Design considerations, Thermal management, 7design considerations – Kontron COMe-bCD2 User Manual
Page 36
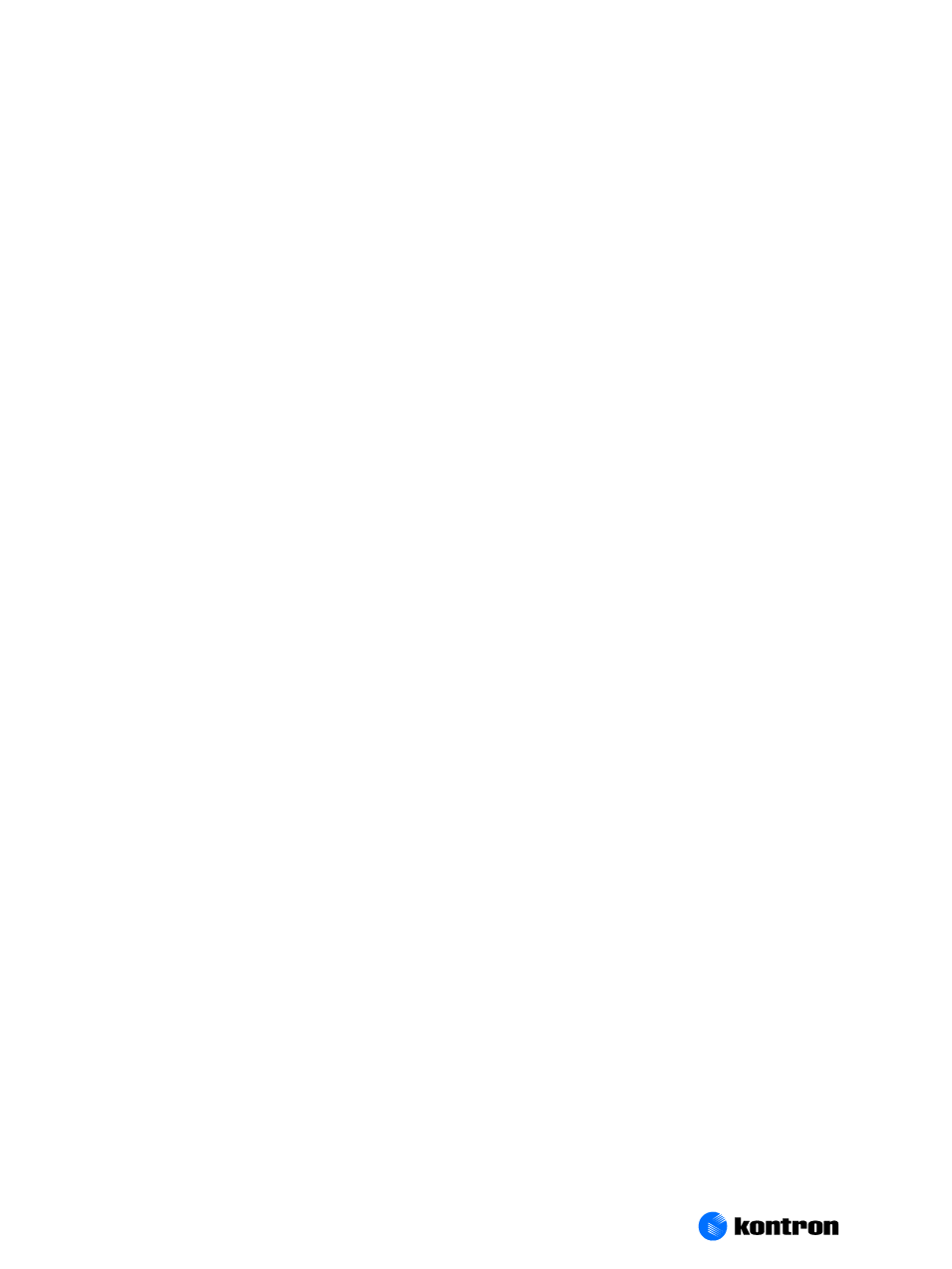
7 Design Considerations
Kontron User's Guide ETXexpress® CD
36
7
Design Considerations
7.1
Thermal Management
A heat-spreader plate assembly is available from Kontron Embedded Modules for the COMe-bCD2. The
heat-spreader plate on top of this assembly is NOT a heat sink. It works as an ETXexpress®-standard
thermal interface to use with a heat sink or other cooling device.
External cooling must be provided to maintain the heat-spreader plate at proper operating
temperatures. Under worst-case conditions, the cooling mechanism must maintain an ambient air and
heat-spreader plate temperature of 60° C or less.
The aluminum slugs and thermal pads on the underside of the heat-spreader assembly implement
thermal interfaces between the heat spreader plate and the major heat-generating components on the
COMe-bCD2. About 80 percent of the power dissipated within the module is conducted to the heat-
spreader plate and can be removed by the cooling solution.
For 2166MHz modules, the heat dissipated into the plate ranges from 45 to 55 watts. Design a cooling
solution to dissipate the heat load on a heat-spreader plate at a minimum of 55 watts to accommodate
all COMe-bCD2 modules.
You can use many thermal-management solutions with the heat-spreader plates, including active and
passive approaches. The optimum cooling solution varies, depending on the COM Express® application
and environmental conditions. Please see the COM Express® Design Guide for further information on
thermal management.