn out furnace
- Overheating alloy melt
- Review both the alloy and casting equipment
manufacturer’s instructions and guidelines
- Defective pattern and/or pattern material
- Use only high quality pattern materials such
as GC Pattern Resin and wax taking care to
avoid contamination with debris
- Wet pattern, use of surface wetting agents
- If a surface wetting agent is used ensure that
it is allowed to thoroughly dry
- Incorrect powder/liquid ratio
- Use correct ratio as stated in the instructions
for use
- Impurities in wax or pattern resin
- Work cleanly and ensure that the pattern
material is free of impurities
- Air bubble entrapped
- Avoid air entrapment by using a thin stream
when investing
- Insufficient vacuum during mixing
- Check efficiency of vacuum on mixing unit
4
Rough casting surfaces
(pits, nodules and porosities)