Measuring manifold pressure, C. adjusting gas input (propane gas furnace), D. adjusting burner air shutters – Bryant 585B User Manual
Page 9: E. blower fan relay (heating)
Attention! The text in this document has been recognized automatically. To view the original document, you can use the "Original mode".
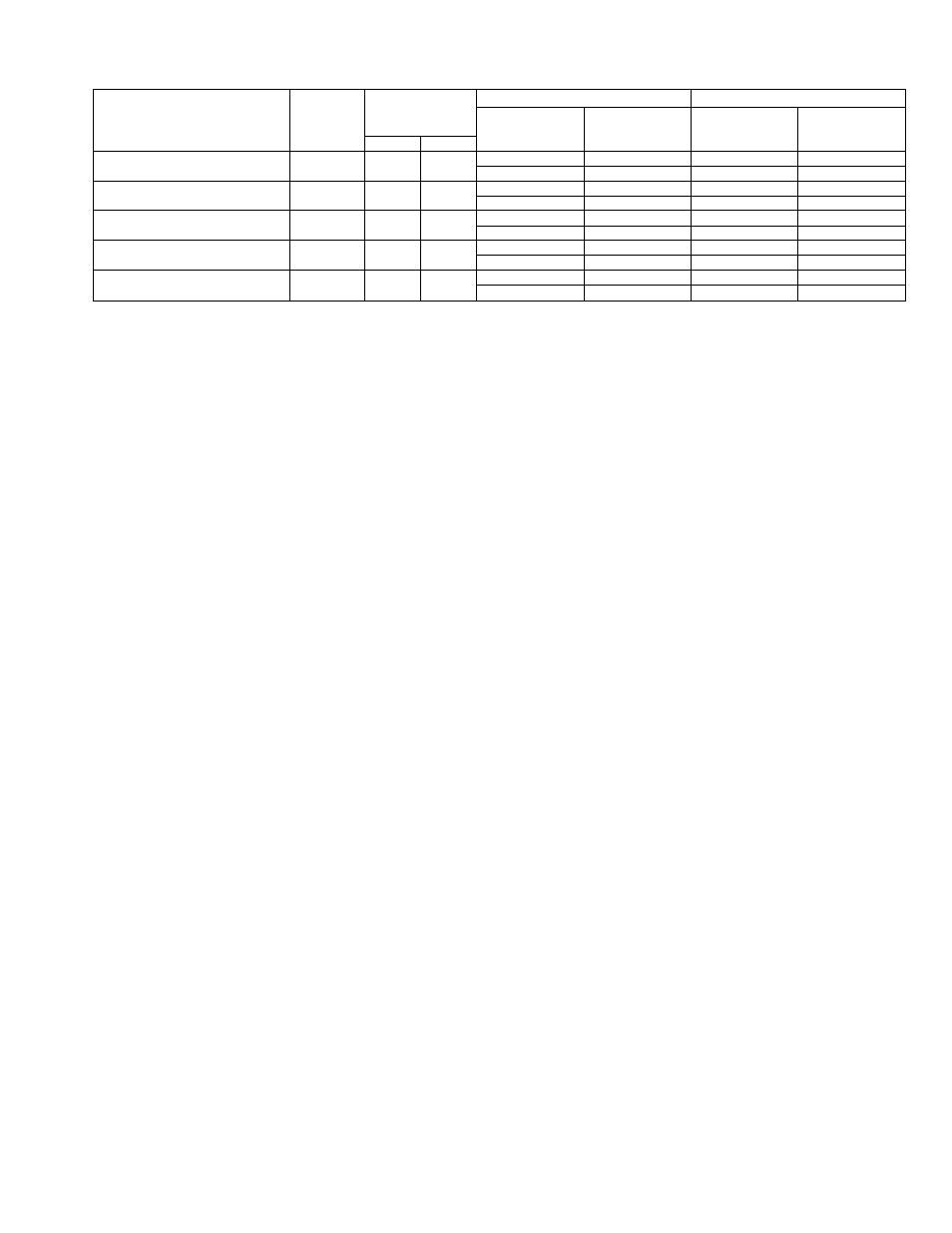
TABLE V-RATED GAS INPUTS (Btuh) FOR VARIOUS MAIN
BURNER ORIFICES AT INDICATED MANIFOLD PRESSURES*
585B
Size
Number
of
Orifices
Manifold
Pressure
(in. wc)
Natural Gas
Propane Gas
Orifice
P/N
Heating
Input
(Btuh)t
Orifice
P/N**
Heating
Input
(Btuh)t
Nat
Prop.
018050
& 024050
2
3.5
10.5
55365-451
40,000
55365-55
40,000
55365-42
50,000
55365-53
50,000
024075, 030075,
& 036075
3
3.5
10.5
55365-45Ф
60,000
55365-55
60,000
55365-42
75,000
55365-53
75,000
042100
4
3.5
10.5
55365-441
80,000
55365-55
80,000
55365-41
100,000
55365-53
100,000
036125,048125,
& 060125
5
3.5
10.5
55365-441
90,000
55365-55
90,000
55365-41
125,000
55365-53
125,000
060150
6
3.5
10.5
55365-441
120,000
55365-55
120,000
55365-41
150,000
55365-53
150,000
*Data in this tabie is based on aititudes from sea ievei up to 7000 feet above sea ievel at the minimum rated input, or 2000 feet above sea
levei at the maximum rated input. For higher altitudes, follow the recommendations of national and local codes,
t Gas inputs for natural gas are based on a heating value of 1050 Btu/Ft® with a specific gravity of 0.65 at the factory-set manifold pres
sure of 3.5 inches wc. Gas inputs for propane gas is based on a heating value of 2500 Btu/Ft® with a specific gravity of 1.5 at a manifold
pressure of 10.5 inches wc.
fThese natural gas burner orifices are the factory-supplied orifices. All other natural gas orifices shown are optional field-supplied
orifices.
**Propane burner orifice P/N’s shown are furnished in conversion kit P/N 301625-703.
a. Determine number of seconds for gas meter test dial
to make one revolution.
b. Divide 3600 by number of seconds in step a.
c. Multiply result of step b by the nuinber of cubic feet
shown for one revolution of test dial. This gives
cubic feet of gas flow per hour.
d. Multiply result from step c by Btu heating value of
gas. Consult local utility for heating value of gas.
This is the total measured input in Btuh. Compare this value
with input shown in Table V.
Example:
Suppose the size of test dial is 1 cubic foot; it
takes 30 seconds to complete one revolution; heating value
of gas 1050 Btu/ft^. Proceed as follows:
a. 30 seconds to complete one revolution.
b. 3600 divided by 30 equals 120.
c. 120 times 1 equals 120 cubic feet of gas flow per
hour.
d. 120 times 1050 equals 126,000-Btuh input.
If the desired input was 125,000 Btuh, only minor changes
would have to be made at the pressure regulator adjustment
screw on the gas valve to bring the unit to the desired input.
If the measured input does not agree with the value desired,
the manifold pressure may be adjusted with the REG ADJ
screw on the gas valve as follows:
To increase input: Turn screw clockwise.
To decrease input: Turn screw counterclockwise.
2. Measuring Manifold Pressure
A water manometer is required to measure the manifold
pressure. If a spring manometer is used, make sure the
manometer is calibrated.
When the heating value of the natural gas being used for a
particular installation is significantly more or less than
1050 Btu/ft®, or slight manifold pressure changes are neces
sary for other reasons, the manifold pressure may be
adjusted at the REG ADJ screw on the gas valve.
CAUTION:
Do not adj ust the manifold pressure more than
0.3 inches wc above or below the 3.5 inches wc factory set
ting. If larger adjustments are required, change the burner
orifices following the recommendations of national and local
Proceed as follows to measure manifold pressure and to
adjust gas input:
a. Turn off gas to unit.
b. Remove pipe plug on gas valve outlet identified as
PRESS TAP, and connect manometer at this point.
c. Turn on gas to unit and start heating section.
d. With all burners fired, adjust manifold pressure
with REG ADJ screw on gas valve to obtain desired
gas input.
NOTE:
To increase input, increase manifold pressure by
turning screw clockwise. To decrease input, decrease
manifold pressure by turning screw counterclockwise.
e. Turn off gas to unit. Remove manometer from gas
valve and replace pipe plug.
C. Adjusting Gas Input (Propane Gas Furnace)
The field-installed propane conversion kit contains a pro
pane gas regulator spring that replaces the natural gas reg
ulator spring in the unit combination gas valve/pressure
regulator. The converted pressure regulator is then adjusted
to provide the desired gas input. Follow the procedures in
the conversion kit Installation Instructions to adjust the
propane gas input.
D. Adjusting Burner Air Shutters
To adjust the primary air to each burner, partially close the
air shutter until there is a slight yellow tip on the top of the
flame, then open the air shutter until the yellow tip just dis
appears. This should be done after the burners have been
operating at full input for 5 or 10 minutes (approximately).
Secure shutters with locking screws after adjusting primary
air to each burner.
E. Blower Fan Relay (Heating)
The heating relay (See Figure 7) is located in the control box
and is adjustable to permit lengthening or shortening the
“off” cycle. The “on” cycle is automatically adjusted as the
“ofiT’ cycle is changed.
The fan control adjusting lever is factory-set at the center
position and should give optimum performance in most in
stallations. However, on unusual installations, or where the
line voltage is considerably above or below the rated output,
it may be necessary to increase or decrease the length of
time the blower remains on. For longer blower operation,
move the adjusting lever toward the right-hand position. In
this position, the control makes contact sooner and takes the
maximum time to break contact. For shorter blower opera
tion, move the lever to the left-hand position.
-9-