ETS-Lindgren SMART 1000 Mini-Reverb Cell User Manual
Page 10
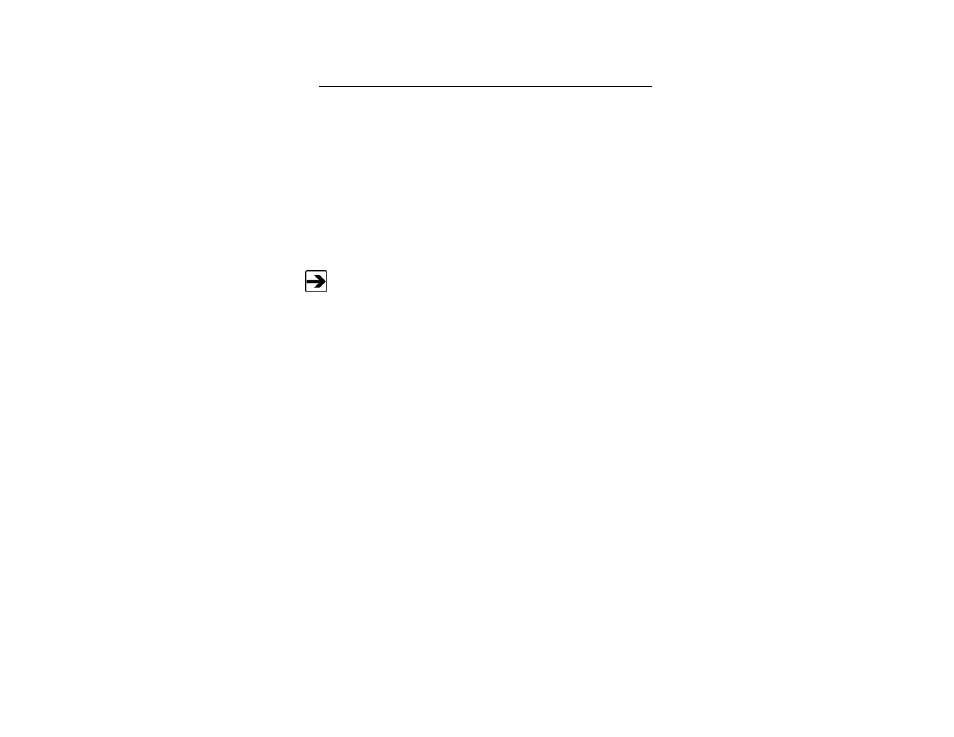
10
|
Maintenance
Tuners
The SMART™ (Statistical Mode Averaging Reverberation Test Site) chamber
tuners are manufactured from rigid structure of gatorboard covered with copper
sheet on the Z-fold section to provide the necessary reflective surface, or of an
aluminum frame with aluminum reinforced sheet reflectors.
No maintenance of the box structure is required in normal use. However, the
surfaces may be dusted or vacuumed periodically to maintain their appearance.
The tuners are supported at their ends only with coupling clamps. These should
be inspected monthly for signs of wear, loose screws, or distortion.
The motors mounted external to the chamber are fixed to the chamber
wall and additionally supported either on a separate frame or the
chamber supports. The motor shaft passes into the chamber through
a shielded penetration fitted to the chamber wall. The horizontal
penetration also ensures that the axial load is not transmitted to the
motor from the tuner.
The RF feed through bearing assembly on the motor side and a self-aligning (on
large chambers) idler bearing on the non-driven end supports the horizontal
tuner. The self-aligning bearing assemblies have a grease nipple that should be
topped off every six months using standard bearing grease. They should also be
checked periodically to ensure free movement and that fixings remain secure.
The tuner body needs only periodic cleaning to remove any accumulated dust.
On all chambers the RF feed-through assembly on the motor side of the tuner
contains a large number of ball bearings. These provide the RF shielding of the
gear shaft as it passes through the shield and should not be removed.
On the SMART 1000 model the tuners are much smaller and subject to less
wear. The tuners should be inspected every six months for signs of excessive
noise or motor overheating. The tuners are lubricated at the factory, so additional
lubrication should not be required.