Emerson Process Management 1051 User Manual
Page 20
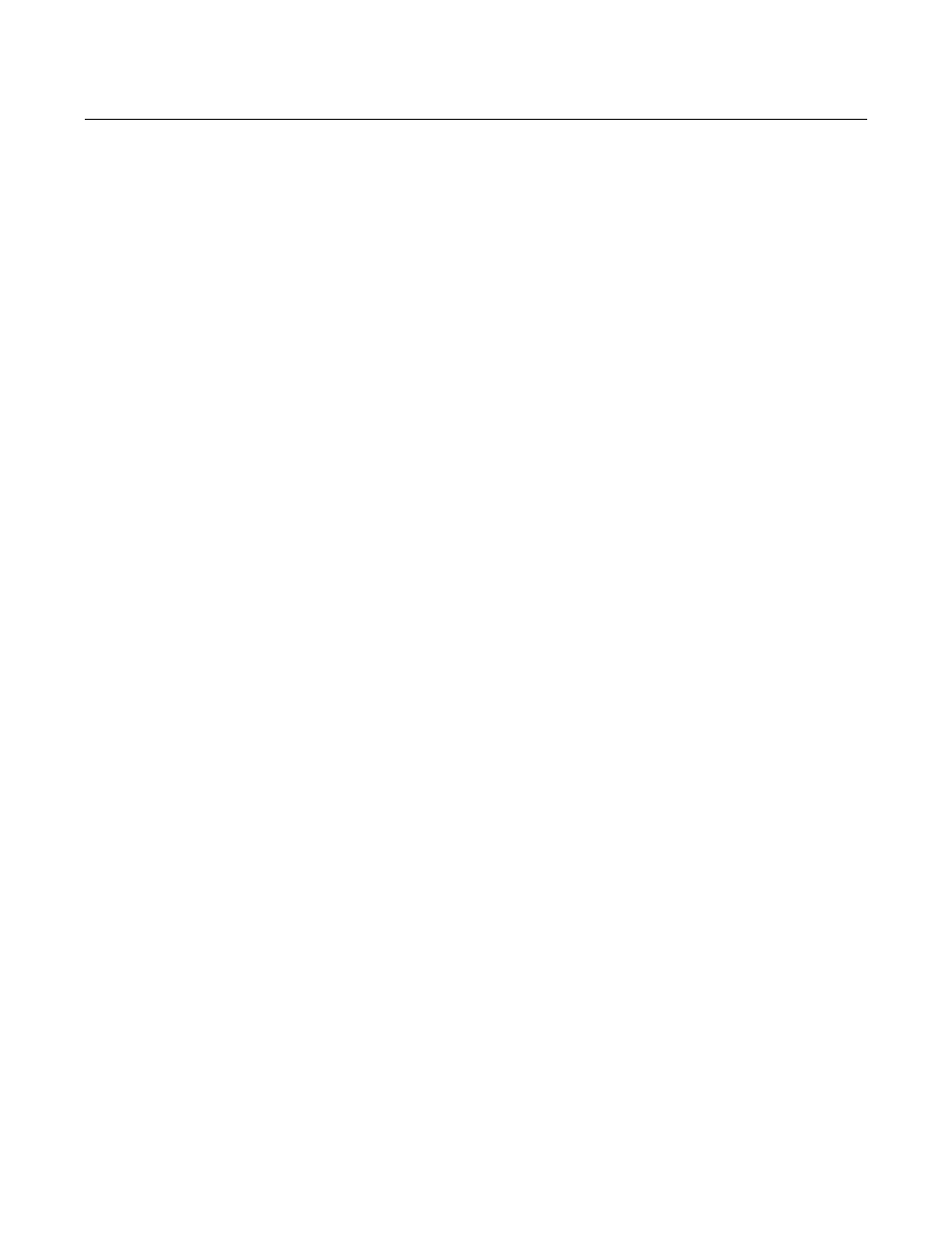
Instruction Manual
D100320X012
1051 and 1052 H & J Actuators
October 2012
20
(key 71), the thrust bearing races (key 72), and the spring seat (key 13) onto the adjustor. Install this assembly into
the spring barrel (key 12). After first cleaning and then coating the set screw (key 75) with thread-locking adhesive
(high strength) (key 77), secure the adjustor with the set screw (key 75).
b. Coat the tapered end of the diaphragm rod (key 10) and the threads of the cap screw (key 9) with lithium grease
(key 76). Bolt the diaphragm plate (key 4) to the diaphragm rod with the cap screw (key 9). Tighten the cap
screw to the torque value listed in table 11.
c. Be certain the travel stops (key 8) are located as shown in figure 11.
d. Install the spring (key 11) into the spring barrel. Install the diaphragm plate and diaphragm rod into the actuator.
Attach the hex nut (key 58), turnbuckle (key 57), hex nut (key 16), and rod end bearing (key 17) to the
diaphragm rod.
e. Install the diaphragm (key 3).
f. Place the upper diaphragm casing (key 1) on the lower diaphragm casing (key 2). If necessary, rotate the lower
bearing seat (key 73) so that the upper diaphragm casing travel stop will not contact the diaphragm when the
casing cap screws (key 5) are tightened. Secure the upper diaphragm casing with the cap screws and hex nuts
(keys 5 and 6) in a criss-cross pattern to the torques shown in table 11. Be sure the warning nameplate is in place
on the casing.
3. If the bearing (key 67) was removed, press in the new bearing. The end of the bearing should be flush with the
outside of the mounting bracket or mounting plate (key 22).
4. For an actuator with an H mounting adaptation, install the output shaft (key 87) through the mounting plate (key
22) and secure it with the retaining ring (key 88). Then, attach the mounting plate and output shaft assembly to the
actuator housing (key 20) with the cap screws (key 23). Tighten the cap screws to the appropriate torque value
listed in table 11.
5. For an actuator with a J mounting adaptation, refer to figures 12 and 13. Install the output shaft (key 87) with
attached coupling (key 90) through the mounting bracket (key 22) and secure it with the retaining ring (key 88).
Attach the mounting bracket and output shaft assembly to the actuator housing (key 20) with the cap screws (key
23). Tighten the cap screws to the appropriate torque value listed in table 11.
6. For an actuator with a J mounting adaptation and a 50.8 mm (2-inch) output shaft, refer to figure 14. Install the
output shaft (key 87) with attached coupling (key 90) through the mounting plate (key 22) and secure it with the
retaining ring (key 88). Attach the mounting plate and output shaft assembly to the actuator housing with the cap
screws (key 23). Tighten the cap screws to the appropriate torque value listed in table 11.
7. Apply lithium grease (key 76) to the output shaft splines. Then, align the lever (key 27) and output shaft so that the
marking that was made in step 6 or 7 of the Disassembly procedure is oriented correctly. Slide the lever into place.
When installing the lever, align the bolt holes in the lever as close as possible with the hole in the rod end bearing
(key 17). Temporarily rotate the lever and output shaft until the rod end bearing no longer interferes with further
installation of the lever. Then, slide the lever as far as it can go onto the output shaft.
8. Clamp the lever to the output shaft with the cap screw (key 28). Tighten the cap screw to the torque value listed in
table 11.
9. For 1052 actuators, complete the Initial Compression portion of the Adjustment section before proceeding.
10. Rotate the lever (key 27) to align with the rod end bearing (key 17). This connection can be aided by stroking the
actuator off its up travel stop with a regulated air source.