Dillon Precision Super 1050 User Manual
Page 18
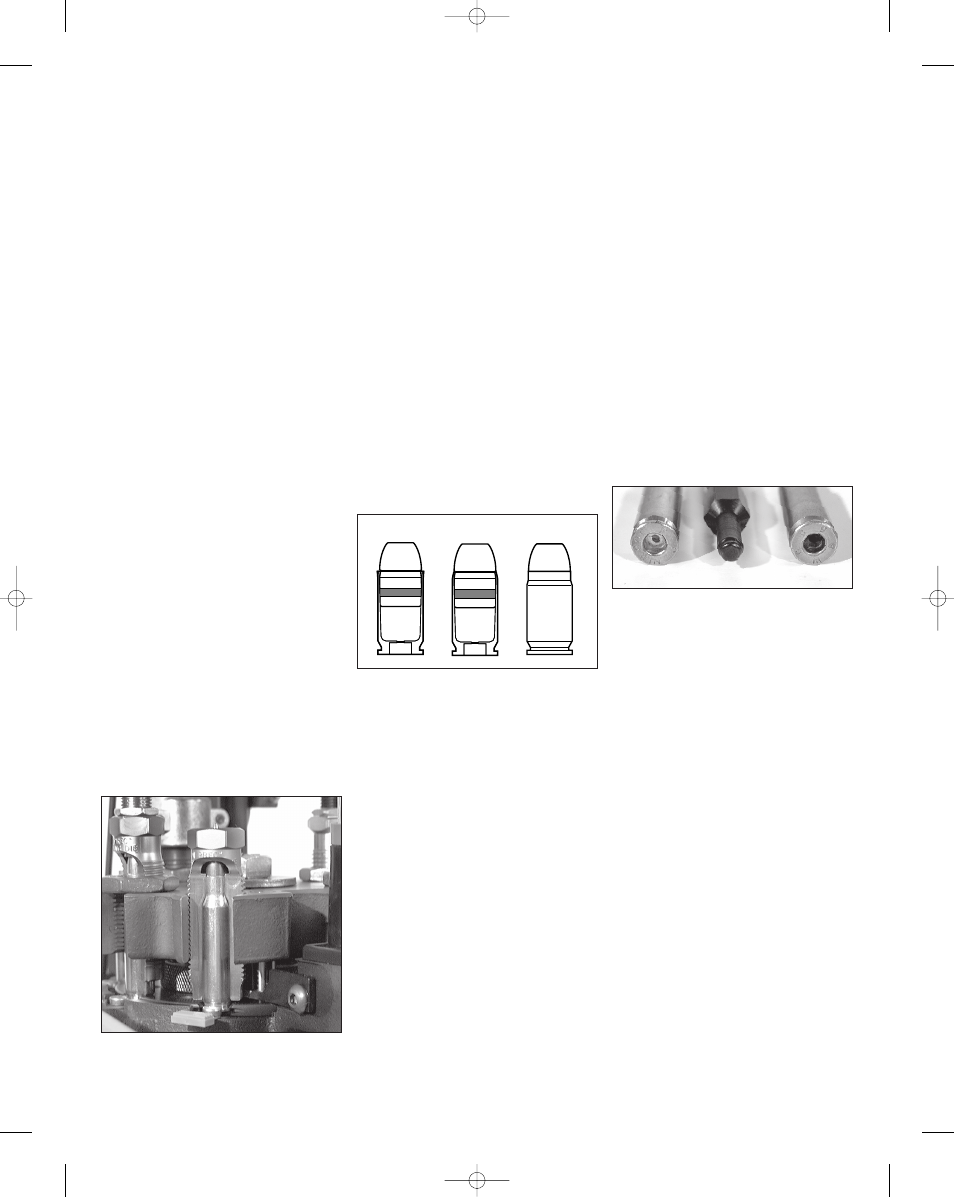
ing the bullet, but it will give you a
place to start.
Place a case (with a belled case
mouth) into Station 7. Fig. 57
Place a bullet on the belled case
mouth and lower the toolhead. Then,
raise the toolhead just enough to inspect
the bullet without indexing the
shellplate. If the bullet is not seated deep
enough, screw the seating die down 1/2
turn at a time. As a guide, one full turn
moves the die down about 70 thou-
sandths of an inch, about the thickness
of a nickel. Again, cycle the machine
and inspect the seating depth. Repeat
these steps as necessary until the correct
overall length is achieved. Use a dial
caliper or equivalent to measure the
overall length of the cartridge. Check the
overall length of the round against the
information in your reloading manual.
Once you have obtained the proper
OAL, replace the cartridge into Station 7
and lower the toolhead. Using a 1"
wrench to turn the lock ring and a 7/8"
wrench to hold the die body, snug the
lock ring.
Note: If you ever load a cartridge that
you are unhappy with, you can use a
Dillon bullet puller to reclaim your com-
ponents.
Station 8 - Installation and adjustment
of the Crimp Die
Screw the crimp die into Station 8.
Screw it down until it is flush with the
bottom of the toolhead. This is a good
starting point for the crimp adjustment.
Place a cartridge with a properly seat-
ed bullet into Station 8.
Lower the toolhead and continue to
screw the die down until it touches the
cartridge.
Fig. 58
Raise the toolhead and screw the die
down 1/8 of a turn, lower the toolhead.
Raise the toolhead halfway and
inspect the cartridge. If the bell is still
present, or the desired amount of crimp
has not been achieved, give the die a
1/8 turn down and try again. Continue
making small adjustments to your crimp
die until the desired amount of crimp
has been achieved.
Once the adjustment is complete,
place the case back into Station 8 and
lower the toolhead. Using a 1" wrench
to turn the lock ring and a 7/8"
wrench to hold the die body, snug the
lock ring.
Note: When adjusting the crimp die it
is important to know what to look for.
Check that the crimp: Looks OK, allows
your firearm to function consistently and
the bullet feels tight in the case.
The drawing of case #3 (above) is a
depiction of a case that has been over
crimped by adjusting the crimp die
down (clockwise) too far. Note the
defined line below the mouth of the case
and the bulge below the line. This is not
a proper crimp. This line is the direct
result of the cartridge being over
crimped. A line like this will only
appear if the crimp die is adjusted
down too far. Warning: Over crimping
.45ACP, .38 Super, 9mm, etc., can
actually cause the bullet to be loose
in the case.
Adjustments for calibers 9mm, .38 Sp.,
.45 ACP and for hot loads that have
been fired many times
Configuration 1
To begin, place a military case (sized,
decapped and unswaged) into Station 3.
Screw the back-up rod (#12749*)
down two turns into the toolhead
(#20420). Pull the handle.
Using a wrench turn the back-up rod
(#12749*) down until it hits the inside
bottom of the case. Note: Do not force
the expander as this will damage the
case and the shellplate. Now secure the
lock ring (#14062). Raise the handle.
Screw the eyebolt (#13245) all the
way into the swager. Grease the clevis
pin (#13522) heavily.
Put the swager into position. Push the
clevis pin through the connecting rod
and eyebolt and secure with the hitch
pin (#13840). Replace the swage cover
(#13064).
With the military case still in
Station 3, pull the operating handle
down with your left hand. Now turn
the swager upward with your right
hand until it meets resistance. With
your left hand raise the operating han-
dle about 10 inches. With your right
hand turn the swager up a 1/4 turn.
Cycle the handle down.
Raise the handle just enough to
remove the case and inspect the primer
pocket to see the amount of swaging
being done. The swager should leave a
radiused entrance on the primer pock-
et. Fig. 59
Turn the swager in, using 1/4 turn
increments until you achieve the prop-
er swage. Secure the jam nut (#13682).
Note: Do not over swage. This condi-
tion will cause damage to the
shellplate (#12600*).
When your swager is properly adjust-
ed you will feel resistance during the
final 1/2" to 1" of the downward stroke
of the handle.
Adjustments for rifle calibers
Configuration 2
To begin, place a military case (sized,
decapped and unswaged) into Station 3.
Remove the back-up rod (#12749*)
from the back-up die (#12184).
With the operating handle in the
down position, screw the back-up die
into Station 3 until the die comes into
contact with the shellplate. Now back
18
Fig. 58 - Cutaway crimp die shows the
area being crimped while the case is
being fully supported by the die body.
Fig. 59 - Note the difference between the
swaged primer pocket (left) and the
unswaged primer pocket (right).
Figure 64
Figure 70
Figure 114
3
2
1
Super 1050, May 2007 5/21/07 12:00 PM Page 18