Diagnostic information – MITSUBISHI ELECTRIC 2408f User Manual
Page 10
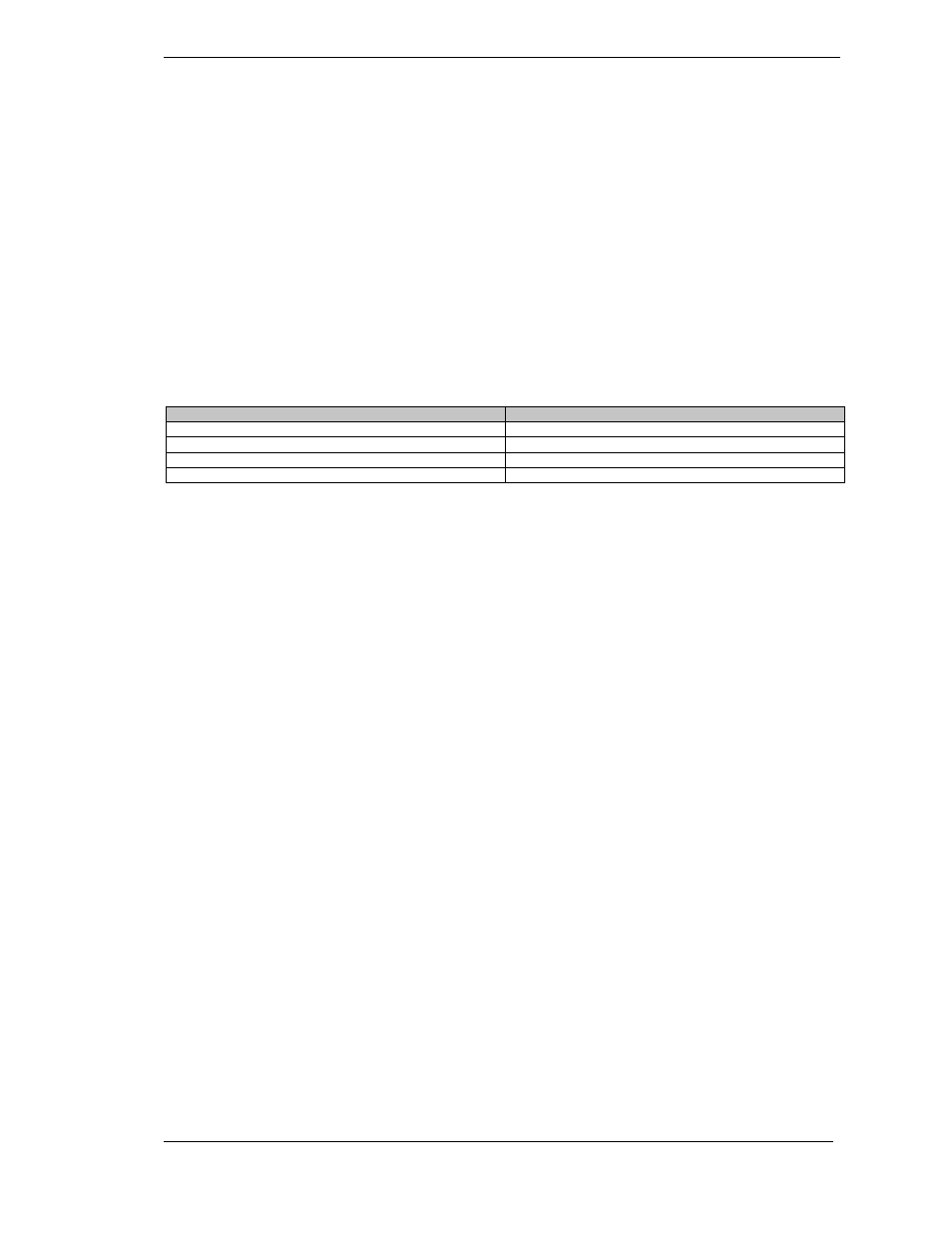
2408
f
& 2404
f
PROFIBUS Communications Handbook Controller Set Up & Network Configuration
2408
f
and 2404
f
PROFIBUS Communications Handbook 4-3
N
ETWORK
C
ONFIGURATION
Having wired and configured the controller, the master PLC or PC based supervisory package must be configured to set-up
the parameters that it will be able to read and write to. This is known as ‘network configuration’.
The network is configured by importing ‘GSD’ files into your Master PROFIBUS network configuration software: This
should be explained in your network configuration software documentation. ‘GSD’ is an acronym of a German phrase
meaning ‘Device Database’.
The GSD files supplied with your 2408
f
and 2404
f
controllers are created using a Windows-based configuration tool. This
software is also separately available under ordering code PROF-ENG.
Two standard GSD files, are supplied on the disc:
EURO2400.GSD - standard parameter mapping. This is the default file, which is pre-configured for commonly used
parameters, as shown in Table 4-1 below.
EURD2400.GSD - standard parameter mapping with ‘demand data’, which allows random read/write to any parameter
within the controller. This is configured with the same default parameters.
PROFIBUS Input Data
PROFIBUS Output Data
Process Variable
0;
Setpoint 1
0
Working Setpoint
<0
Setpoint 2
0
Output 1
0
Setpoint Select
)
Summary Output Status Word
Acknowledge all Alarms
Table 4-1: Default Parameters.
The Summary Output Status Word is shown in Table 4-2., see ‘PROFIBUS DIAGNOSTICS’
It is possible to edit the above files or create new files using the Windows configurator.
The Master network configuration software uses the GSD files to produce a further file which is downloaded into your master
PLC or PC supervisory package. Once the configuration file has been downloaded, you can set the network running. If all is
well, the ‘REM’ beacon on the controller will start to flash, indicating that the data exchange is proceeding. The
66
parameter in the
+ list will show 59.. Input data will then be transferred from the controller to the master, and output
data will be transferred from the master to the controller.
If all 2400
f
controllers are of the same type only one GSD file needs to be configured.
F
LOATING
P
OINT
D
ATA
F
ORMATS
Data is returned or sent in the form of a single 16 bit integer value (register). Since the controllers use and display floating
point values, these are translated into integers in one of two ways, selected in controller configuration.
Full Resolution: The value is returned as a ‘scaled integer’, such that 999.9 is returned or sent as 9999; 12.34 is encoded as
1234. The control program in the PROFIBUS master must convert the numbers into floating point values if required. This is
the recommended format and is the factory default.
Integer Resolution. The floating point value is returned as a rounded integer, with the fractional part discarded. For example
999.9 would be returned as 1000; 12.34 would be returned as 12. Similar rules apply to output operations, although note that
it is only possible to send integer values so that setpoint values such as 11.5 cannot be used and so either 11 or 12 would have
to be chosen instead.