Description, Instruction manual – Emerson Process Management 1051 User Manual
Page 2
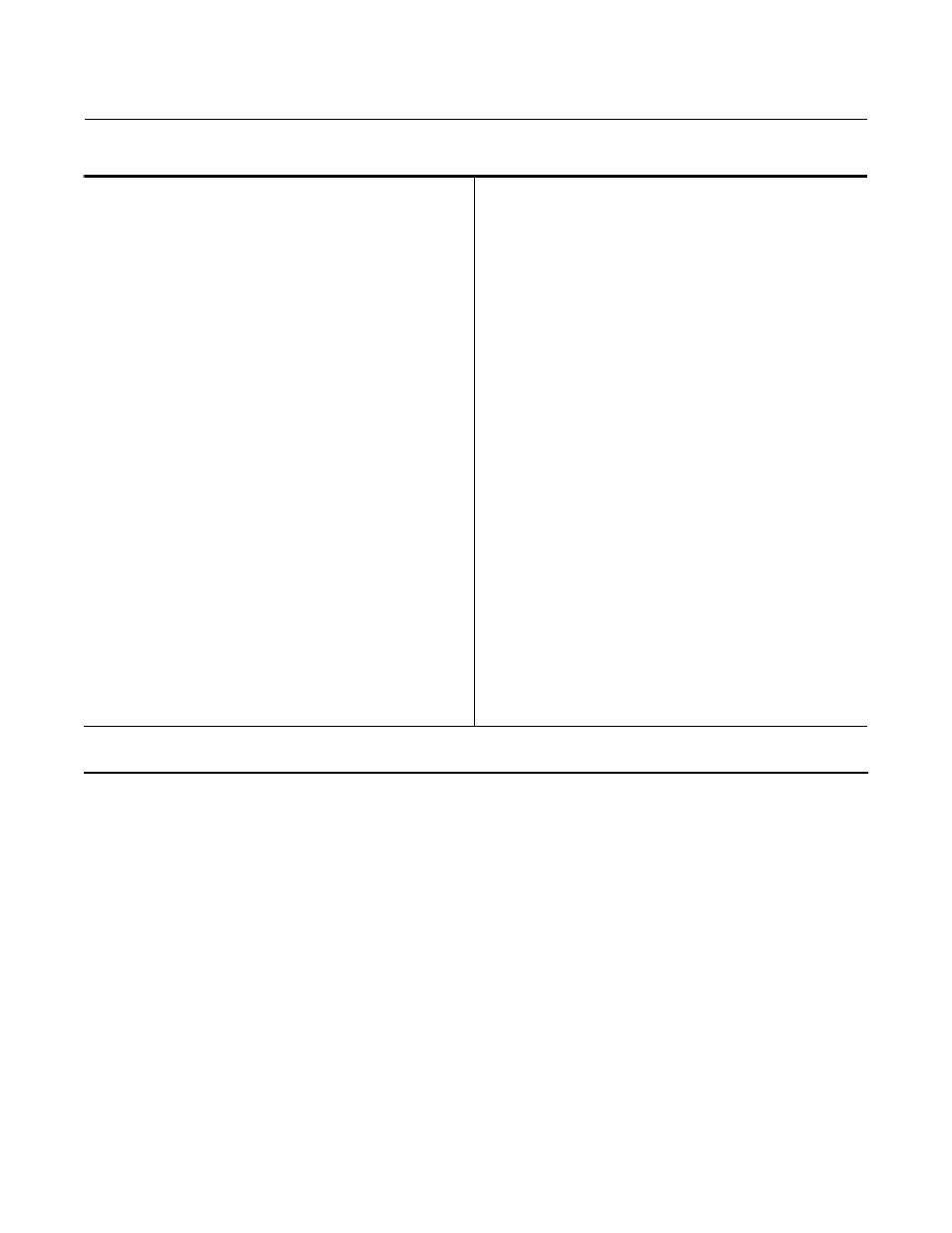
Instruction Manual
D100320X012
1051 and 1052 H & J Actuators
October 2012
2
Table 1. Fisher 1051 and 1052 Actuator Specifications
Operation
Direct Acting: Increasing loading pressure extends
the diaphragm rod out of the spring barrel
Service:
1051: For on-off or throttling service with positioner
1052: For on-off or throttling service with or without a
positioner
Actuator Sizes
1051: 40, and 60
1052: 40, 60, and 70
Maximum Diaphragm Sizing Pressure
(2)(3)
Size 40: 4.5 bar (65 psig)
Size 60: 2.8 bar (40 psig)
Size 70: 3.8 bar (55 psig)
Maximum Diaphragm Casing Pressure
(2)(3)
Size 40: 5.2 bar (75 psig)
Size 60: 3.4 bar (50 psig)
Size 70: 4.5 bar (65 psig)
Maximum Valve Shaft Rotation
90, 75, or 60 deg with optional stops
Torque Limits (mm)
(4)
Limited by maximum diaphragm sizing pressure or
tables 2 and 3, whichever is less
Stroking Time
Dependent on actuator size, rotation, spring rate,
initial spring compression, and supply pressure. If
stroking time is critical, consult your Emerson Process
Management sales office
Material Temperature Capabilities
(3)
Nitrile Diaphragm or O-Rings
(1)
: -40 to 82_C
(-40 to 180_F)
Silicone Diaphragm: -40 to 149_C (-40 to 300_F)
Travel Indication
Graduated disc and pointer combination located on
actuator end of valve shaft
Pressure Connections
1/4 NPT internal
Mounting Positions
See figure 10
Approximate Weights
See table 8
Additional Specifications
For casing pressure ranges and for material
identification of the parts, see the Parts List
1. Nitrile O-rings are used in optional top-mounted handwheel, adjustable down travel stop, and adjustable up travel stop assemblies.
2. Use this value to determine the maximum torque output allowed.
3. The pressure / temperature limits in this manual and any applicable standard or code limitation for valve should not be exceeded.
4. Exceeding any torque requirements could damage the actuator and impair safe operation.
Do not install, operate, or maintain a 1051 or 1052 actuator without being fully trained and qualified in valve, actuator,
and accessory installation, operation, and maintenance. To avoid personal injury or property damage, it is important
to carefully read, understand, and follow all the contents of this manual, including all safety cautions and warnings. If
you have any questions about these instructions, contact your Emerson Process Management sales office before
proceeding.
Description
1051 and 1052 diaphragm rotary actuators are pneumatic spring-return actuators for use with rotary-control valves
and other equipment. The 1051 actuator can be used for on-off service, or it can be used for throttling service when
equipped with a valve positioner. The 1052 actuator can be used for on-off service, or it can be used for throttling
service when equipped with or without a valve positioner. The 1052 actuator spring is adjustable.
The H mounting adaptation permits the actuator to be used with equipment other than Fisher valve bodies. The
mounting brackets and couplings for rotary actuation are user-provided. This mounting adaptation includes a
flat-surface mounting plate that is drilled and tapped for attaching the user-provided bracket. Cap screws for attaching
the bracket are provided. H mounting also includes an output shaft (with milled flats) to provide the Double D rotary
output either directly or through a user-provided coupling. Output shaft diameters and torque limits are listed in table
2. Dimensional information for the mounting plate and output shaft are shown in figures 4, 5, and 6.