Users manual, Mc100, 7 operating the mc100 – Watson-Marlow MC100 User Manual
Page 18
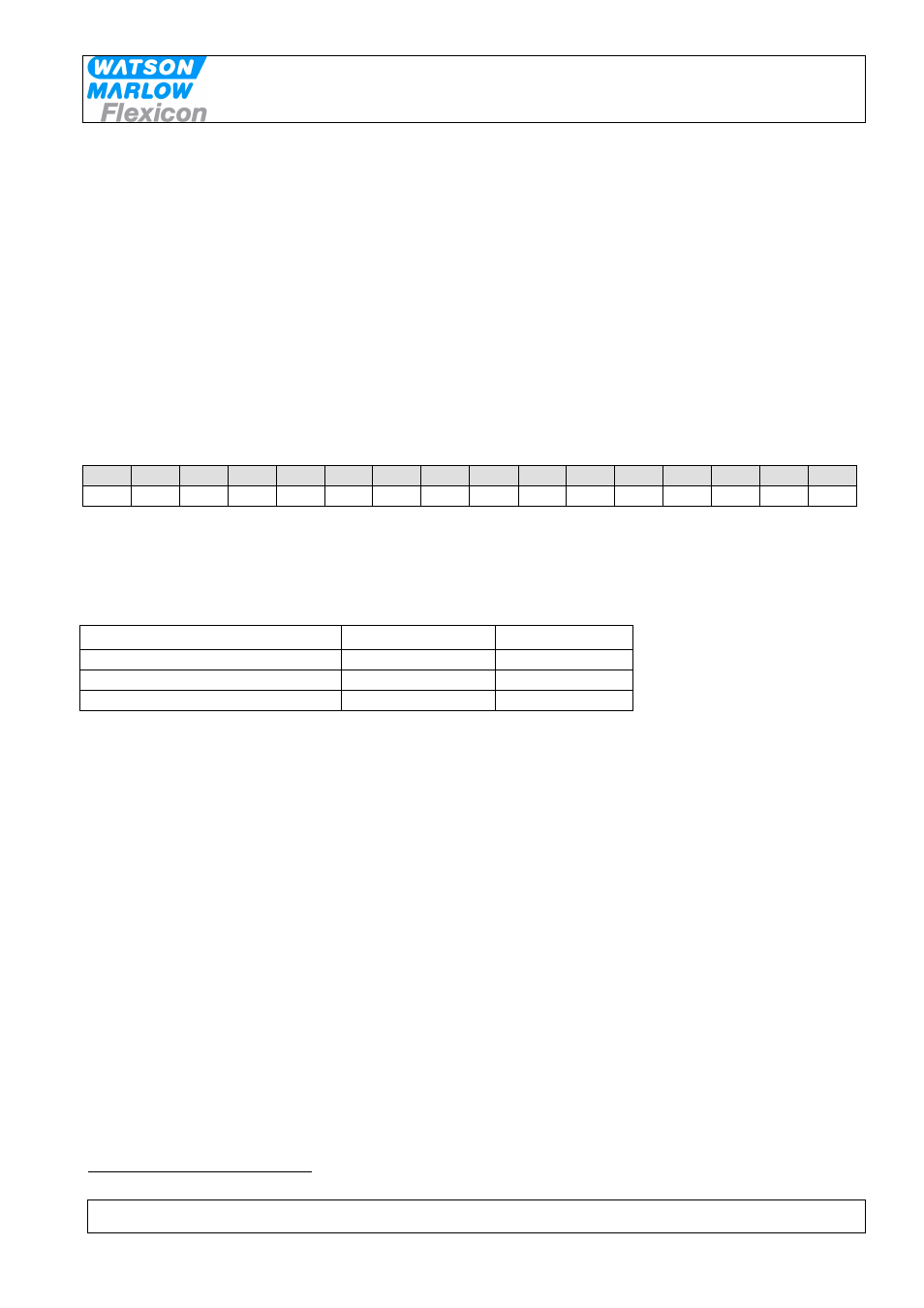
Users Manual
MC100
MC100 DeviceNet OM 1.15 EN
Version: 1.04
Page 18 of 43
7 Operating the MC100
7.1 Process Data Exchange (Cyclic data)
The cyclic data consists of control bits and status bits.
There is a distinction between MC100 control/status bits and pumps control/status bits.
When connected to the Fieldbus network the MC100 will always transmit and receive 1 word for the
MC100 function and minimum 1 word for the pumps (even if only 1 pump is connected there will still
be allocated 1 word, where the highest 8 bits will be empty).
7.1.1 Process control bits for MC100
There is allocated one word (2 bytes) for MC100 control bits as shown below.
Word 0
15
14
13
12
11
10
9
8
7
6
5
4
3
2
1
0
B1.7 B1.6 B1.5 B1.4 B1.3 B1.2 B1.1 B1.0 B0.7 B0.6 B0.5 B0.4 B0.3 B0.2 B0.1 B0.0
B0.0-4:
Sets the active pump number
B0.4-7
Reserved for future use
B1.0:
Mode bit 0
B1.1:
Mode bit 1
MC100 working modes:
1
Mode bit 0
Mode bit 1
Individuel
“1”
“0”
Parallel
“0”
“1”
Seriel
“1”
“1”
B1.2-4
Reserved for future use
B1.5
Alarm reset: will reset lowest number alarm or warning
B1.6
Rescan for pumps: resulting in new values for connected pumps (See ADI 12)
B1.7
Total reset of MC100 including loading the default values to connected pumps.
7.1.2 Modes:
Individual mode
When selected the attached pumps are operated individually. I.e.
volumes; dispense signals; calibration values etc. has to be sent to
each pump.
Parallel mode
Parallel mode requires that all pumps not disabled are of the same
type, i.e. PD12 or PD22 or GD30.
In parallel mode the virtual pump 0 is used to hold common
parameters for all the enabled pumps.
In parallel mode the common data are:
• Volume
• Pump speed
• Acceleration
• Tube size
• Density
1
See Appendix 1 for description of the working modes