Arcmaster 401s power source – Tweco ArcMaster 401S User Manual
Page 31
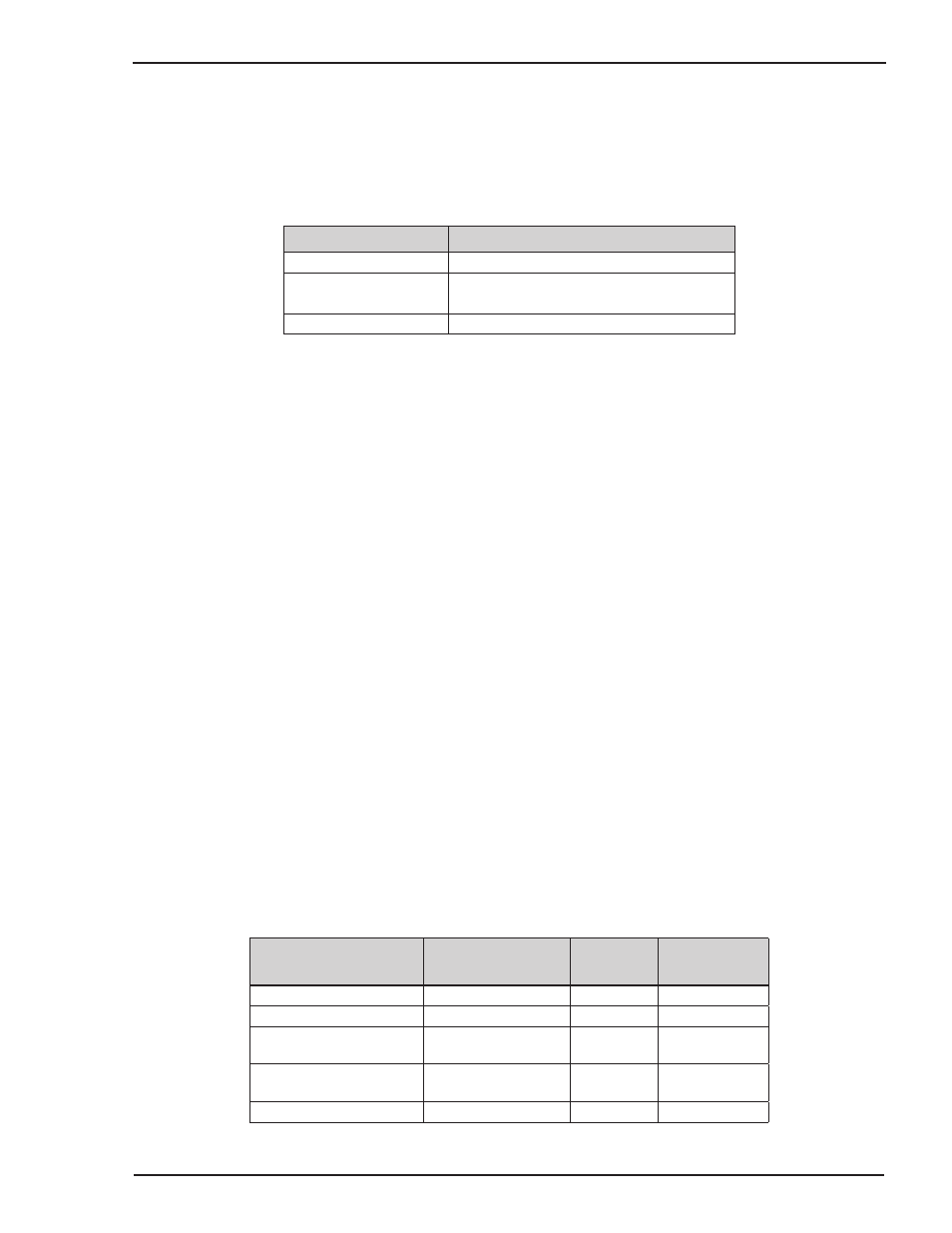
ARCMASTER 401S POWER SOURCE
Manual 0-5345
3-11
INSTALLATION, OPERATION AND SETUP
ARC FORCE CONTROL
This parameter encoder controls in STICK mode only and is used to adjust percentage increase in welding
current and is proportional to arc length (arc voltage). This control provides an adjustable amount of arc control
(or dig). This feature can be particularly beneficial in providing the operator with the ability to compensate for
variability in joint fit up in certain situations with particular electrodes, e.g. cellulose and hydrogen controlled
electrodes. In all welding processes, the amount of penetration obtained is dependent on the welding current;
i.e. the greater the penetration, the greater the current.
Arc Force Position
Effect on Welding Performance
Minimum (0)
Soft arc, Low spatter, Low penetration
Medium (100%)
Normal arc, Improved fusion
characteristics, Normal penetration
Maximum (200%)
Hard arc, Deep penetration
Table 3-5 Weld Parameter Descriptions
In general, having the Arc Force set at 200% (maximum) allows greater penetration to be achieved. With the
ARC set at 0% (minimum) the Power Source has a constant current characteristic. In other words, varying the
arc length does not significantly affect the welding current. When the Arc Force is set to 100%, it is possible
to control the welding current by varying the arc length. This is very useful for controlling penetration and
side wall wash on vertical up fillet welds.
i) Root runs
During root runs the weld pool forms a “keyhole” shape. If too much weld current is used, the hole blows
out and the weld collapses. If too little weld current is used, the hole closes up and penetration is lost. The
size of the hole also determines the arc length; i.e. as the hole gets bigger, the arc gets longer.
If arc force is used, the increase in the arc length causes the weld current to decrease until the hole starts
to close up but if the hole closes up to much then the arc length decreases which causes the weld current
to increase. Too little or too much arc force makes this process unstable. The operator must adjust the
arc force until a happy medium is reached.
ii) Vertical up welding
When welding vertical up with arc force on, the operator can control the amount of current by changing arc
length, i.e. voltage. Weld metal is deposited by “digging” the electrode into the side of the base metal joint
and then increasing the arc length with a flicking motion, to allow the weld pool to freeze, before digging
the electrode into the other side of the base metal joint.
Without arc force, increasing the arc length does not decrease the weld current sufficiently and the operator
has to manually decrease the current via a Remote Control to freeze the weld pool. This welding current
reduction also reduces the penetration.
The arc force allows the weld pool to freeze during the “flick” phase without decreasing the amount of weld
current available during the “dig” phase thus maximizing penetration.
Weld
Parameter
Parameter Range
Factory
Setting
Incremental
Unit
HOT START (TIG)
50 to 200%
50%
1%
HOT START (STICK)
100 to 200%
125%
1%
WELD (A) (1 phase)
TIG or STICK
10 to 300A
100A
1A
WELD (A) (3 phase)
TIG or STICK
10 to 400A
100A
1A
ARC FORCE
0 to 200%
100%
1%
Table 3-6 Weld Parameter Setting