B. low-voltage connections, C. heat anticipator setting, Vi. preparing unit for startup – Bryant 585B User Manual
Page 8: Vii. heating startup and adjustments, A. gas input, B. adjusting gas input (natural gas furnace), Measuring gas flow at meter
Attention! The text in this document has been recognized automatically. To view the original document, you can use the "Original mode".
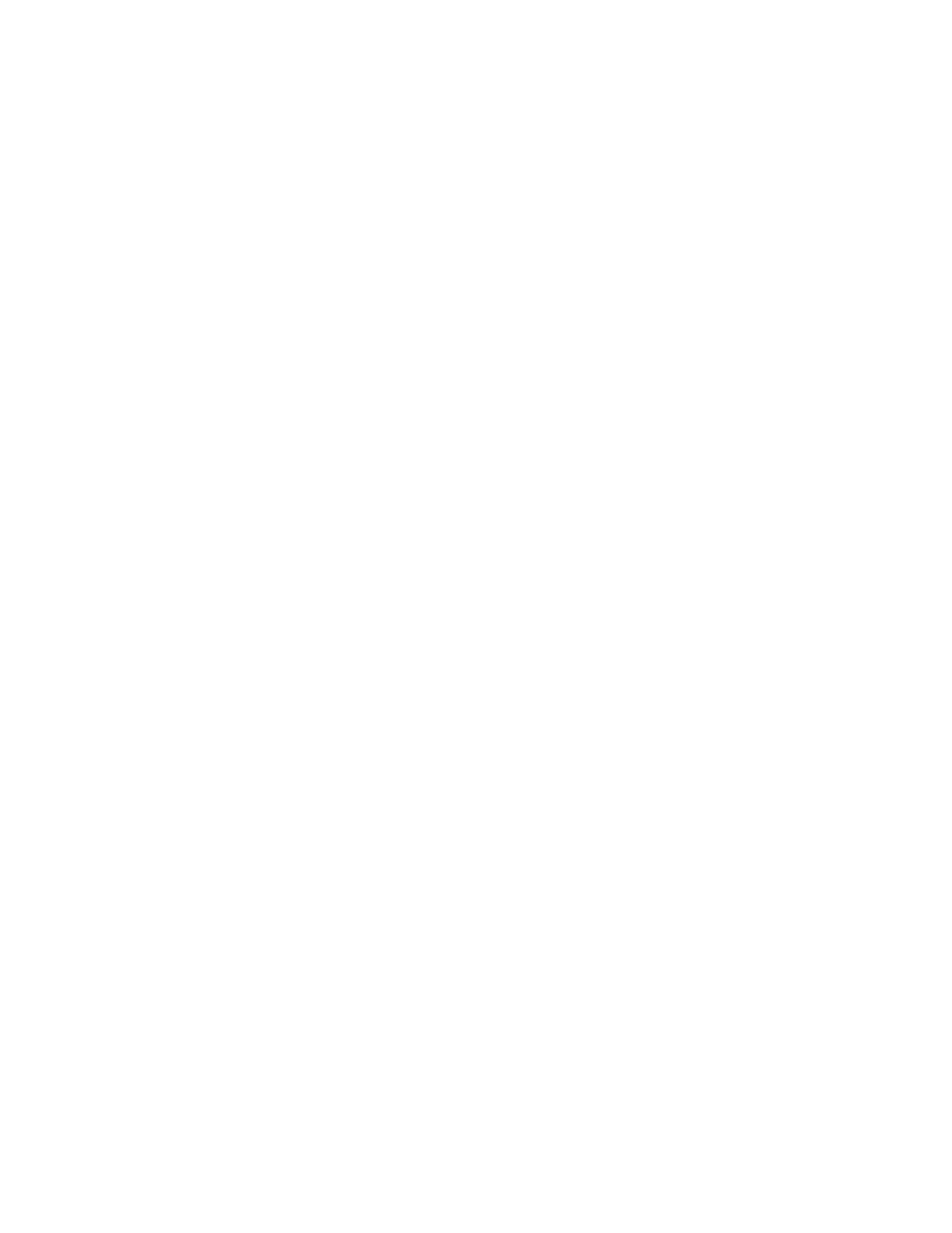
NOTE:
On 3-phase units, the third power lead is connected
to the brown high-voltage pigtail lead. See unit wiring label
and Figure 11.
B. Special Procedures for 208-V Operation
WARNING:
Make sure the power supply to the unit is
switched OFF before making any wiring changes.
When size 018050 thru 036125 dual-voltage units are to be
operated at 208 volts, unplug the orange lead running to the
primary side of the unit transformer and plug it onto the
208-V red transformer tap. See the unit wiring label.
When sizes 018050 or 024050 are to be operated at 208 volts,
additional wiring changes must be made in the unit control
box as follows:
1. Unplug orange motor lead connected to evaporator mo
tor run capacitor (4A1). See unit wiring label. Tape end
of orange lead.
2. Plug unused yellow motor lead onto vacated run capaci
tor terminal. Figure 12 shows corrected wiring.
B. Low-Voltage Connections
CAUTION:
When room thermostat leads are run in the
same conduit with high-voltage leads, they must be insu
lated for the highest voltage contained within the conduit.
A room thermostat with isolated contacts must be used to
prevent interconnection of class 2 outputs. (The following
recommended thermostats meet this criteria.)
Recommended room thermostats are P/N 34427D03O (sub
base included) or P/N PS2758-1 (or -2) with subbase P/N
PS2759-34 for manual system changeover. For automatic
system changeover, use thermostat P/N 34427D52 or P/N
PS3108A with subbase P/N PS3109E.
Mount the room thermostat on an inside wall of the space to
be conditioned. The thermostat should be positioned approx
imately 4 or 5 feet above the floor, and located where it will
not be subjected directly to either a cooling or heating
source, or direct exposure to sunlight.
If low-voltage leads from the thermostat are run separately,
enter the unit through grommeted hole provided in the con
trol corner panel. See Figure 2 for hole location.
Connect the low-voltage thermostat leads to the flagged pig
tail leads that run through a hole in the bottom of the unit
control box. See Figures 7 and 11.
NOTE:
Connect thermostat to unit using No. 18 AWG “col
or-coded” insulated wires. If thermostat is located more than
100 feet from unit as measured along the low-voltage wires,
use No. 16 AWG wire.
C. Heat Anticipator Setting
The room thermostat heat anticipator must be properly
adjusted to insure proper heating performance. Set the heat
anticipator to 0.85 amps.
Failure to make a proper heat anticipator adjustment will
result in improper operation, discomfort to the occupants of
the conditioned space, and inefficient energy utilization;
however, the required setting can be changed slightly to pro
vide a greater degree of comfort for a particular installation.
VI.
PREPARING UNIT FOR STARTUP
Proceed as follows to prepare the unit for startup:
1. Remove all service access panels and check for shipping
damages, such as broken lines, loose parts, disconnected
wires, etc.
2. Read and follow instructions on all WARNING, CAU
TION, AND INFORMATION labels and tags attached
to unit; such as motor rotation labels, blower rotation
labels, and vent instruction tag.
3. Make certain gas supply has been purged and all gas
piping checked.
WARNING:
Do not purge into the combustion chamber. Do
not use a match or other open flame to check for leakage.
4. Check to be sure all wiring connections, including facto
ry connections, have been completed and are tight.
5. Inspect all supply ducts and grilles to be sure they are
adjusted properly.
6. Check to be sure air filters are in place.
VII.
HEATING STARTUP AND ADJUSTMENTS
CAUTION:
Complete the steps in Section VI before starting
unit.
Do not jumper any safety devices when operating unit.
Burner orifice alignment must be insured. Unstable opera
tion may occur when the manifold’s burner orifices are not
aligned correctly. To insure correct burner orifice alignment,
check the orifice angle with a machinist’s or carpenter’s
square, a machinist’s protractor, or other suitable device.
The orifice angle should be from horizontal to 3 degrees
down as measured from the unit base.
Follow the instructions on the unit rating plate for starting
the heating section.
A. Gas Input
The unit rating plate indicates two A.G.A.-certified gas
inputs. The burners are equipped with natural gas orifices
that deliver the minimum rated input. Optional field-in-
stalled burner orifices are required to provide the optional
maximum heating input rating. See Table V.
When the unit is being installed for operation at the
optional maximum heating input rating, proceed as follows
to install the field-supplied maximum heating input burner
orifices:
1. Remove burner shield and burners.
2. Remove factory-supplied burner orifices from manifold
and replace with field-supplied maximum heating input
burner orifices.
3. Replace burners and burner shield.
4. Mark appropriate changes on unit rating plate in boxes
provided.
For propane gas operation, propane conversion kit P/N
301625-703 must be field-installed. This kit contains six
burner orifices for the minimum input rating and six for the
maximum input rating. Six orifices are sufficient for the
largest heating unit. For smaller heating sizes, all orifices
will not be required. See Table V.
CAUTION:
The units are designed to give the correct input
using the fixed orifices and manifold pressures shown in
Table V. Do not redrill the orifices under any circumstances.
NOTE:
The minimum and maximum rated inputs shown in
Table V are for altitudes from sea level up to 7000 feet above
sea level at the minimum input or 2000 feet above sea level
at the maximum input. These inputs are based on a heating
value for natural gas of 1050 Btu/ft® at 0.65 specific gravity
and propane gas with a heating value of 2500 Btu/ft®. For
elevations above 7000 feet at the minimum rated input or
2000 feet at the maximum rated input, reduce the ratings
4% for each 1000 feet above sea level. For other gas heating
values or specific gravities, refer to BDP training and ap
plication materials, national and local codes, or contact your
BDP Distributor or Branch to determine the required orifice
size.
B. Adjusting Gas Input (Natural Gas Furnace)
Natural gas input can be determined and adjusted using one
of the following two recommended methods.
1. Measuring Gas Flow at Meter
All other gas appliances must be turned off when measuring
gas flow at meter to check the input. Proceed as follows:
-8-