Safety reminders, Preventive maintenance – Carrier 51CM User Manual
Page 2
Attention! The text in this document has been recognized automatically. To view the original document, you can use the "Original mode".
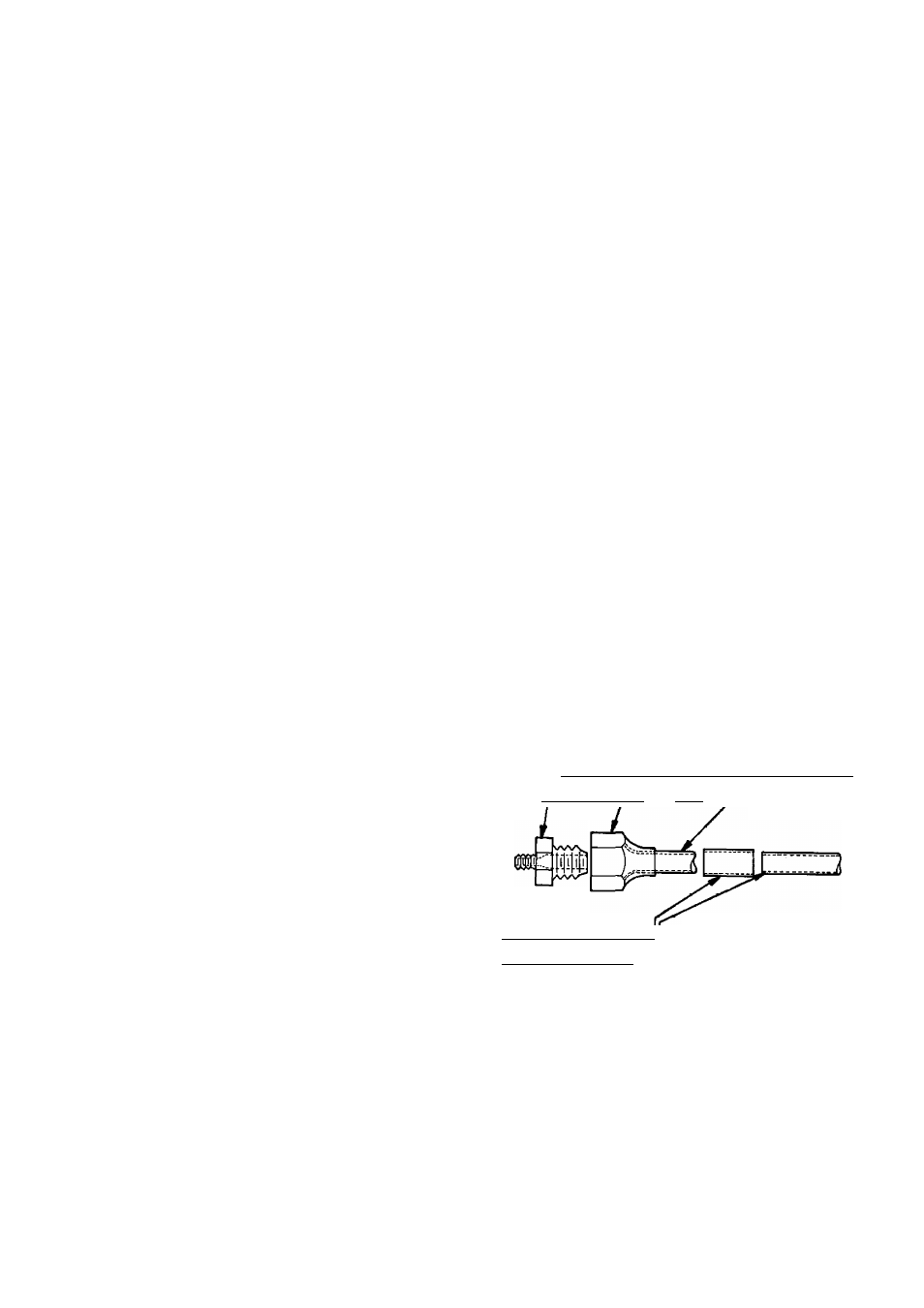
It is much easiei to unsweat a short piece of tubing from
the compressor afte) you have removed the compressoi
irom the unit It follows that you can soldei the oil piping
stub into the new compressor fittings more easily befoie
the eompiessor is put back into the unit
If you choose a good tubing location for cutting the
refrigerant lines initially, the loeation is easily accessible
when making the final joints
SAFETY REMINDERS
1 Cany a file extinguishei in youi tiuck Keep it within
reach when using a torch Check fiie extinguisher
peiiodically to be suie it is fully loaded and iunctional.
2 Know how to handle oxyacetylene equipment safely
Lock the equipment in an upright position in the
truck and at the job site
3 Use dry nitrogen oi carbon dioxide to pressuiize the
system for leak checking Always use a good regulatoi
Be careful not to exceed 150 psig test pressure in the
heimetic eompiessor
4 Weal your safety goggles and gloves when lemoving
refiigeiant from a system
5 Attend your shop safety meetings
Preventive Maintenance
CLEANING — Clean cooling coil and condensei coil
Hold flashlight behind coil to see if all spaces are clear
Use a hooked wire to lemove dirt Dust accumulation
obstructs or reduces airflow and results in loss of capac-
ity Coils may be vacuumed when diy Outdoois, unit can
be brushed with a stiff brush and fins blown out with
compressed aii
Thoroughly clean basepan, motors, fan wheels, other
components and all drain passages Vacuum insulation
Clean all inside painted surfaces with mineral spirits to
remove grease
Clean cabinet and grille Mild detergents reduce elec
trostatic charges on plastic sections of the grille and are
good cleaners Do no! use carbon tetrachloride, solvents
or waxes containing solvents to clean plastic sections
PAINTING — Paint any parts that show evidence of
rust with a good rust-resistant paint
WIRING — Check all wiring for deterioration and all
electrical contacts for tightness and lack of corrosion
LEAKS — Check any connections that show evidence of
oil or leaks When unit is property installed, centered and
leveled (see MOUNTING), check gaskets and wing
panels for possible air leakage
MOUNTING — Make sure unit is secure in window,
level from left to right, and from front to rear according
to installation instructions provided
If used, check compressor mounting springs and re
place if necessary Spt ings tend to lose their tension with
use This could lead to noisy operation
Check fans to ensure they are correctly positioned,
centered in orifice and tight on shaft
CONTROLS — Check unit to ensure all controls ate
functioning correctly and unit operation is normal
Vibrations can cause unwanted noise Check to be sure
no piping is vibrating against any side of unit
System Cleaning — A motor burnout is recognized
by the burnt odor of the refrigerant system When the
motor of a hermetically sealed compressor but ns out, the
insulation of the stator winding forms carbon, water and
acid After burnout, clean refrigerant circuit before a new
motor-compressor is installed installation of a new
capillary and strainer is also recommended when re
placing a compressor after burnout
The system is partially cleaned by back flushing with
relrigerant vapor blown into the suction line and out the
discharge just before connecting the new compressor If
this method is chosen, install a Sporlan C052S (Carrier
No KH41EZ246) lilter drier or equal in the liquid
line, using a capillary tube adapter (Carrier Part No
DEC3680001) An alternate and equally satisfactory
method follows under System Flushing
NOTE Damage to a new compressor caused by failure
to clean the system as recommended is not covered by
the product warranty
System Flushing — Flush with liquid R-22 refrig
erant before the suction line is connected to the new
compressor
1 Clean, flux and solder discharge line to new compressor
NOTE Compressor valves keep relrigerant from
backing out through compressor
2 Makeal/4-in connection to suction line Forexample
Use a 1/2-in x 1/4-in flare reducing coupling
and a/1/2-in. flare nut and tube (flared) and a
1/2-in sweat coupling||that connects to the system
1 /2-in. suction line. For other size suction lines use