10 maintenance overrides – Rockwell Automation 8000 Series TMR System User Manual
Page 16
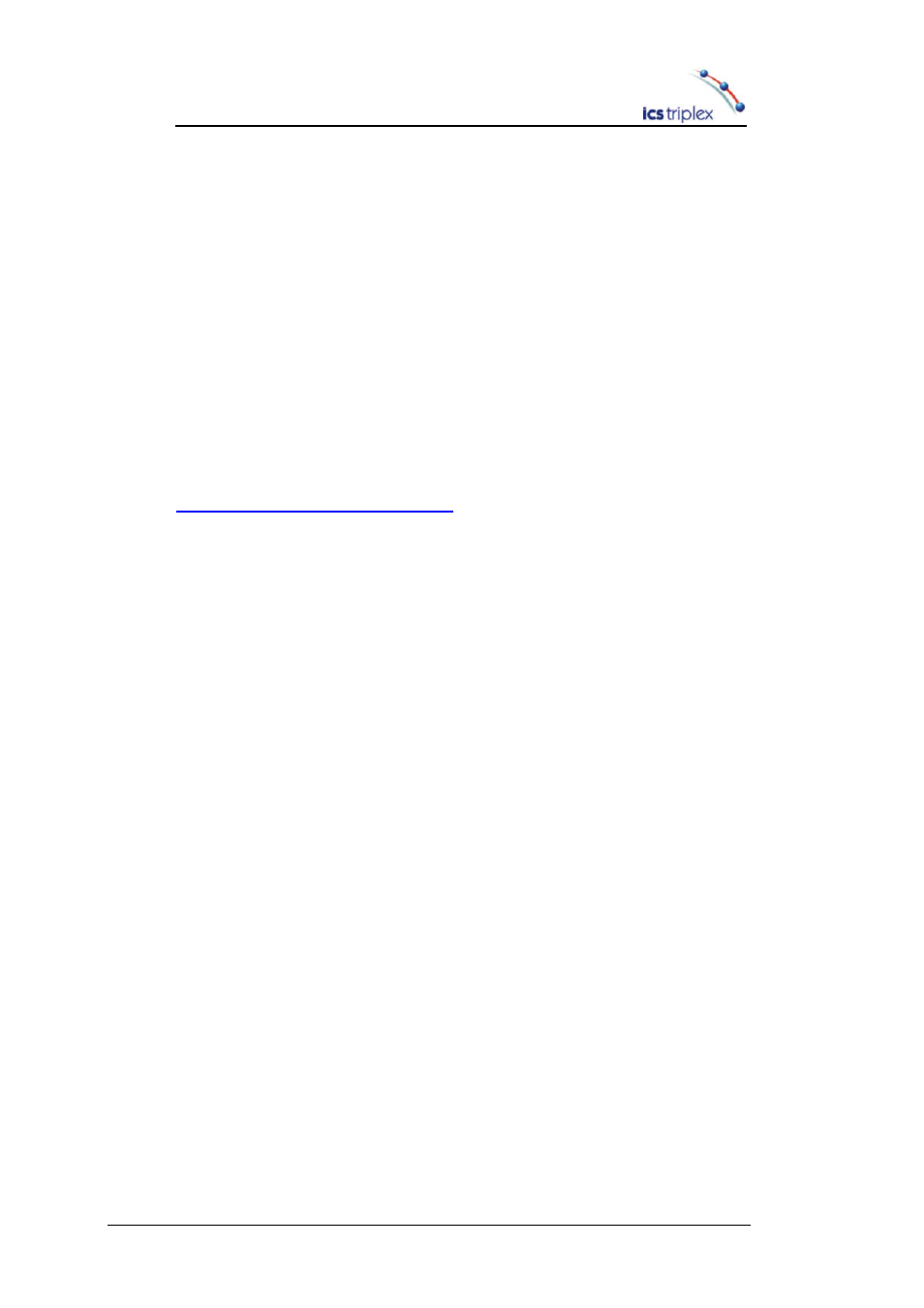
OPERATOR AND MAINTENANCE MANUAL
D o c N o 5 5 2 8 6 4
P a g e 6 o f 2 2
I s s u e 0 2 J u n e 2 0 0 4
1.10 MAINTENANCE OVERRIDES
Maintenance Overrides set inputs or outputs to a defined state that can be
different from the real state during safety operation. They are used during
maintenance, usually to override input or output conditions in order to perform a
periodic test, calibration, or repair of a module, sensor or actuator.
To correctly implement a maintenance override scheme within the TMR
Controller
the override, or ‘bypass’ logic shall be programmed within the Application Program,
with a separate set of safety-related input points or variables enabling the bypass
logic.
In order to accommodate maintenance overrides safely, TÜV has
documented a set of principles that shall be followed. These principles are
published in the document "Maintenance Override" by TÜV Süddeutschland /
TÜV Product Service GmbH and TÜV Rheinland.
http://www.tuvasi.com/modr_3_d.htm
There are two basic methods now used to check safety-related peripherals
connected to the TMR system
:
1. Special switches connected to conventional system inputs. These inputs are
used to deactivate sensors and actuators during maintenance. The
maintenance condition is handled as part of the system’s application
program.
2. Sensors and actuators are electrically switched off during maintenance and
are checked manually.
In some installations, the maintenance console may be integrated with the operator
display, or maintenance may be covered by other strategies.