Carrier 38HQ User Manual
Page 15
Attention! The text in this document has been recognized automatically. To view the original document, you can use the "Original mode".
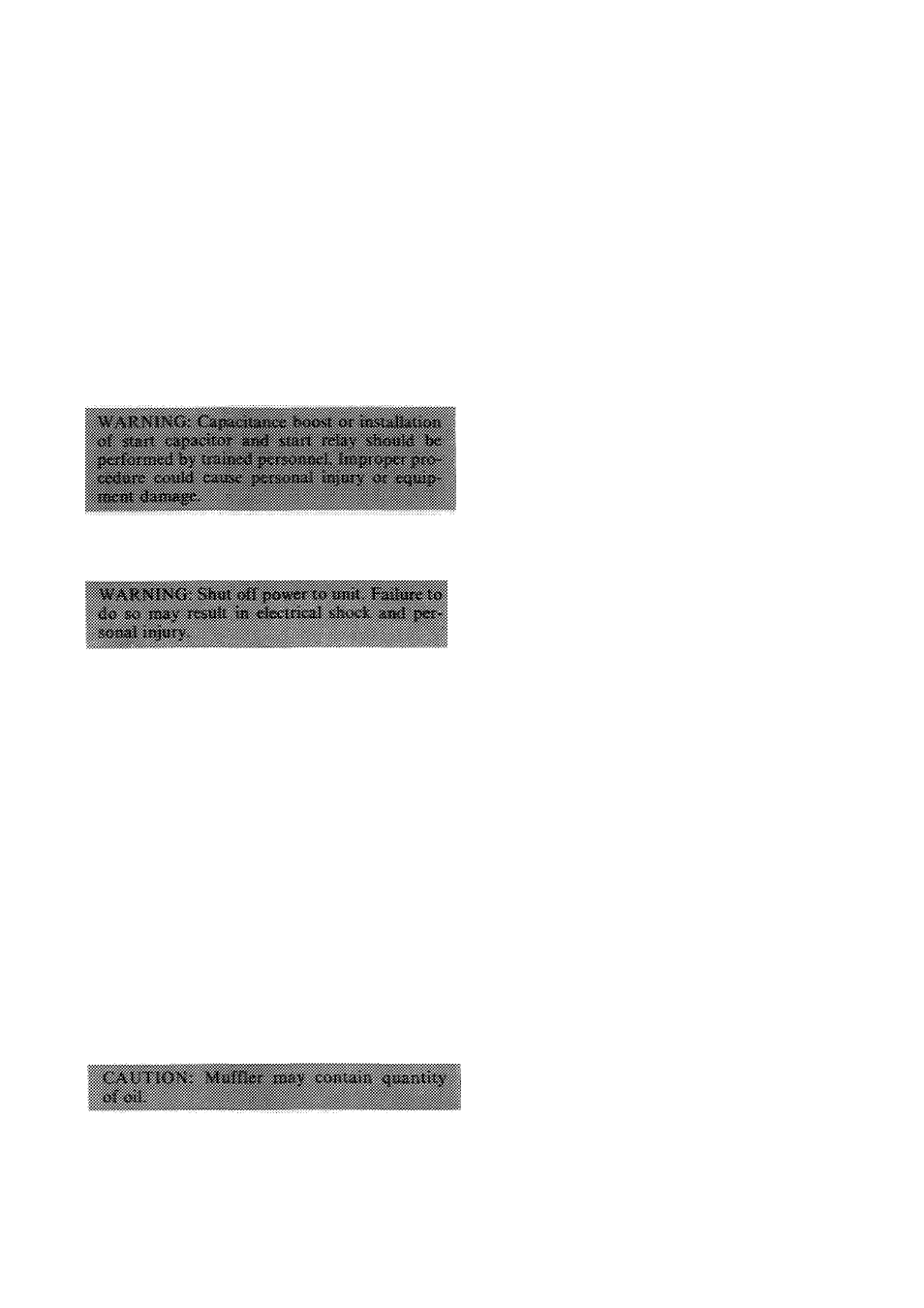
6.
From intersect point, project vertically down
ward to chart suction pressure line. Compare
chart suction pressure to unit suction pressure
(Step 2).
7.
If unit suction pressure is lower than chart
pressure, add refrigerant to system until chart
pressure is reached. If unit suction pressure is
higher than chart pressure, remove refrigerant
until chart pressure is reached.
Unit
Single-Phase
Compressors
that
are
Equipped with a Compressor Start Thermistor
(PTC device) — When supply voltage is within 10%
limit and compressor does not start, check the start
thermistor with an ohmmeter.
If PTC resistance is 0 ohm (open) or higher than
200% of the rating, the device is defective.
Compressor Removal — See Table 8 for com
pressor information and Fig. 24 for component
location.
Remove refrigerant from system using refrigerant
removal
methods
described
in
Carrier
Standard
Service Techniques Manual, Chapter 1.
Follow safety codes, and wear safety glasses and
work gloves. Have quenching cloth available.
1. Remove unit top cover and front access
wrapper.
2. Remove compressor terminal box cover, dis
connect and remove compressor power leads.
3. Using a tubing cutter, cut suction and discharge
lines at convenient place near compressor for
easy reassembly to new compressor with copper
slip couplings.
4. Remove crankcase heater from compressor
base.
5.
Remove compressor hold-down bolts. Lift out
compressor.
6.
Carefully unbraze suction and discharge line
piping stubs from compressor. If oil vapor in
piping stubs ignites, use quenching cloth.
7. Braze piping stubs (removed in step 6) on new
compressor.
8. Clean system. Add new liquid line heat pump
filter-drier as described below.
9.
Install new compressor in unit. Braze suction
and discharge lines to compressor piping stubs
(at points where cut, step 3) using field-
supplied copper couplings. Ensure compressor
hold-down bolts are in place. Connect wiring.
10. Evacuate and recharge system.
FILTER-DRIER — Install accessory heat pump
filter-drier (Table 4) in system liquid line when
refrigerant system is opened for service as described
under Compressor Removal. Position drier in liquid
line at convenient location.
Unit Controls and Safety Devices
HIGH-PRESSURE RELIEF VALVE is located in
compressor. Relief valve opens at a pressure differ
ential of approximately 600 psi between suction
(low side) and discharge (high side) to allow pres
sure equalization.
INTERNAL
CURRENT
AND
TEMPERATURE
SENSITIVE
OVERLOAD
resets
automatically
when internal compressor motor temperature drops
to a safe level (overloads may require up to 45
minutes to reset). When an internal overload is
suspected
of
being
open,
check
by
using
an
ohmmeter or continuity tester. If necessary, refer
to
Carrier Standard Service Techniques Manual,
Chapter 2, for complete instructions.
LOW-PRESSURE
SWITCH
is
located
in
com
pressor section on suction line between reversing
valve and accumulator. Provides loss of charge pro
tection
by
shutting
compressor
off
if
suction
pressure drops below setting. Low-pressure switch
settings are: open, 5 ± 3 psig; close, 20 ± 5 psig.
CRANKCASE HEATER is connected across line
side of contactor and operates continuously.
The purpose of the heater is to keep the crank
case warm during the off cycle and thus prevent
dilution of the oil with refrigerant. This assures good
lubrication and prevents loss of oil from crankcase
during start-up.
If the electrical disconnect switch to the com
pressor section has been off for an extended period
of time, the crankcase heater should be energized for
24 hours before starting the compressor.
SYSTEM
MALFUNCTION
WARNING
INDI
CATOR turns on indoor thermostat light if ther
mostat calls for heating or cooling and compressor
doesn’t
operate
because;
low-pressure
switch
or
internal line break has functioned; control device
or compressor is not operational. The light turns off
when
compressor
restarts,
indoor
thermostat
is
satisfied or if thermostat is manually turned off,
then on.
15