Sloan MCR 4004-A CONTROLLER User Manual
Page 4
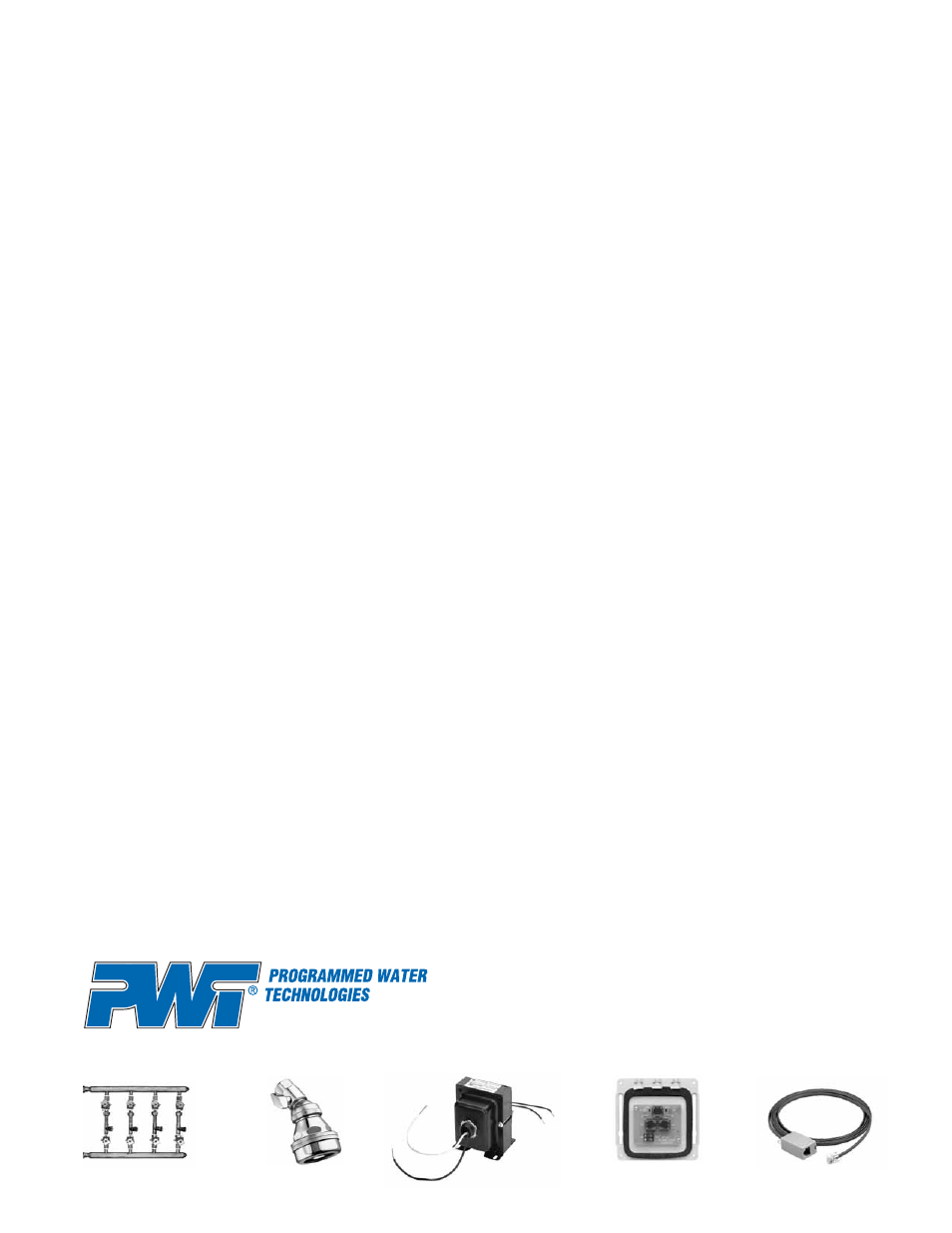
10500 Seymour Avenue • Franklin Park, Illinois 60131-1259
Phone 800-671-6970 • Fax 847-671-6944
A SLOAN VALVE COMPANY
Copyright ©2008 Programmed Water Technologies, A Sloan Valve Company
Printed in U.S.A.
0816638 0508
1. PROBLEM: No water is delivered to any fixture when the push buttons
are pressed.
INDICATOR: No LED lights are illuminated.
CAUSE: No electricity is being supplied to the controller.
SOLUTION: Ensure that the main power is turned on. Check breaker and
transformers. Make sure transformer is supplying 24 VAC (Volts AC).
If no voltage is detected, replace transformer.
INDICATOR: Red LED lights are flashing.
CAUSE: Controller is in “LOCK-OUT” mode.
SOLUTION: Press reset button on face plate or disconnect power to controller for
10-seconds. LED light will stop flashing.
INDICATOR: LED light on input does not illuminate when button
is activated.
CAUSE: Push button is defective, RJ-11 jack is not in correctly, or reed
switch magnets are fouled (MCR 60-A button).
SOLUTION: Unplug RJ-11 Jack then reinstall. Activate push button and check for
LED to illuminate.
If this does not fix the problem, move a working input line to the
problem terminal then activate button. If the LED light illuminates,
you know the original push button is damaged or defective. Replace
with new button. If the button is an MCR 60-A, replace the magnets
inside the push button assembly (MCR 22-A) or the reed switch
(MCR 18-A).
2. PROBLEM: MCR-250-A unit false triggers (activates by itself).
INDICATOR: Input LED light stays on or shows a constant dim light.
SOLUTION: The reed switch is to close to the push rod. Turn off the water supply
to the valve. Remove reed switch from valve body. Remove B-39
Seal. Push reed switch sensor back into the retaining spring away
from the push rod. Reassemble. Check LED light on input. If LED is
still illuminated, repeat action until LED light only illuminates when
button is activated.
3. PROBLEM: Input LED illuminates when button is pressed but valve does
not activate.
CAUSE: Control board output jack is not properly connected or is defective.
SOLUTION: Disconnect RJ-11 plug from the jack and then reconnect. If this does
not fix the problem, plug a working valves’ output RJ-11 plug into
problem output jack. Cycle the valve using alternate push button.
INDICATOR: NO LED light at output jack. Damaged or defective output
jack on the board. Replace board.
CAUSE: Wiring pigtail to valve damaged or defective.
SOLUTION: Replace pigtail or for 603-ESM valve, replace MCR 1001-A solenoid
operator.
PWT TROUBLESHOOTING GUIDE — NON-COMMUNICATING SYSTEM
4. PROBLEM: Flush valve does not function after output LED illuminates.
INDICATOR: Valve makes a "CLICKING" sound but does not flush.
CAUSE: No water is being supplied to valve.
SOLUTION: Make sure the water supply is turned on at the control stop.
Check to see if any ball or gate valves have been turned off up
stream of the control stop.
CAUSE: The EL-163-A Solenoid shaft assembly is fouled or jammed.
SOLUTION: Turn the power off to the valve (Failure to do so could result in
damage to the solenoid coil). Remove the EL-166 nut from the
solenoid operator. Use a spanner wrench or pliers to remove the
EL-163-A solenoid shaft assembly from the valve. Clean and/or
replace as necessary. Be sure to replace the plunger spring when
reassembling solenoid shaft assembly.
CAUSE: The EL-128-A actuator assembly is clogged or needs to be replaced.
SOLUTION: Shut off water to the valve. Remove the solenoid assembly. Take out
and replace/or clean the EL-128-A cartridge assembly. Make sure the
PISTON RING is on the PLUNGER PISTON.
5. PROBLEM: Little or no water is delivered to bubbler or shower head after
output LED has activated.
CAUSE: Water supply stops are closed or partially open.
SOLUTION: Open stops.
CAUSE: Debris is clogging solenoid filter.
SOLUTION: Shut off water supply. Remove, clean, and reinstall solenoid filter.
CAUSE: Solenoid is worn or faulty.
SOLUTION: Turn off water supply. For MCR 139-A, Rebuild with ETF-1009-A
solenoid repair kit, or replace MCR 139-A. For MCR 194-A, Rebuild
with or replace MCR 194-A.
CAUSE: Flow restrictor in bubbler or shower head is clogged with debris.
SOLUTION: BUBBLER- Remove compression nut from 3/8 O.D. Nylon tubing
connecting to bubbler. Remove and Clean flow restrictor.
SHOWER - Remove shower. Remove and Clean flow restrictor.
6. PROBLEM: Bubbler or shower does not stop delivering water or
continues to drip after programmed run time has lapsed.
INDICATOR: Output LED does not turn off after programmed run time.
CAUSE: Short or moisture at output connection.
SOLUTION: Push the reset button on the face plate. If output LED light turns off
reactivate the valve. If LED remains on remove RJ-11 connection.
Clean output jack and plug with electrical contact cleaner. Reinstall.
CAUSE: Debris is clogging solenoid.
SOLUTION: Turn off water supply. For MCR 139-A, Rebuild with ETF-1009-A
solenoid repair kit, or replace MCR 139-A. For MCR 194-A, Rebuild
with or replace MCR 194-A.
7. PROBLEM: Flush valve runs non-stop (run on) or has a slow leak.
CAUSE: Diaphragm by pass hole is clogged and/or filter ring needs to
be cleaned.
SOLUTION: Shut off water at control stop. Remove top cap and inside cover.
Remove and clean diaphragm assembly. Re-install. In reverse order.
CAUSE: Valve body seat is nicked or defective.
SOLUTION: Replace valve body.
8. PROBLEM: Toilet flushes without activation.
INDICATOR: Button is not pressed and solenoid does not fire.
CAUSE: Crack in the inside cap cover (A-71).
SOLUTION: Shut off water to the valve. Remove top cap and inside cover.
Replace inside cover (A-71). Reassemble.