Ntellisys, Daptive, Ressure – Nor-Cal IQ+ Adaptive Pressure Controller User Manual
Page 21: Ontrollers, 2 - devicenet communications
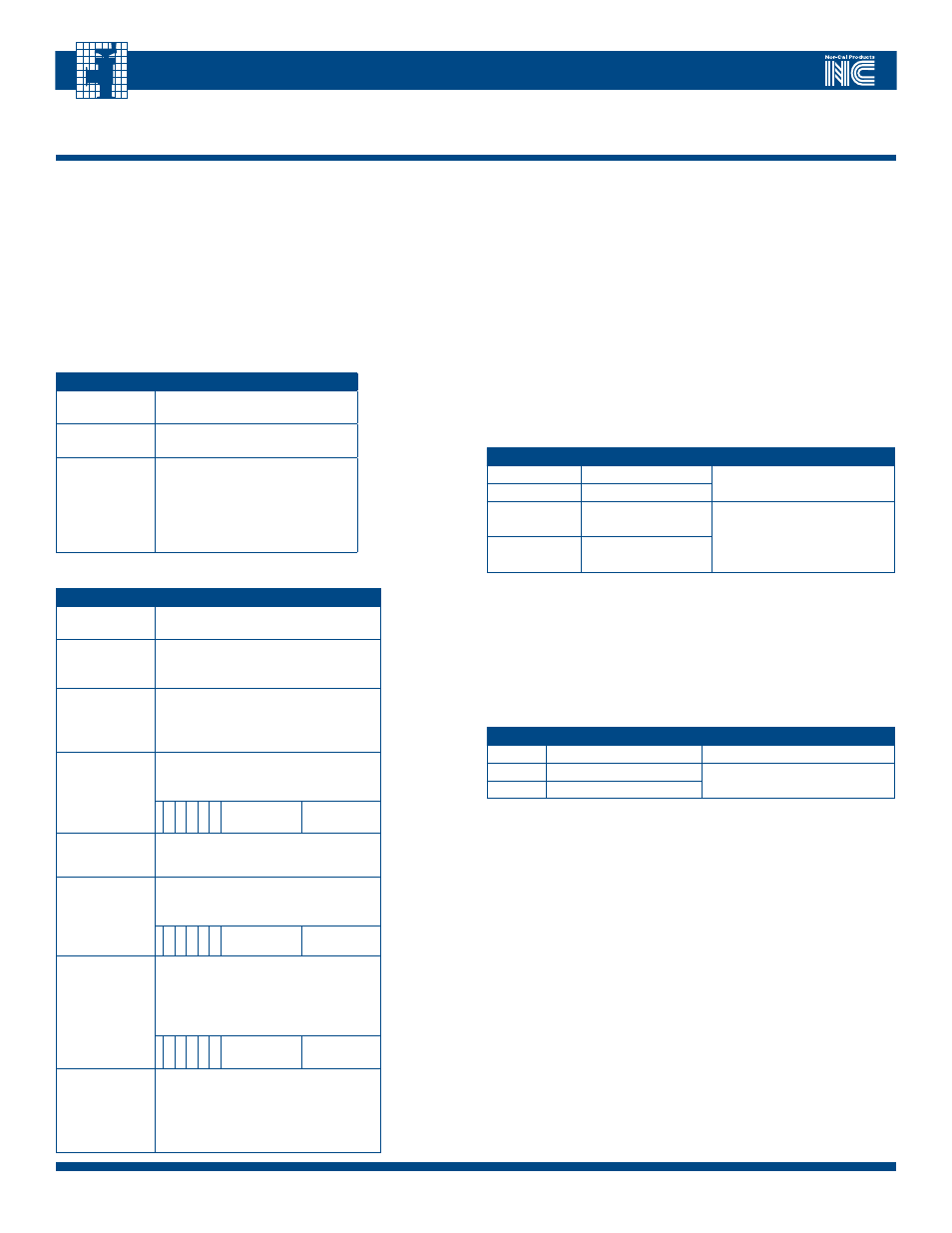
1
Call toll free
800-84-4166
or 530-842-4457
•
FAX 530-842-9130
I
ntellIsys
A
dAptIve
p
ressure
C
ontrollers
IQ+ OP-LIT 9/08
TAbLE 7.5
INPUT ASSEmbLy FORmATS
InStance
hex
varIaBleS
2
(default)
Exception status
Process variable
4
Exception status
Process variable
Control setpoint
5
Exception status
Process variable
Control setpoint
Valve position
0B
Exception status
Process variable
Valve
Discrete
Input 2
Discrete
Input 1
12
Exception status
FP-Process variable
1A
Exception status
FP - Process variable
FP - Valve
Discrete
Input 2
Discrete
Input 1
96
Exception status
Process variable input 1 (low range)
Process variable input 2 (high range)
Valve
Active process input instance
Discrete
Input 2
Discrete
Input 1
97
(Master / Slave)
Control mode
Pressure setpoint
Position setpoint
Control instance
Individual valve control (address)
Individual valve control (action)
TAbLE 7.4
OUTPUT ASSEmbLy FORmATS
InStance
hex
varIaBleS
7
(default)
Control setpoint
Control instance
17
FP-Control setpoint
Control instance
97
(Master / Slave)
Control mode
Pressure setpoint
Position setpoint
Control instance
Individual valve control (address)
Individual valve control (action)
How to read system pressure and valve position:
•
Select the service code
0E
(get attribute)
•
Select class ID
31
(select the s-analog sensor object)
•
Select instance ID
1
(process input low range)
•
Select attribute ID
6
(value attribute)
•
The device will respond with data bytes 00 00
meaning that the measured pressure is 0
•
Select instance ID
3
(valve position)
•
Select attribute ID
6
(value attribute). The device will respond
with data bytes
FF 7F
meaning that the valve position is fully open.
Input/Output messaging:
I/O messaging is used to read and write data to the device on a periodic basis.
They are used for transmission of a continuous stream of data such as setpoint
or process pressure. I/O messages have limited overhead and rely on a
prearranged set of data called assemblies. The IQ+ controller handles input
assemblies and output assemblies in a poll connection. In an I/O poll
connection the tool DeviceNet controller periodically sends an output
assembly and the IQ+ responds with an input assembly. The IQ+ supports 3
output and 8 input assembly formats. For polled I/O connections, the device
will automatically transition to the device Executing state after the first valid
I/O data has been received.
Example of I/O messaging transactions:
The following is an example format of a typical poll connection, using
default settings.
After having opened the I/O connection the master sends the following data:
Byte
deScrIPtIon
data ranGe
1
Setpoint (low byte)
0 to 7FFFh
2
Setpoint (high byte)
3
Setpoint destination
(low byte)
00 for no operation
01 for pressure control
02 for position control
4
Setpoint destination
(high byte)
Note:
The setpoint is a number from 0000 hex to 7FFF hex covering the
range 0 to 100%. In other words, in pressure control mode, 7FFF hex
represent full scale of the selected pressure source. If the pressure gauge
used is 1 Torr then a set point of 4000 hex will control pressure to 0.5 Torr.
In valve position control mode, 7FFF hex represents full open stroke.
Respectively, 0000 hex setpoint corresponds to closing the valve and 7FFF hex
corresponds to fully opening the valve.
The controller response is formatted accordingly:
Byte
deScrIPtIon
data ranGe
1
exception status
See table 8.8.2 on page 12
2
pressure (low byte)
0 to 6000h
3
pressure (high byte)
Note:
Data types and data units may be changed in application objects
handling pressure and position related attributes. Data type can only be
changed if no I/O connection has been established using a related attribute
and the device is in idle state. Data units can only be changed when the device
is in idle state. Changes to these attributes in application objects are
non-volatile (recorded in NVRAM).
7.2 - DeviceNet Communications
(continued)