Motor & gearbox – Grizzly G0709 User Manual
Page 61
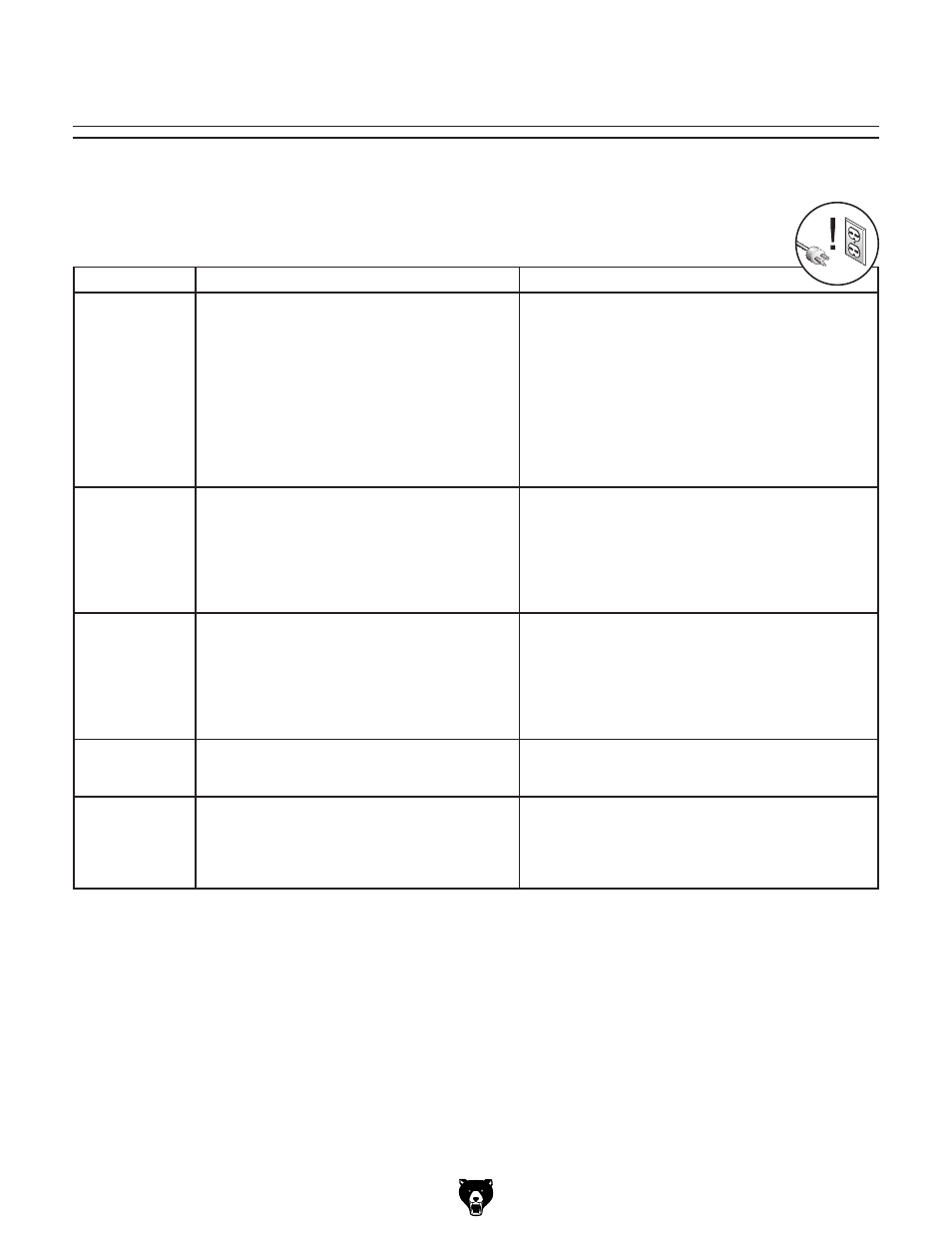
Model G0709 (Mfg. Since 5/11)
-59-
symptom
possible Cause
possible solution
Motor will not
start.
1. stop button not reset.
2. Main power panel switch is
OFF.
3. Circuit breaker or fuse has tripped.
4. no voltage or open connection.
5. Capacitor is at fault.
6. spindle on/oFF switch is at fault.
7. power switch or magnetic contactor is at
fault.
8. Motor is at fault.
1. reset stop button.
2. turn the main power panel switch
ON.
3. seek an electrician to troubleshoot and repair the
power supply.
4. test circuit, replace wires and connections as
required (refer to
Wiring, page 74).
5. replace capacitor.
6. replace switch.
7. replace power switch or magnetic contactor.
8. replace motor.
Fuses or circuit
breakers trip
open.
1. short circuit in power cord or plug.
2. short circuit in motor or loose connections.
3. incorrect fuses or circuit breakers in power
supply.
1. inspect cord or plug for damaged insulation and
shorted wires, repair or replace as required.
2. inspect all connections on motor for loose or
shorted terminals or worn insulation. repair as
required (refer to
Wiring, page 74).
3. install correct fuses or circuit breakers.
Machine is
loud; belt slips
when cutting.
overheats or
bogs down in the
cut.
1. excessive depth of cut.
2. rpM or feed rate wrong for operation.
3. dull bit.
4. Belt is slipping.
5. Belt is at fault.
1. decrease depth of cut.
2. refer to rpM feed rate chart for appropriate rates,
(
page 41).
3.
sharpen or replace bit.
4. remove grease or oil on belt tighten belt adjustment
(
page 70).
5. replace belt.
gear change
levers will not
shift into position.
1. gears not aligned in headstock.
1. rotate spindle by hand until gear falls into place.
loud, repetitious
noise coming
from machine
at or near the
motor.
1. pulley set screws or keys are missing or
loose.
2. Motor fan is hitting the cover.
1. inspect keys and set screws. replace or tighten if
necessary.
2. replace fan and cover as required.
Motor & Gearbox
Review the troubleshooting and procedures in this section if a problem develops with your machine. If you
need replacement parts or additional help with a procedure, call our Technical Support at (570) 546-9663.
Note: Please gather the serial number and manufacture date of your machine before calling.
SEcTION 7: SERvIcE