Setup, Chapter, Chapter objectives – Rockwell Automation 4100 ALEC AXIS LINK ENCODER CONVERTER User Manual
Page 35: Setting the rotary switches
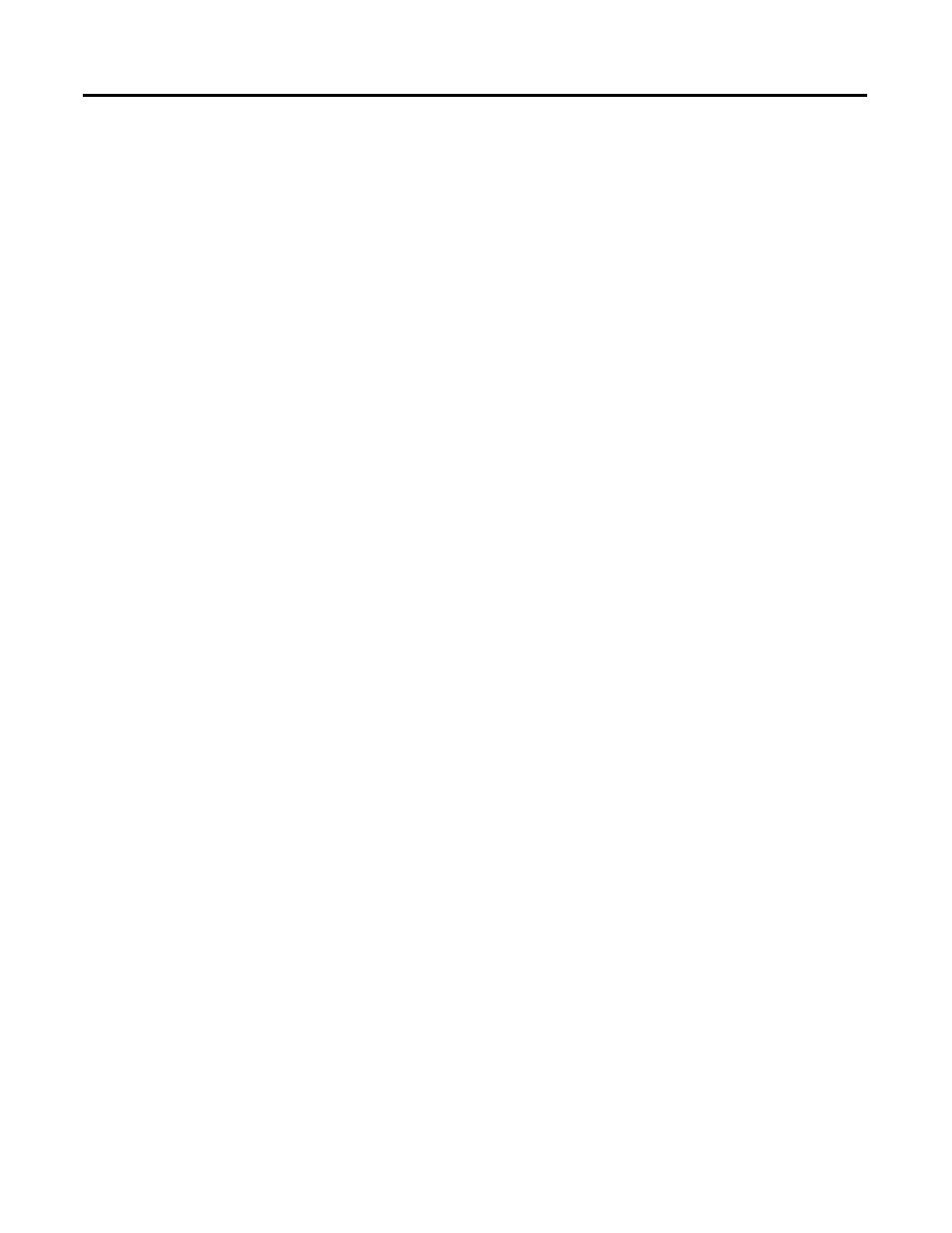
27
Publication 4100-5.3 - June 1999
Chapter
3
Setup
Chapter Objectives
The ALEC is used in conjunction with the 1394 GMC System or the S
Class Compact motion controller and an encoder. It is not a
stand-alone product and must be configured to work with the
hardware connected to it. This involves specific steps that are
determined by the make and model of the hardware connected to the
ALEC. This manual assumes that the GML Commander v4.01 or higher
software is used.
This chapter covers :
•
Setting the Mode rotary switch.
•
Setting the AxisLink Address rotary switch.
•
Setting the DIP Switches.
•
Powering the ALEC.
•
Configuring the ALEC with the GML Commander software.
•
Compatible Allen-Bradley Encoder settings.
Setting the Rotary Switches
There are two rotary switches located on the front panel of the ALEC.
These are used for setting the Mode (frequency) and AxisLink Address
(node). You must set these switches before powering the ALEC.
Selecting the Operation Mode
The Mode selector switch on the front panel of the ALEC selects the
axis position update rate; the periodic rate at which the ALEC can
broadcast encoder position information onto the AxisLink
communication network.
The mode switch is a 16-position rotary switch. Select an axis position
update rate that is the same as the motion controller’s servo rate. For
example:
If your motion system servo rate is 500Hz , select position 4 on the
mode switch with a small flat-head screw driver. At this setting, the
ALEC updates position information 500 times per second.