Warning, Power supply, Power wiring – Carrier 38AH024-034 User Manual
Page 7
Attention! The text in this document has been recognized automatically. To view the original document, you can use the "Original mode".
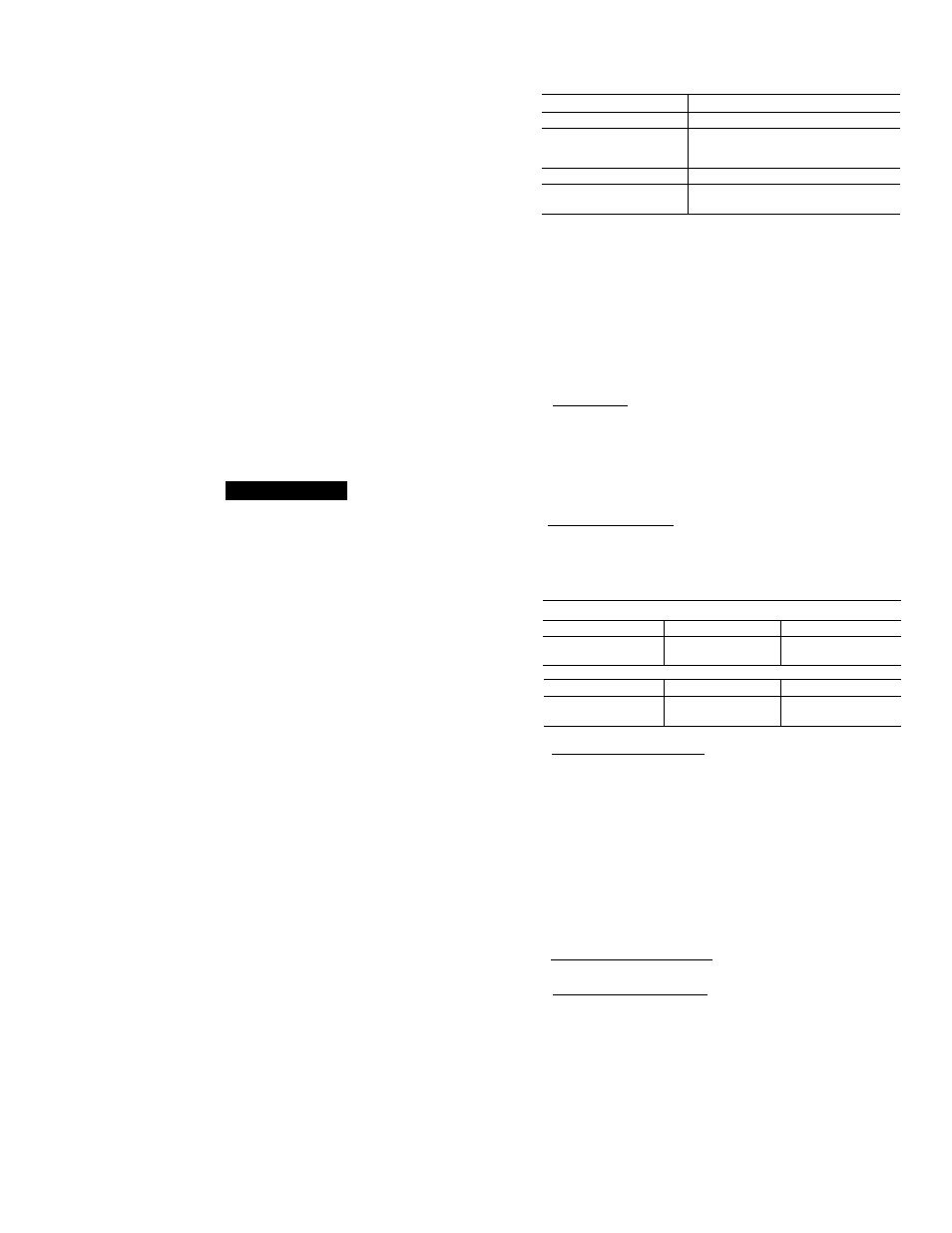
3. Size the suction line from the evaporator through the
riser for high velocity. Suction piping for the high
velocity section should be selected for about 0.5° F
(0.3° C) frietion loss. If a 2° F (1.1° C) loss is allowed
for the entire suction line, 1.5° F (0.8° C) is left for the
balance of the suction line and it should be sized on that
basis.
Check that the high-velocity sizing is ade
quate for oil return up the riser.
If an oil return connection at the bottom of this suction
header is supplied with an evaporator, this connection must
be teed-in ahead of first mixing elbow. When the condens
ing unit is below the evaporator, the riser at the evaporator
does not have to extend as high as the top level of a given
evaporator circuit. After a 15-diameter riser has been pro
vided, the suction line may elbow down immediately.
SAFETY RELIEF — A fusible plug is located on unit liq
uid line before the liquid valve. Other fusible plugs are
located on the compressor(s) and on the suction line(s).
VAV (Variable Air Volume) APPLICATIONS — Field-
supplied suction line accumulators (one per circuit)
(Replacement
Components
Division,
Carrier
Part
No. KH73LZ001) are required for VAV applications in
outdoor units.
A
WARNING
Failure to install accumulator in outdoor unit VAV ap
plications may VOID warranty.
4. Maximum field wire sizes allowed by lugs on terminal
Power Supply
— Electrical characteristics of available
power supply must agree with unit nameplate rating. Sup
ply voltage must be within limits shown in Table 3.
IMPORTANT: Operating unit on improper supply volt
age, or with excessive phase imbalance, constitutes
abuse and may affect Carrier warranty. See Unbal
anced 3-Phase Supply Voltage, page 8.
Power Wiring
— All power wiring must comply with
applicable local and national codes. Install field-supplied
branch circuit fused disconnect(s) per NEC (National Elee-
trical Code [U.S.A. Standard]) of a type that can be locked
OFF or OPEN. Disconnect(s) must be within sight from
and readily accessible from unit in compliance with NEC
Article 440-14.
GENERAL WIRING NOTES
1. A crankcase heater is wired in the eontrol cireuit so it is
always operable as long as power supply disconnect is
on, even if any safety device is open or unit stop-start
switch is off. It is protected by a 5-amp circuit breaker
in control power.
2. The power circuit field supply disconnect should never
be open except when unit is being serviced or is to be
down for a prolonged period. When operation is re
sumed, crankcase heater should be energized for 24 hours
before start-up. If unit is to be shut down for a pro
longed period, it is recommended that the suction and
discharge valves be closed to prevent an excessive ac
cumulation of refrigerant in the compressor oil.
3. Power entry is at compressor end only.
block are as follows:
V-PH-HZ
WIRE SIZE
208/230-3-60
350 kcmil (177.90 sq mm)
380-3-60
460-3-60
575-3-60
2/0 AWG (67 42 sq mm)
230-3-50
350 kcmil (177.90 sq mm)
346-3-50
400-3-50
2/0 AWG (67.42 sq mm)
5. Terminals for field power supply are suitable for cop
per, copper-clad aluminum, or aluminum conductors.
Insulation must be rated 167 F (75 C) minimum.
CONDENSER FANS — The fans must rotate counter
clockwise when viewed from above. If necessary, correct
direction of fan rotation by interchanging any 2 power
input wires at disconneet switch. Affix crankcase heater
decal (located in installer’s packet) to unit disconnect
switch.
FIELD CONNECTIONS
1. Main Power — Bring wires from the fused disconnect
switch through hole in bottom rail of unit to control box
11
12
13
2
.
(Fig. 6) and connect to terminals
on line side of terminal block TBl (see Fig. 7 or 8). To
comply with NEC Article 440-14, the disconnect must
be located within sight from and readily accessible from
the unit.
24-v Control Power — Units have single point power
connections. Control circuit is directly connected inter
nally to unit. Maximum 24-v control circuit is 3.2 amps.
NOTE; For wire runs, use the following sizes of insu
lated wire;
Ft
0-50
50-75
Over 75
No 18 AWG
No 16 AWG
No 14 AWG
35 C Min
35 C Min
35 C Min
0-15.2
15.2-22.9
Over 22.9
0 82 sq mm
1.30 sq mm
2 08 sq mm
35 C Min
35 C Min
35 C Min
3. Control Circuit Interlock — An airflow switch may be
installed in the indoor air handler to prevent unit from
running when indoor air is not flowing. This switch
(Carrier part no. HR81JE001) is available from Service
Parts Center, or equivalent can be field supplied. This
should be electrically interlocked in the control circuit
as shown on the label diagram affixed to the access panel
on end of unit. Note that for a single air handler with
constant volume controls (those shown in Fig. 7 and 8),
the airflow switch must be used in combination with a
relay having 2 sets of normally open contacts (Carrier
part no. HN61KK040 or equivalent). For wiring, see
unit label diagram on inside of unit access door.
4. ModuPanel™ Connections — Refer to Fig. 9 and 10 for
field connections.
5. Transformer Connections — See unit wiring label dia-
gram, notes 1 and 2, located behind compressor com
partment end access door.
IMPORTANT: Ensure power to the crankcase
heater is always on (except when servicing the
unit). If circuit breakers inside unit shut down
the compressor and condenser fans, crankcase heater
remains on.