16v picotlynx, 4a: non-isolated dc-dc power modules, Data sheet – GE Industrial Solutions 16V PicoTLynx 4A User Manual
Page 14: Test configurations, Design considerations, Input filtering, Output filtering, Figure 50. output ripple and noise test setup, The 16v picotlynx, Feature described later in this data sheet
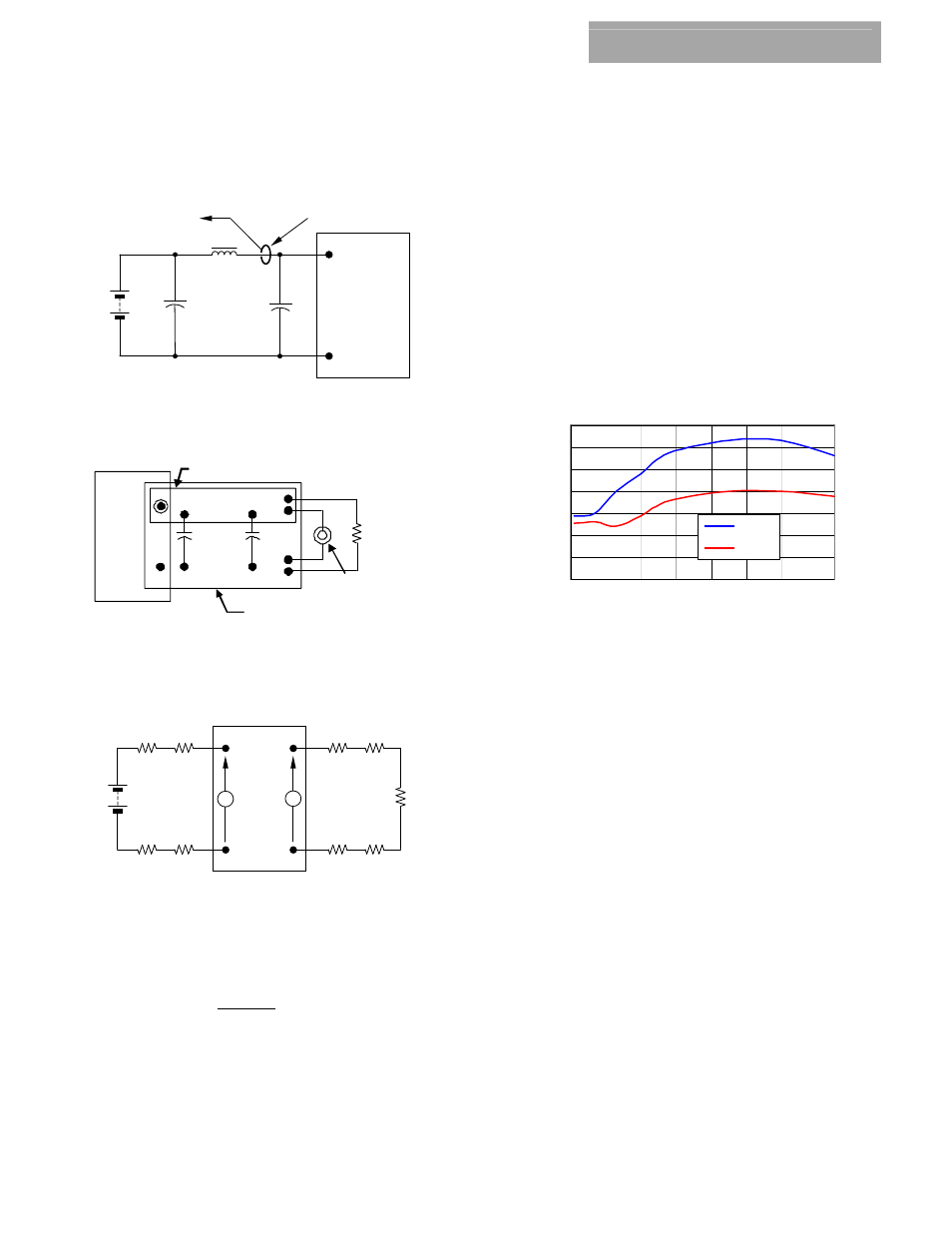
GE
Data Sheet
16V PicoTLynx
TM
4A: Non-Isolated DC-DC Power Modules
8Vdc –16Vdc input; 0.6Vdc to 8.0Vdc output; 4A Output Current
September 10, 2013
©2013 General Electric Company. All rights reserved.
Page 14
Test Configurations
TO OSCILLOSCOPE
CURRENT PROBE
L
TEST
1μH
B
A
TTE
R
Y
C
S
1000μF
Electrolytic
E.S.R.<0.1
Ω
@ 20°C 100kHz
2x100μF
Tantalum
V
IN
(+)
COM
NOTE: Measure input reflected ripple current with a simulated
source inductance (L
TEST
) of 1μH. Capacitor C
S
offsets
possible battery impedance. Measure current as shown
above.
C
IN
Figure 49. Input Reflected Ripple Current Test Setup.
NOTE: All voltage measurements to be taken at the module
terminals, as shown above. If sockets are used then
Kelvin connections are required at the module terminals
to avoid measurement errors due to socket contact
resistance.
Vo+
COM
0.1uF
RESISTIVE
LOAD
SCOPE USING
BNC SOCKET
COPPER STRIP
GROUND PLANE
10uF
Figure 50. Output Ripple and Noise Test Setup
V
O
COM
V
IN
(+)
COM
R
LOAD
R
contact
R
distribution
R
contact
R
distribution
R
contact
R
contact
R
distribution
R
distribution
V
IN
V
O
NOTE: All voltage measurements to be taken at the module
terminals, as shown above. If sockets are used then
Kelvin connections are required at the module terminals
to avoid measurement errors due to socket contact
resistance.
Figure 51. Output Voltage and Efficiency Test Setup.
η =
V
O
. I
O
V
IN
. I
IN
x
100
%
Efficiency
Design Considerations
Input Filtering
The 16V PicoTLynx
TM
4A module should be connected to a low
ac-impedance source. A highly inductive source can affect
the stability of the module. An input capacitance must be
placed directly adjacent to the input pin of the module, to
minimize input ripple voltage and ensure module stability.
To minimize input voltage ripple, ceramic capacitors are
recommended at the input of the module. Figure 52 shows the
input ripple voltage for various output voltages at 4A of load
current with 1x10 µF or 1x22 µF ceramic capacitors and an
input of 12V.
Inp
ut Ripple Vo
ltage (mVp-p)
0
50
100
150
200
250
300
350
0.5
1.5
2.5
3.5
4.5
5.5
6.5
7.5
1x10uF
1x22uF
Output
Voltage
(Vdc)
Figure 52. Input ripple voltage for various output voltages
with 1x10 µF or 1x22 µF ceramic capacitors at the input (4A
load). Input voltage is 12V.
Output Filtering
The 16V PicoTLynx
TM
4A modules are designed for low output
ripple voltage and will meet the maximum output ripple
specification with 0.1 µF ceramic and 10 µF ceramic
capacitors at the output of the module. However, additional
output filtering may be required by the system designer for a
number of reasons. First, there may be a need to further
reduce the output ripple and noise of the module. Second, the
dynamic response characteristics may need to be customized
to a particular load step change.
To reduce the output ripple and improve the dynamic
response to a step load change, additional capacitance at the
output can be used. Low ESR polymer and ceramic capacitors
are recommended to improve the dynamic response of the
module. Figure 53 provides output ripple information for
different external capacitance values at various Vo and for a
load current of 4A. For stable operation of the module, limit the
capacitance to less than the maximum output capacitance as
specified in the electrical specification table. Optimal
performance of the module can be achieved by using the
Tunable Loop
TM
feature described later in this data sheet.