Attwood Integrated Fuel Demand Valve User Manual
Integrated fuel demand valve, Caution, 99ifdv series
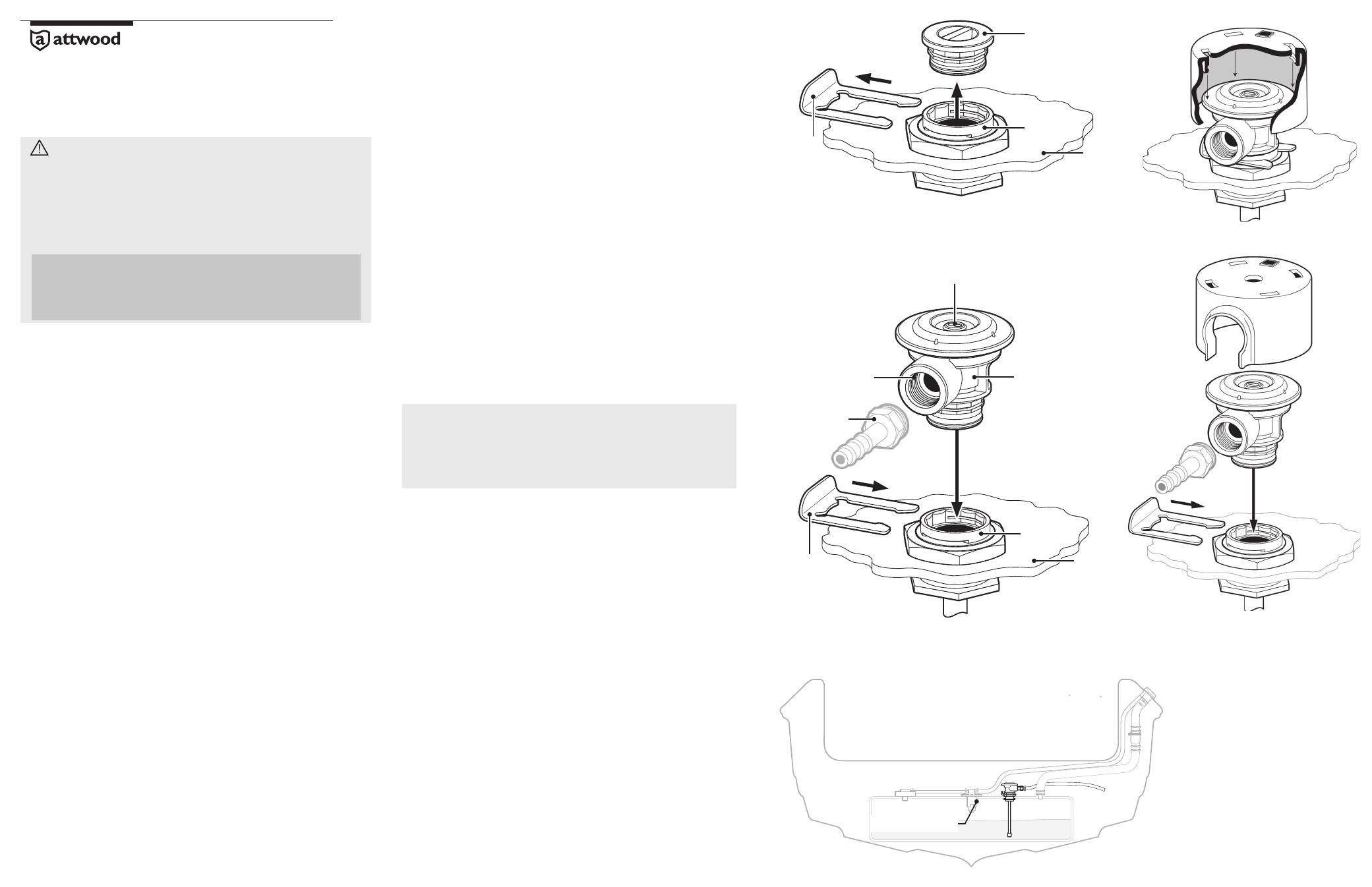
INTEGRATED FUEL DEMAND VALVE
99IFDV Series
INSTALLATION INSTRUCTIONS
8/2014
69487 Rev. D
SAVE THESE INSTRUCTIONS
CAUTION:
The vessel manufacturer must comply with the requirements of CFR
40 1060.202. Any questions can be directed to www.attwood.com
Failure to follow these instructions may result in accidental fuel
system over-pressurization. Users must follow these instructions to
ensure vessel function and operation
EMISSION-RELATED INSTALLATION INSTRUCTIONS
Failing to follow these instructions when installing the Attwood
Integrated Fuel Demand Valves in a piece of nonroad equipment violates federal law
(40 CFR 1068.105(b)), subject to fi nes or other penalties as described in the Clean
Air Act.
FEATURES:
Attwood’s Integrated Fuel Demand Valve meets EPA regulations. The Fuel
Demand Valve can be oriented in twelve (12) different positions providing optimal
orientation. The Fuel Demand Valve also has a manual override built into the top.
REQUIRED FOR INSTALLATION
• Pliers for removal and assembly of retainer clip
• Appropriate hose fi tting (1/2" NPT)
• Marine-grade urethane-based sealant (Attwood #30106-6 recommended, DO
NOT USE A SILICONE-BASED SEALANT)
• Wrench for fi tting
LOCATION
• Mount of fl at surface where risk of torsional loads being applied to the Integrated
Fuel Demand Valve is minimal
• Locate in position where consumers will not kick or step on the valve
• A heat shield (99IFDVHS1) is recommended to protect against fi re unless the
Fuel Demand Valve passes USCG fi re test in the as-installed position. If heat
shield is required, see separate installation sheet.
INSTALLATION INSTRUCTIONS
1. Locate built in Fuel Demand Valve aluminum base on tank
2. Remove clip and transport plug (Figure 1)
3. Install necessary barb fi tting or anti-siphon valve (1/2" NPT, not supplied).
Use thread sealant.
4. Torque up to 8 lb-ft where applicable. Do not over torque.
Ensure sealing surface (interior of insert) is clean of debris
5. Remove shipping cover from valve assembly.
6. Lubricate O-ring with a petroleum based lubricant such as motor oil. Insert Fuel
Demand Valve to predetermined orientation (Figure 2). Once inserted, apply
slight downward pressure on Valve and install retainer clip fully into slot.
7. Once installed, apply slight upward pressure to Fuel Demand Valve to ensure it
is locked into position.
8. Pressure test tank to ensure connection integrity, per CFR 33 183.580, at
pressure of 3 psi for no less than 10 minutes. Inspect all connections for leak
by method other than pressure decay.
9. If 99IFDVHSI is installed, align top hole with the top of the vent cap and snap in
place. (Figure 3 & 4)
MANUFACTURER REQUIREMENTS
Manufacturer must determine required amount of anti-siphon protection
for specifi c vessel confi guration per CFR 33. Manufacturer must ensure
that engine fuel distribution line vacuum requirements are met. See engine
manufacturer for details.
The information below applies only to EPA CFR 40 1060.135. The vessel
manufacturer is responsible to meet all additional regulatory labeling
requirements including EPA, CARB, USCG and others as necessary. The below
information is for reference only. The vessel manufacturer should refer to CFR
40 for complete labeling guidelines.
In order to meet the requirements of CFR 40 1060.135, the vessel must be labeled
with respect to evaporative emissions in the following manner when installing
certifi ed components;
Excerpt from CFR 40 1060.135
(a) You must affi x a permanent and legible label identifying each engine or piece of equipment before introducing it into
U.S. commerce. The label must be—
(1) Attached in one piece so it is not removable without being destroyed or defaced.
(2) Secured to a part of the engine or equipment needed for normal operation and not normally requiring
replacement.
(3) Durable and readable for the equipment’s entire life.
(4) Written in English.
(5) Readily visible in the fi nal installation. It may be under a hinged door or other readily opened cover. It may not
be hidden by any cover attached with screws or any similar designs. Labels on marine vessels must be visible from
the helm.
(c) If you produce equipment without certifying with respect to evaporative emissions, the equipment label specifi ed in
paragraph (a) of this section must—
(1) State: ‘‘MEETS U.S. EPA EVAP STANDARDS USING CERTIFIED COMPONENTS.’’
(2) Include your corporate name.
Below is an example of a label specifi ed by CFR40 1060.135 for use with certifi ed components;
MEETS U.S. EPA EVAP STANDARDS USING CERTIFIED
COMPONENTS
CORPORATE NAME
Please refer to CFR 40 1060.135 to review EPA vessel labeling requirements.
The NMMA has a program to supply OEM builders with labels. Please refer to the
NMMA website below for further information regarding the NMMA label program;
www.nmma.org/certifi cation/products/labelsanddecals.aspx
TWO-YEAR WARRANTY & LIABILITY
Generally:
Attwood Integrated Fuel Demand Valves are covered by a two (2) year limited warranty
from the date of a Vessel’s fi rst retail sale.
Pre-requisites to Warranty Eligibility:
For the warranty coverage described herein to apply, the
following conditions must be met:
• Component must have been properly installed per Attwood installation instructions; and
• The component cannot have been altered or abused by Boat Company or its customers.
Warranty Terms for Components:
Attwood warrants that any Attwood Integrated Fuel Demand Valves are free from defects in materials
and workmanship and are designed, built, and equipped to conform at the time of sale to Boat Company
with the 40CFR.1060 requirements. For two (2) years from the date of a Program Boat’s fi rst retail sale,
Attwood will, at its sole option, repair or replace any components that fail due to a defect in material or
workmanship. ATTWOOD PROVIDES NO WARRANTIES WITH RESPECT TO ANY PART OR COMPONENT
NOT MANUFACTURED BY ATTWOOD, INCLUDING FUEL TANKS. Boat Company is responsible for the
installation of all Systems, whether installed by Boat Company or under its direction.
A.B.Y.C.
American Boat & Yacht Council
3069 Solomon’s Island Road
Edgewater, Maryland 21037
www.abycinc.org
U.S. Coast Guard
Washington, DC 20460
www.uscgboating.org
E.P.A.
401 “M” Street, SW
Washington, DC 20593 www.
www.epa.gov
ISO
iso.org
National Marine Manufacturers
Association (NMMA)
231 S. LaSalle Street
Suite 2050
Chicago, IL 60604
www.NMMA.org
Fuel Demand Valve
FIGURE 1
FIGURE 2
Tank
Tank
Clip
Clip
Transport
Plug
Valve
Assembly
Use thread
sealant
For Override
Using a small fl at head screwdriver,
press downward through slot
Anti-Siphon Valve
or Barbed Fitting
not included
Molded Nut
Molded Nut
©2014 Attwood Corporation
1016 North Monroe Lowell, MI 49331
www.attwoodmarine.com
FIGURE 4
Full Pressure Relief System
FIGURE 3