A warning – Carrier 38AH024-034 User Manual
Page 5
Attention! The text in this document has been recognized automatically. To view the original document, you can use the "Original mode".
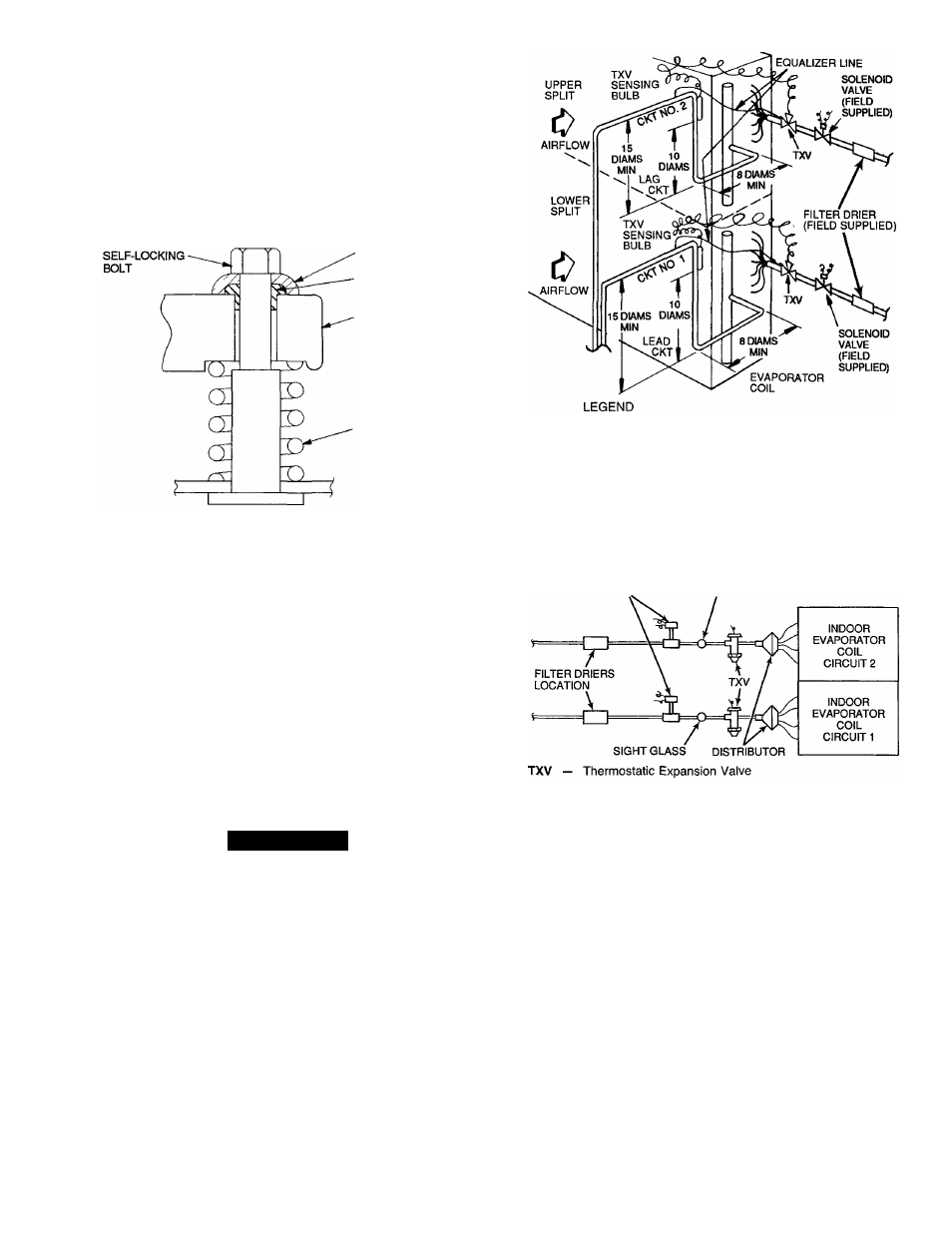
Mounting Unit
— When unit is in proper location, use
of mounting holes in base rails is recommended for secur
ing unit to supporting structure, or for mounting unit on
vibration isolators if required. Fasteners for mounting unit
are field supplied. Be sure to mount unit level to ensure
proper oil return to compressors.
Compressor Mounting
— As shipped, compressor
is held down by 4 bolts. After unit is installed, loosen each
bolt until the snubber washer can be moved with finger pres
sure. See Fig. 3.
SNUBBER FLANGED
WASHER
NEOPRENE
SNUBBER
COMPRESSOR FOOT
ISOLATION SPRING
Fig. 3 — Compressor Mounting
TXV — Thermostatic Expansion Vaive
NOTES:
1. Lower section is first on and last off.
2. For more complete piping information, refer to Carrier System
Design Manual, Part 3, or E20-II refrigerant piping computer
program
Fig. 4 — Suction Line Piping to Unit with
2-Section Coil Split
INSTALLATION
Refrigerant Piping Connections
— Line sizes de
pend on length of piping required between condensing unit
and evaporator. See Table 2A or 2B. It is important to con
sider liquid lift and compressor oil return. Refer to Part 3 of
Carrier System Design Manual for line sizing information,
and Fig. 4 for recommended piping details.
Solenoid Drop Refrigerant Control
— All units
are factory wired to operate on solenoid drop refrigerant
control. A field-supplied liquid line solenoid valve must be
installed in the liquid line ahead of the indoor coil. See
Fig. 5. Wires from solenoid valve do not need to be in con
duit as coil voltage is 24 v (class 2 circuit).
A WARNING
Failure to properly install liquid line solenoid at the in
door unit as described, without Carrier authorization,
may VOID warranty.
fie
L
d
-
supplied
SOLENOID VALVE
SIGHT GLASS
Filter Drier and Moisture Indicator
— Every unit
should have a filter drier and a sight glass (moisture indi
cator) field installed. Select the filter drier for maximum
unit capacity and minimum pressure drop. Figure 5 shows
recommended locations of filter drier(s) and sight glass(es).
Complete the refrigerant piping from the evaporator to the
condenser before opening the liquid and suction lines at the
condensing unit.
Receiver
— No receiver is provided with the unit; it is
recommended that one not be used.
Piping Procedure
— Do not remove run-around pipe
from suction and liquid line stubs until piping connections
Fig. 5 — Liquid Line Solenoid Valve,
Filter Drier(s), and Sight Glass Locations
are ready to be made. Pass nitrogen or other inert gas through
piping while brazing, to prevent formation of copper oxide.
Install field-supplied thermostatic expansion valve (TXV)
in liquid line ahead of each evaporator section.
SUCTION PIPING AT EVAPORATOR AND TXV BULB
LOCATION (See Fig. 5) — The purpose of these recom
mendations is to achieve good mixing of the refrigerant leav
ing the evaporator suction header for proper sensing by the
TXV bulb.
1. A minimum of two 90 degree elbows must be installed
upstream of the expansion valve bulb location.
2. The TXV sensing bulb should be located on a vertical
riser where possible. If a horizontal location is neces
sary, secure the bulb at approximately the 4 o’clock
position.
Copy continued on page 7.