Pierce lead-in overrun at end of cut – Tweco Dynamics Automation User Manual
Page 14
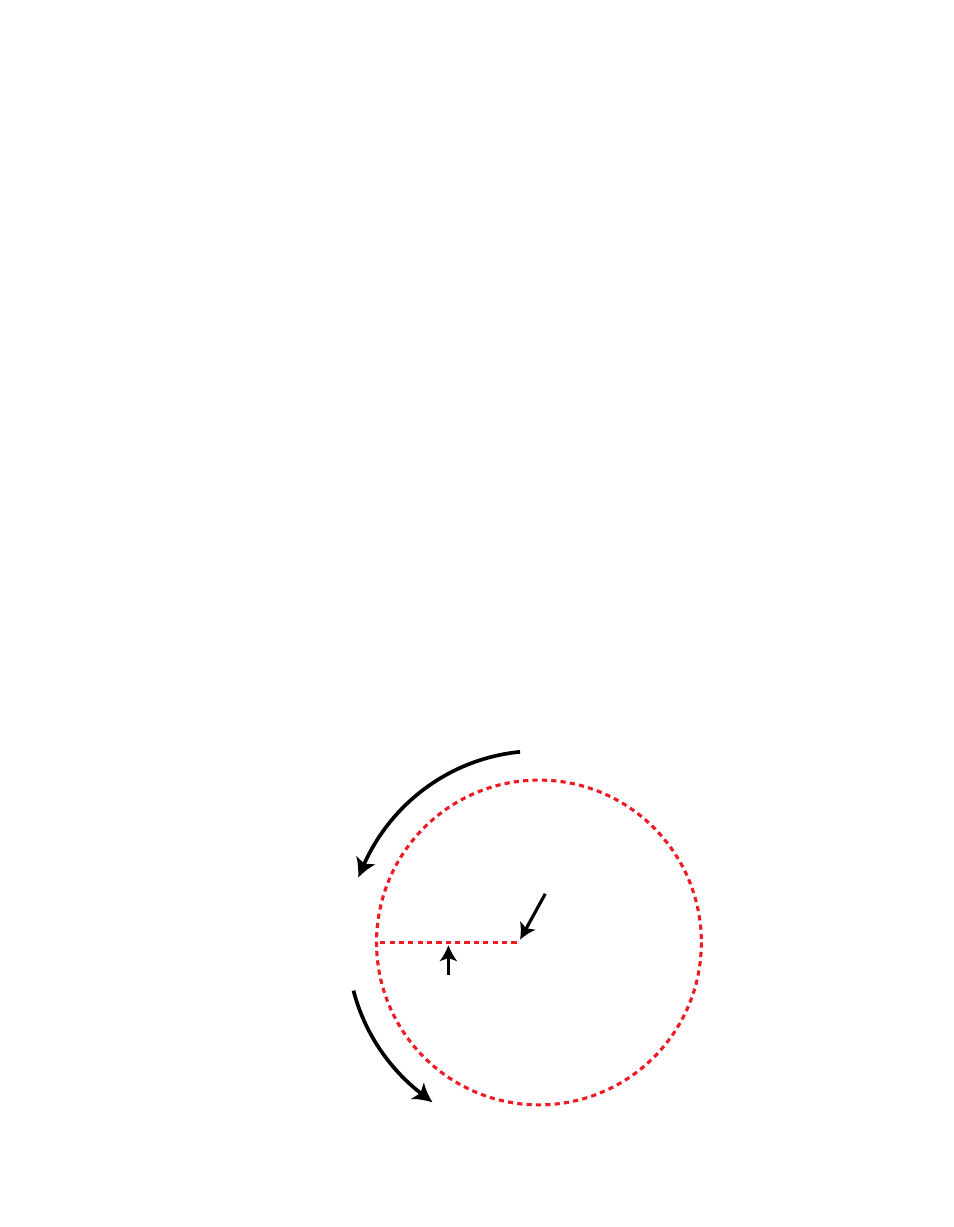
Cutting Circles
Circle cutting demands precise motion control and circle cut quality will vary as the circle
diameter approaches the thickness of the plate. In general, a circle that is equal in diameter
to the thickness of the plate being cut is the minimum circle diameter possible. Cut quality will
decrease markedly when the circle diameter is less than 1.5 times the thickness of the plate
being cut.
For maximum circle cut quality:
1.
Slow down cut speed. Smaller circles may require a cut speed that is 60-50% of the
speed specified in system cut charts. A slower cut speed will eliminate trailing arc and allow the
arc to cut at closer to 0° of bevel.
2.
Maintain constant cut height through the circle. This may require locking out the height
controller. As the cut speed slows, arc voltage increases and the height controller tends to drive
the torch down, changing cut bevel. Avoid torch height movement by locking out the height
controller during the circle cut.
3.
Start the cut in the center of the circle and use a 90° lead-in to the circle. When the
positioner is in top running condition, a 90° lead-in will produce less distortion at the circle
initiation. A cutting table with backlash may produce a better cut when a radial lead-in is used.
4.
End the cut by overburning the circle cut line rather than by using a lead-out. Time the
cut to end just as the arc completes the circle. A lead out or too much of an overburn will cause
the arc to cut more of the outside of the circle and cause a distortion at the point where the
circle cut is completed. Many CNC systems use and advanced off feature to ramp down cutting
current end of cut. Use of the CNC’s advanced off feature will improve circle cutting.
Pierce
Lead-in
Overrun
at end
of cut
page 1