A caution – Carrier 38AH024-034 User Manual
Page 18
Attention! The text in this document has been recognized automatically. To view the original document, you can use the "Original mode".
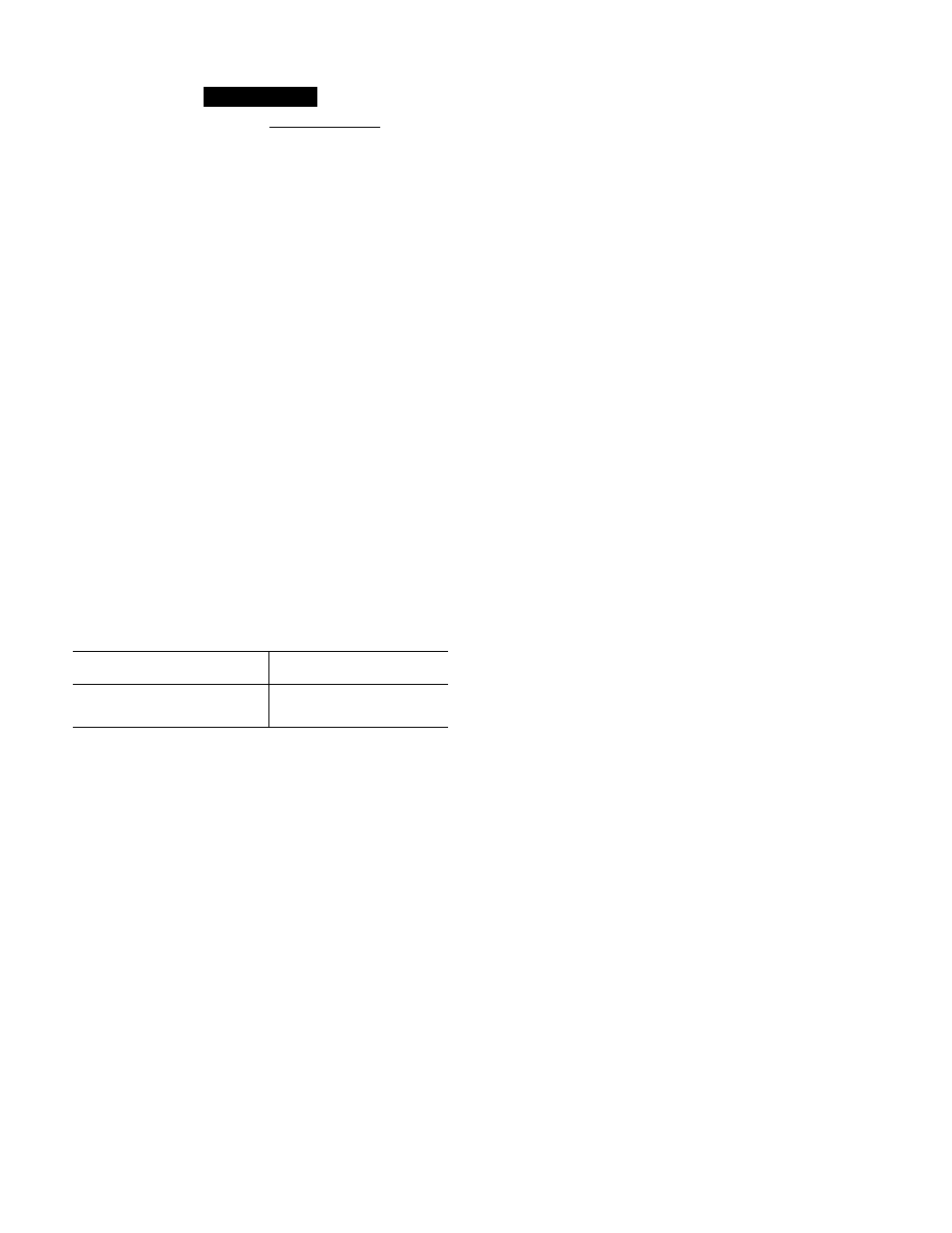
SERVICE
A
CAUTION
I
Tum off all power to unit before proceeding.________
Access for Servicing (See Fig. 13)
COMPRESSOR SECTION — The compressor compart
ment has 2 side doors and one front door for servicing, pro
viding access to compressors, all components of the refrig
eration system, electrical controls, and control box. After
opening the front door an inner cover must be removed for
access to control box.
OIL PRESSURE SAFETY SWITCH - Switch is reset by
opening either access door on either side of the unit. Circuit
no. 1 oil pressure safety switch is reset by opening the side
access door on the left side of the unit (as viewed from the
compressor end). Circuit no. 2 oil pressure safety switch is
reset by opening the side access door on the right side of
the unit. Circuit no. 1 liquid line service valve is located
directly below circuit no. 1 oil pressure switch. Circuit
no. 2 liquid line service valve is located directly below cir
cuit no. 2 oil pressure switch.
CONDENSER SECTION — Condenser-fan motors and fans
can be serviced by removal of outlet grilles or side panels.
If a fan motor is serviced, be sure the wire fan guard is in
place over each fan before starting unit. See Fig. 14 for
proper fan adjustment. Tighten fan hub securely on motor
shaft with setscrew which bears against the key. Be sure to
replace Permagum and rubber cap over end of motor shaft
to protect against moisture causing fan to rust on shaft. Re
check rotation of fan(s) after service work on motors.
Fan Adjustment (See Fig. 14)
Oil Charge
— Compressors are factory charged with oil
as follows:
COMPRESSOR
AMOUNT
pints (liters)
06D824
10 (4.73)
06D328
10 (4.73)
06D537
10 (4.73)
When additional oil or a complete charge is required, use
only Carrier-approved compressor oil:
Petroleum Specialities.......................................... Cryol 150A
Texaco, Inc......................................................Capella WF-32
Witco Chemical Corp .......................................... Suniso 3GS
IMPORTANT: Do not use drained oil or use oil that
has been exposed to atmosphere. Refer to GTAC II,
Module 5; Charging, Recovery, Recycling, and Rec
lamation for procedures to add oil. To remove excess
oil. Isolate the compressor by use of the service valves,
slowly relieve the internal pressure, and then use the
oil drain plug at the bottom of the compressor to re
move the excess oil.
Liquid Shutoff/Charging Valve
— Valve is lo
cated inside the compressor compartment and is provided
with Vi-in. flare connection for field charging.
Capacity Control, Suction Pressure — Actu
ated Unloaders
— Each controls 2 cylinders. Unload
ers are factory set (see Table lA or IB) but may be field
adjusted.
CONTROL SET POINT — The control set point (cylin
der load point) is adjustable from 0 to 85 psig (0 to
586 kPa). To adjust, turn control set point adjustment nut
(Fig. 15) clockwise to its bottom stop. In this position,
set point is 85 psig (0 to 586 kPa). Then tum adjustment
counterclockwise to desired control set point. Every full
turn counterclockwise decreases set point by 7.5 psig
(51.7 kPa).
PRESSURE DIFFERENTIAL - The pressure differential
(difference between cylinder load and unload points) is ad
justable from 6 to 22 psig (41 to 15.2 kPa). To adjust, tum
pressure differential adjustment screw (Fig. 15) counter
clockwise to its backstop position. In this position, differ
ential is 6 psig (41 kPa). Then, tum adjustment clockwise
to desired pressure differential. Every full turn clockwise
increases differential by 1.5 psig. (10.34 kPa).
Capacity Control, Electrically Operated Unload
ers (Variable Air Volume, Factory-Installed
Option Units)
— Each controls 2 cylinders. Electric
unloaders are not field adjustable. Circuit no. 1 compressor
on this factoiy-installed option has 2 electric unloaders. For
service, replace any failed solenoid.
Oil Pressure Safety Switch (OPS)
— In the con
trol circuit, switch stops the compressor and unit, if proper
oil pressure differential is not established at start-up or main
tained during operation. If OPS stops the unit, determine
the cause and correct before restarting unit. Failure to do so
will constitute abuse. Equipment failure due to abuse may
void the warranty.
Compressor Protection
CIRCUIT BREAKER — Calibrated trip manual reset, am
bient compensated, magnetic breaker protects against
motor overload and locked rotor conditions.
COMPRESSOR OVERTEMPERATURE PROTECTION
(COTP) — A thermostat installed on compressor motor wind
ing reacts to excessively high winding temperatures and shuts
off the compressor.
TIME GUARD® Control — Control prevents compressor
from short cycling. See Sequence of Operation.
CRANKCASE HEATERS — Heaters minimize absorption
of liquid refrigerant by oil in crankcase during brief or ex
tended shutdown periods. The control circuit is maintained
if compressor fan motor circuit breakers are turned off. The
main disconnect must be on to energize crankcase heater.
IMPORTANT: Never open any switch or disconnect
that deenergizes the crankcase heaters unless unit is
being serviced or is to be shut down for a prolonged
period. After a prolonged shutdown on a service job,
energize the crankcase heaters for 24 hours before start
ing the compressor.
High-Pressure Switches
— Switches have fixed,
nonadjustable settings. Switches are mounted on the
compressors.
Low-Pressure Switches
— Switches have fixed, non
adjustable settings. The switches are mounted on the
compressors.
TO CHECK — Slowly close liquid shutoff valve and allow
compressor to pump down. Do not allow compressor pump
down below 2 psig (13.8 kPa). Compressor should shut down
when suction pressure drops to cutout pressure in Table 4,
and should restart when pressure builds up to cut-in pres
sure shown.
18