Page 1 – Tweco Dynamics Automation User Manual
Page 13
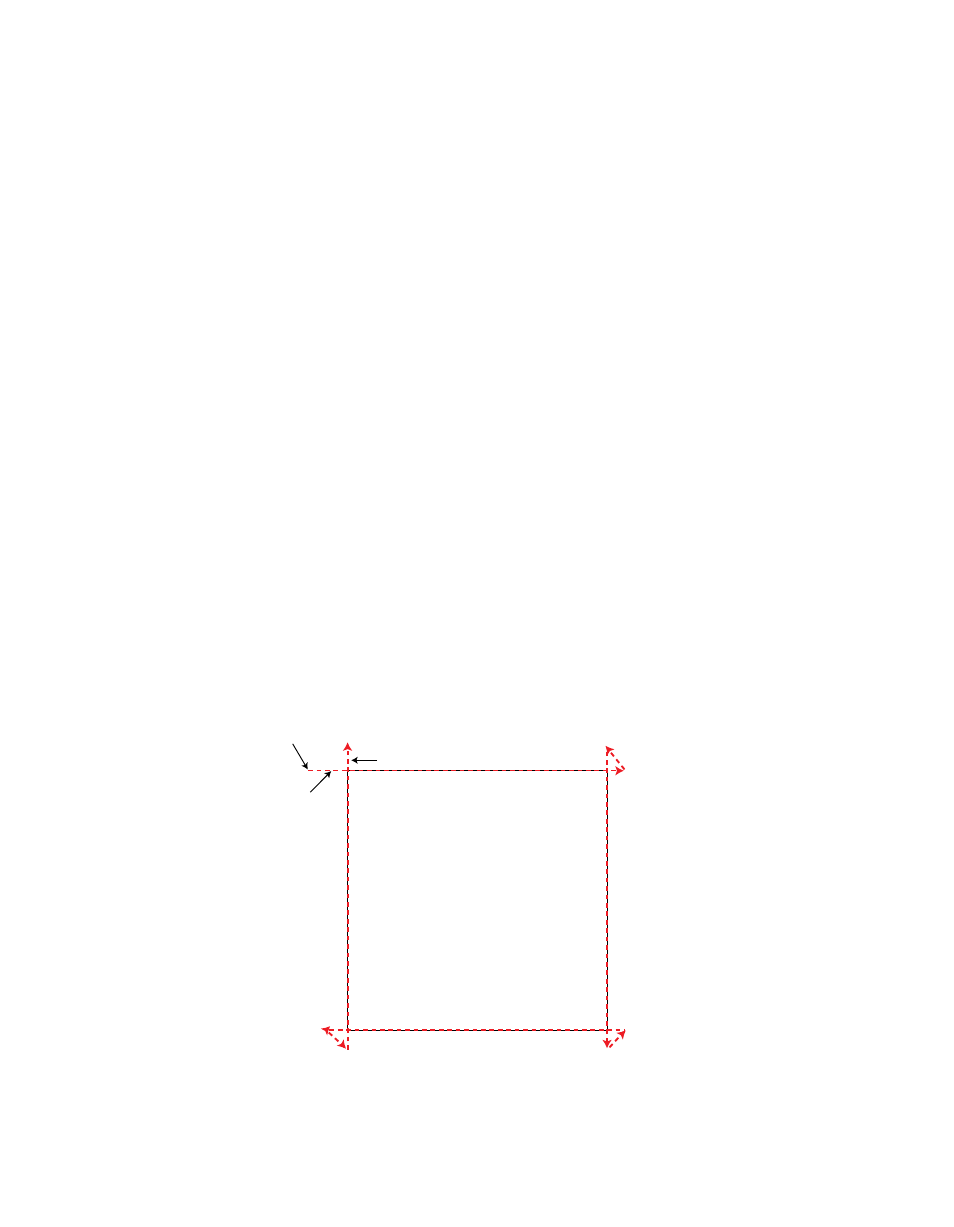
Corners
The cutting arc normally trails the torch tip orifice. When the torch makes an abrupt
change in direction this trailing arc cannot change direction as quickly at the bottom of the cut
as at the top of the cut. This results in undercutting of sharp corners. 2 techniques can be used
to minimize this effect.
1. Use cut-outs – Overcut past the corner of the shape, then return and cross over the cut line to
achieve a square corner. Triangular or looped overcuts are commonly used.
2. Use the CNC corner slowdown function to hold torch height as it enters and leaves
the corner. As the speed decreases, the arc voltage will increase, driving the torch
down, so corner slowdown will lock out the height controller during the corner cut,
keeping the torch at the programmed height, regardless of arc voltage variations.
Piercing
Piercing causes the molten metal to form a puddle on top of the plate. On thicker plate,
pierce height is calculated to keep the torch away from the plate so that the molten metal does
not adhere to the consumable parts and shorten parts life. Hold pierce height as the cutting
table starts movement to allow the torch to clear the pierce puddle before moving to cut height.
Using the Inova height controller, this is done using the Set Pierce Time function on the edit
screen.
Lead-in and lead-out
Lead-in and lead-out should be calculated to allow the torch to move to cut height
before starting the final piece contour of the cut and to move away from the final piece before
beginning end of cut current ramp down.
Lead-out
Overcut
Corner
Pierce
Lead-in
page 1