A caution – Carrier 38AH024-034 User Manual
Page 14
Attention! The text in this document has been recognized automatically. To view the original document, you can use the "Original mode".
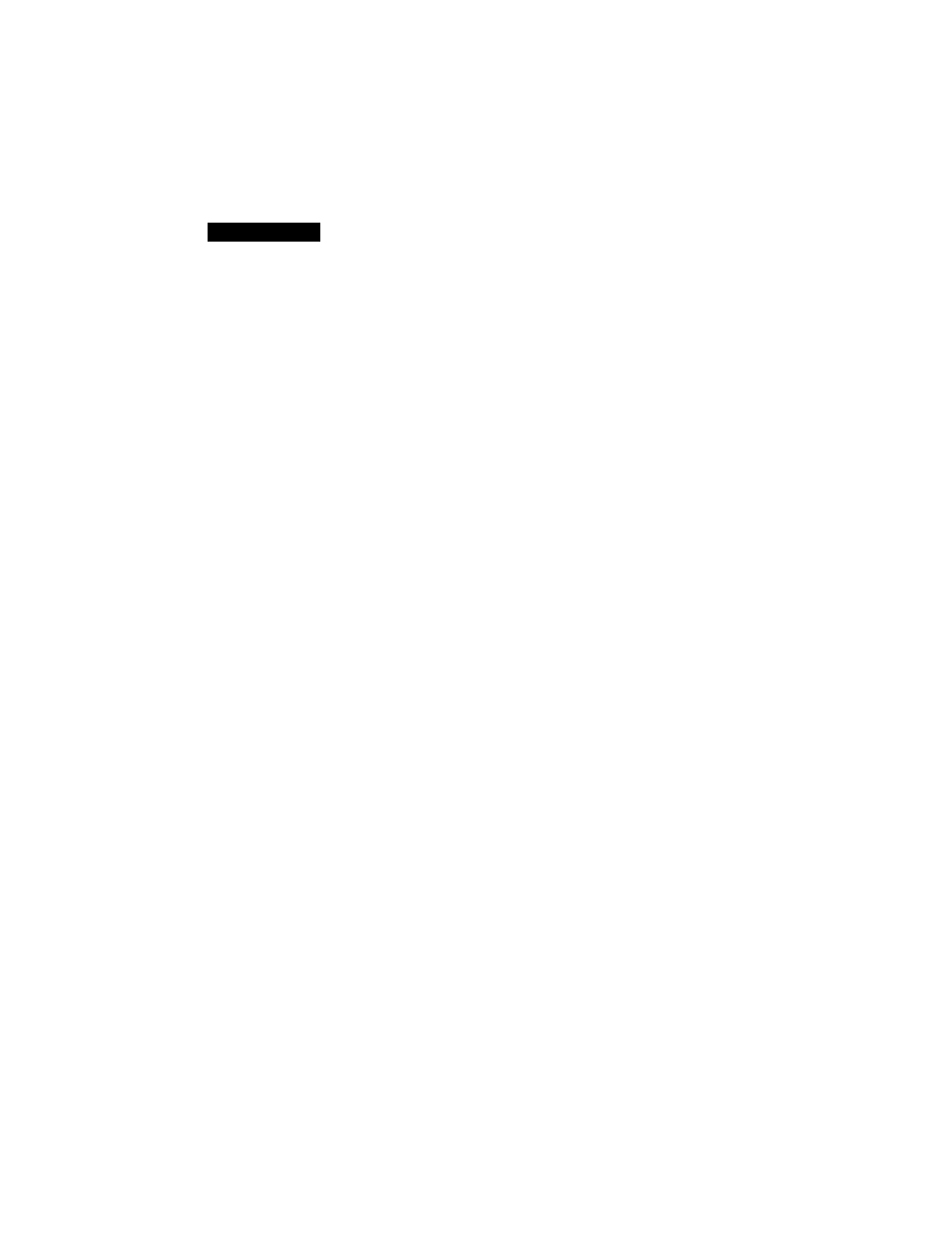
PRE-START-UP
IMPORTANT: Before beginning Pre-Start-Up or
Start-Up, review Start-Up Checklist at the back of this
book. The Checklist assures proper start-up of a unit
and provides a record of unit condition, application
requirements, system information, and operation at ini
tial start-up.
A
CAUTION
Do not attempt to start the condensing unit, even
momentarily, until the following steps have been com
pleted. Compressor damage may result.
System Check
1. Check all air handler(s) and other equipment auxiliary
components. Consult the manufacturer’s instructions re
garding any other equipment connected to the condens
ing unit. If unit has field-installed accessories, be sure
all are properly installed and correctly wired. If used,
airflow switch must be properly installed. See Fig. 9
or 10.
2. Backseat (open) compressor suction and discharge valves.
Now close valves one turn to allow refrigerant pressure
to reach test gages.
3. Open liquid line service valves.
4. Check tightness of all electrical connections.
5. Compressor oil level should be visible in sight glass.
Adjust the oil level as required. No oil should be
removed unless the crankcase heater has been ener
gized for at least 24 hours. See Service section. Oil
Charge on page 18.
6. Be sure unit is properly leak checked, dehydrated, and
charged. See Preliminary Charge, below.
7. Electrical power source must agree with nameplate
rating.
8. Crankcase heater must be firmly locked into compres
sor crankcase. Be sure crankcase is warm (heater must
be on for 24 hours before starting compressor).
9. Fan motors are 3-phase. Check rotation of fans during
first start-up check. Fan rotation is counterclockwise
as viewed from top of unit. If fan is not turning
counterclockwise, reverse 2 of the power wires.
10. Be sure compressor floats freely on the mounting springs
and that snubber washers can be moved with finger pres
sure. See Compressor Mounting, page 5, and Fig. 3
for loosening compressor bolts.
Leak Test and Dehydration
— Leak test the entire
refrigerant system using soap bubbles and/or an electric
leak detector. Evacuate and dehydrate entire refrigerant sys
tem by use of methods described in GTAC II, Module 4,
System Dehydration.
Preliminary Charge
— Refer to GTAC II, Module 5,
Charging, Recovery, Recycling, and Reclamation for charg
ing methods and procedures. Charge each system with R-22
by the liquid charging method (through liquid service valve)
on the high side. See approximate refrigerant charge in
Table 1A or IB. Charge according to the values in the Charg
ing Chart, Eig. 11, page 16.
START-UP
Compressor crankcase heaters must be on for 24 hours
before start-up. To energize the crankcase heaters, set the
space thermostat above the ambient so there will be no de
mand for cooling. Close the field disconnect and turn on
the fan circuit breakers. Leave the compressor circuit break
ers off/open. The crankcase heaters are now energized.
After the heater has been on for 24 hours, the unit can be
started. If no time has elapsed since the preliminary charge
step has been completed, it is unnecessary to wait the
24-hour period.
Preliminary Checks
1. Ensure that compressor service valves are backseated.
2. Verify that each compressor floats freely on its mount
ing springs.
3. Check that electric power supply agrees with unit name
plate data.
4. Verify that compressor crankcase heaters are securely in
place.
5. Check that compressor crankcase heaters have been on
at least 24 hours.
6. Note that compressor oil level is visible in the sight glass.
7. Recheck for leaks using same procedure as previously
outlined in Pre-Start-Up section. Leak Test and De
hydration, this page.
8. If any leads are detected, evacuate and dehydrate as pre
viously outlined in Pre-Start-Up section. Leak Test and
Dehydration, this page.
Preliminary Oil Charge
— Each compressor is fac
tory charged with oil (see Table lA or IB). When oil is
checked at start-up, it may be necessary to add or remove
oil to bring it to the proper level. One recommended oil
level adjustment method is as follows:
ADD OIL — Close suction service valve and pump down
crankcase to 2 psig (14 kPa). (Low-pressure switch must be
jumpered.) Wait a few minutes and repeat until pressure re
mains steady at 2 psig (14 kPa). Remove oil fill plug above
the bull’s-eye, add oil through plug hole, and replace plug.
Run compressor for 20 minutes and check oil level.
NOTE: Use only Carrier approved compressor oil. Ap
proved sources are:
Petroleum Specialties Inc..................................... Cryol 150A
Texaco, Inc......................................................Capella WF-32
Witco Chemical Co...............................................Suniso 3GS
Do not use oil that has been drained out, or oil that has
been exposed to atmosphere.
REMOVE OIL — Pump down compressor to 2 psig
(14 kPag). Loosen the Ut-in. (6.4 mm) pipe plug at the com
pressor base and allow the oil to seep out past the threads
of the plug.
NOTE: The crankcase will be slightly pressurized. Do not
remove the plug, or the entire oil charge will be lost.
Small amounts of oil can be removed through the oil pump
discharge connection while the compressor is running.
Start Unit
— The field disconnect is closed, the fan cir
cuit breaker is closed and the space thermostats are set above
ambient so that there is no demand for cooling. Only the
crankcase heaters will be energized.
i
14